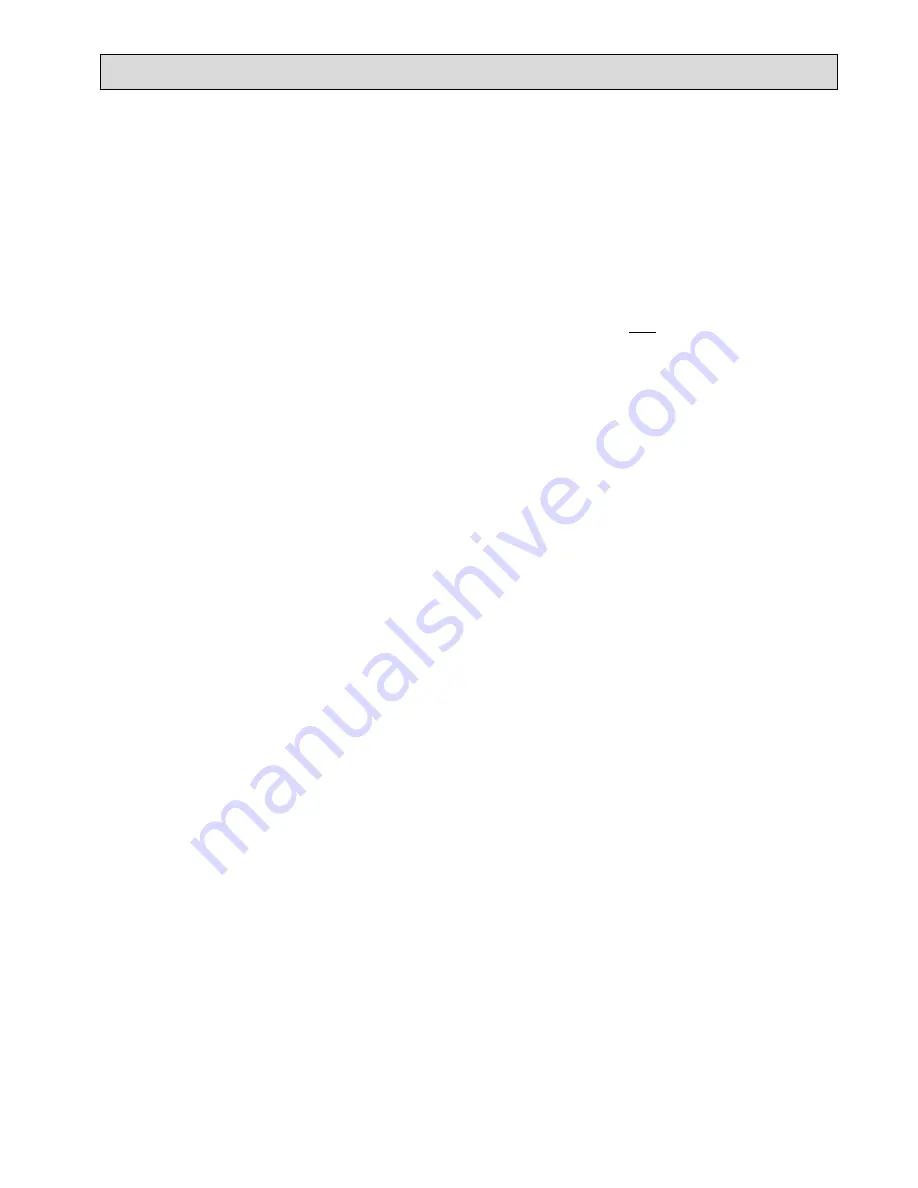
April 2011
Section 6 Maintenance
Page 6 – 2
Amerex Restaurant Fire Suppression System (EX 4658)
7.
The Pneumatic Release Module (PRM) o-ring (P/N 17692) on the brass actuation piston must be
replaced every six months.
a.
Materials required: 1 1/8” open-end wrench, 5/32” Allen wrench, clean, lint-free shop towels,
o-ring (P/N 17692), and Visilox lubricant (available as p/n 06247 in a 5 oz. tube).
b.
Remove the cover of the PRM and make sure the nitrogen actuation cylinder is removed.
Remove the screw anchoring the spring to the brass block with a 5/32” Allen wrench. The
silver lever should now swing down away from the brass block.
c.
Unscrew the cap off of the Schrader valve and bleed the pressure off of the accumulator
cylinder. Confirm that the pressure gauge reads zero.
d.
With the 1 1/8” open-end wrench, loosen and remove the brass hex nut that retains the piston
spring and piton inside the brass block. A shop towel may be required to grip the end of the
brass piston for extraction from the block. Take care to use only your hands to remove the
piston.
VERY IMPORTANT: DO NOT use pliers or tools to remove the piston from the
bore or the o-ring from the piston groove. Scratches will cause system leaks and
unwanted system discharges.
e.
With a clean shop towel, wipe out all the old grease from the inside the cylindrical bore at the
deepest point inside the brass block. Using the Visilox V-711 lubricant,
thoroughly and
completely
wipe the internal bore in a circular motion with a clean finger. Make sure that
you reach all the way to the rear of the bore with the lubricant.
f.
Clean off the old grease from the piston o-ring. Using a dry shop towel, ‘pinch’ the o-ring until
it can be slipped over the end of the piston by hand.
DO NOT
use a sharp instrument to
remove or cut the old o-ring off of the piston – scratches on the brass will create a leak point.
Clean the groove of the piston prior to installing the new o-ring. Liberally lubricate the o-ring
on the piston with Visilox before inserting into the brass block.
g.
VERY IMPORTANT
–
Lubricate both the o-ring and the internal bore! Use NO TOOLS to
remove the old o-ring.
h.
After inserting the new piston all the way into the bore, slide the spring over the end and re-
tighten the brass hex retaining nut until resistance is felt. Do not over-tighten, as spring
tension will present the nut from backing out.
i.
Temporarily pressurize accumulator through the Schrader valve with approximately 40-50
psi. Re-attach the screw which retains the lever spring to the corner of the brass block.
Tighten securely. Latch the tip of the actuation lever under the exposed tip of the piston.
j.
Apply the lube totally around the perimeter of the exposed brass piston tip of the trip
mechanism. Work the piston in and out several times to distribute the lube. Additionally,
place some lube on the tip of the spring-loaded lever where it contacts the underside of the
piston tip.
k.
Re-pressurize to 70 psi and leak check all fittings. Perform a full function test of the PRM at
this time, as well as the remainder of the six month maintenance.
8.
Use the digital thermometer to record the temperatures found at each detector location (with
appliances running) and compare with those temperatures found at the same location during the last
system maintenance. Insufficient air movement, excessive grease build up and appliance changes
can cause temperatures to elevate even to the point of system discharge without a fire occurring.
INCREASING THE TEMPERATURE SETTING OF THE FUSIBLE LINK IS NOT AN ACCEPTABLE
SOLUTION TO THIS PROBLEM
.
9.
The agent cylinder assembly and nitrogen actuation cylinder must be checked for proper pressure
(within the green pie
OPERABLE RANGE
on pressure gauges).
10.
The agent cylinder and all hose assemblies must be hydrostatically tested at a minimum of every 12
years.
a
Agent Cylinder – test to 480 psi (3309 kPa)
b
Actuation Hose (if used) – test to 3500 psi (24131 kPa)
c
Distribution Hose – Test to 480 psi (3309 kPa)
If the agent cylinder or hose assemblies have been subjected to physical damage, excessive heat or
corrosion they should be hydrostatically tested or replaced regardless of their age.