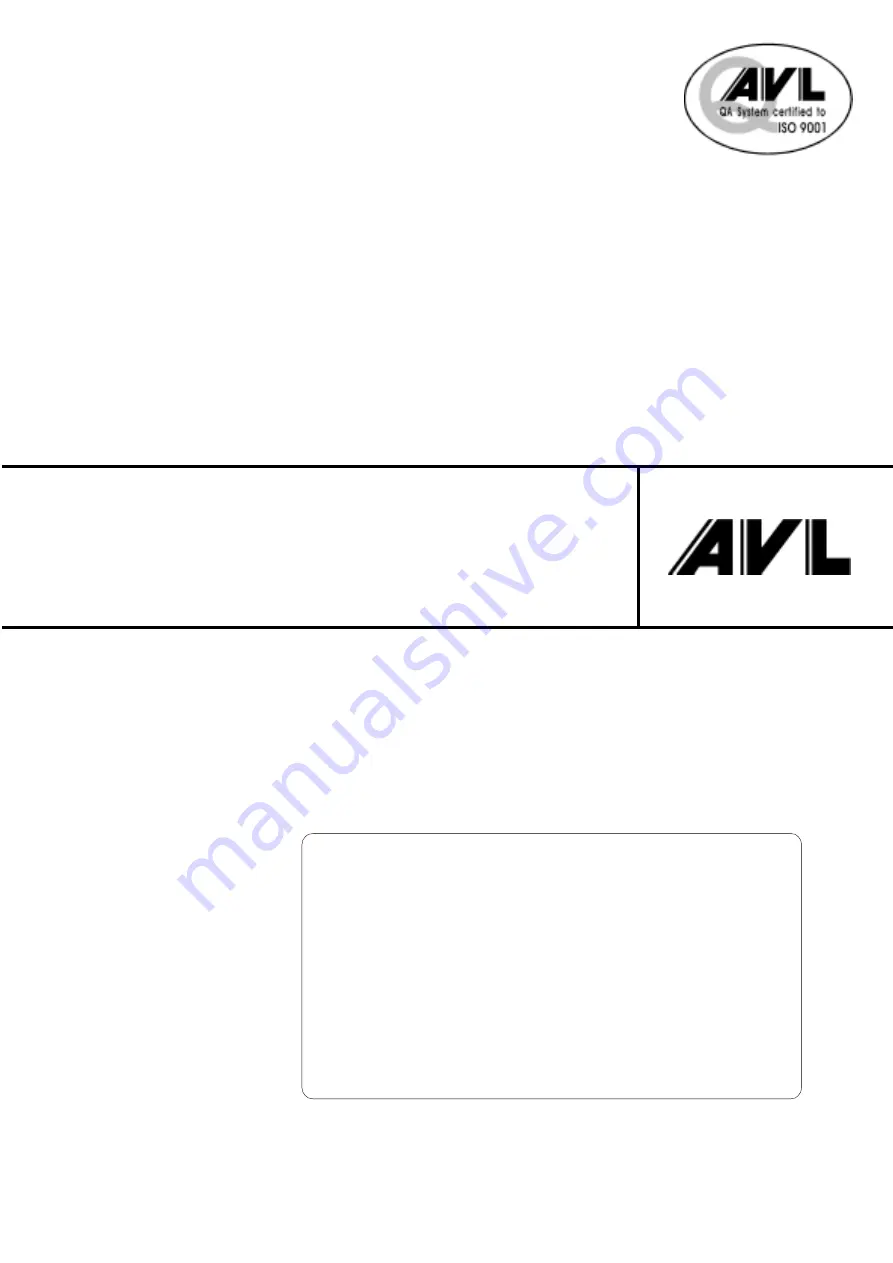
ENGINE DIAGNOSTICS
AVL LIST GMBH
Hans-List-Platz 1
A-8020 Graz / Austria
Phone: +43 316 787-0
Fax: +43 316 787-550
http://www.avl.com
Ident. number:
AT0391E
Revision no.:
04
Edition:
January 1999
Subject to alteration
Printed in Austria by
AVL LIST GMBH Graz
Service Manual
AVL DiGas 4000
AVL DiCom 4000
AVL DiSmoke 4000
Summary of Contents for AVL DiCom 4000
Page 4: ......
Page 6: ......
Page 22: ...Periodic Maintenance AVL 4000 1 12 Service Manual ...
Page 47: ...4000 Evaluation Unit Service Manual 4 15 4 9 Main Board 4 9 1 Components Location Diagram ...
Page 48: ...Evaluation Unit AVL 4000 4 16 Service Manual 4 9 2 Circuit Diagrams ...
Page 49: ...4000 Evaluation Unit Service Manual 4 17 ...
Page 50: ...Evaluation Unit AVL 4000 4 18 Service Manual ...
Page 51: ...4000 Evaluation Unit Service Manual 4 19 ...
Page 52: ...Evaluation Unit AVL 4000 4 20 Service Manual ...
Page 54: ...Evaluation Unit AVL 4000 4 22 Service Manual 4 10 2 Circuit Diagrams ...
Page 55: ...4000 Evaluation Unit Service Manual 4 23 ...
Page 56: ...Evaluation Unit AVL 4000 4 24 Service Manual ...
Page 57: ...4000 Evaluation Unit Service Manual 4 25 ...
Page 59: ...4000 Evaluation Unit Service Manual 4 27 4 11 2 Circuit Diagram ...
Page 61: ...4000 Evaluation Unit Service Manual 4 29 4 12 2 Circuit Diagram ...
Page 63: ...4000 Evaluation Unit Service Manual 4 31 4 13 2 Circuit Diagram ...
Page 65: ...4000 Evaluation Unit Service Manual 4 33 4 14 2 Circuit Diagram ...
Page 67: ...4000 Evaluation Unit Service Manual 4 35 4 15 2 Circuit Diagram ...
Page 69: ...4000 Evaluation Unit Service Manual 4 37 4 16 2 Circuit Diagram ...
Page 71: ...4000 Evaluation Unit Service Manual 4 39 4 17 2 Circuit Diagram ...
Page 73: ...4000 Evaluation Unit Service Manual 4 41 4 18 2 Circuit Diagram ...
Page 75: ...4000 Evaluation Unit Service Manual 4 43 4 19 2 Circuit Diagram ...
Page 77: ...4000 Evaluation Unit Service Manual 4 45 4 20 2 Circuit Diagram ...
Page 79: ...4000 Evaluation Unit Service Manual 4 47 4 21 2 Circuit Diagram ...
Page 124: ...4 5 Gas Measuring Instruments Unit AVL 4000 5 28 Service Manual ...
Page 149: ...4000 Opacity Measuring Chamber Type A Service Manual 6 25 Fig 6 30 Fig 6 31 ...
Page 150: ...Opacity Measuring Chamber Type A AVL 4000 6 26 Service Manual Fig 6 32 ...
Page 180: ...Spare Parts Lists AVL 4000 8 14 Service Manual ...
Page 182: ...Tools for the Service Technician AVL 4000 9 2 Service Manual ...