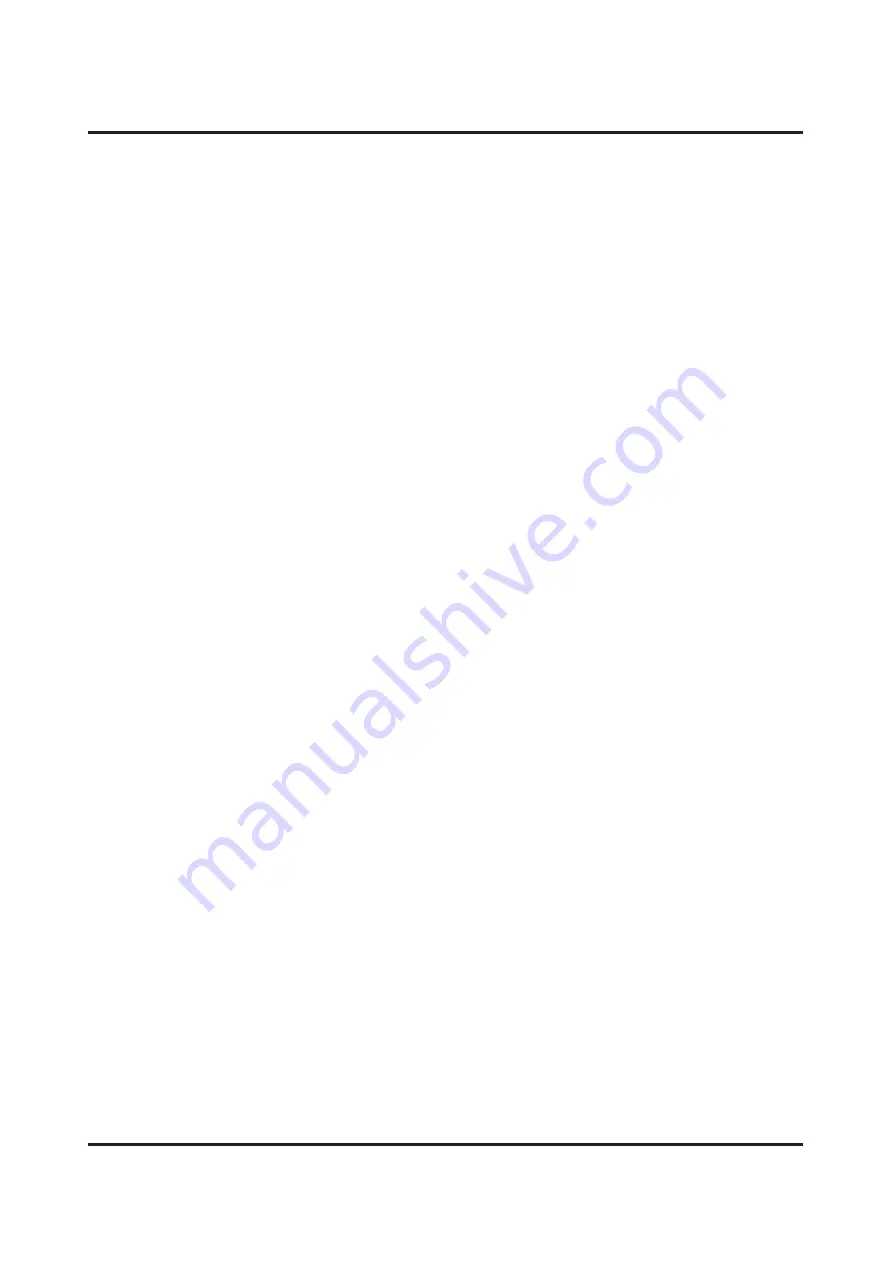
INDEX
42
Tab Sensor
Automatic Adjustment
19
Manual Adjustment
21
Tab/Stamp
Automatic Positioning
27
Clearing
31
Loading
8
Manual Positioning
23
Tabber
Adjusting
10
Advanced
14
Job#
13
Mode
13
Operating
8
Pass-Thru Operate
13
Pre-programmed Job
15
Programming
17
Start-Up
13
Take-up Reel
1
Troubleshooting
33
Jams
33
Stamp Placement Problems
35
Tab Placement Problems
33
Tabber Operation
36
V
V-Tab
Automatic Adjustment
19
Manual Adjustment
21