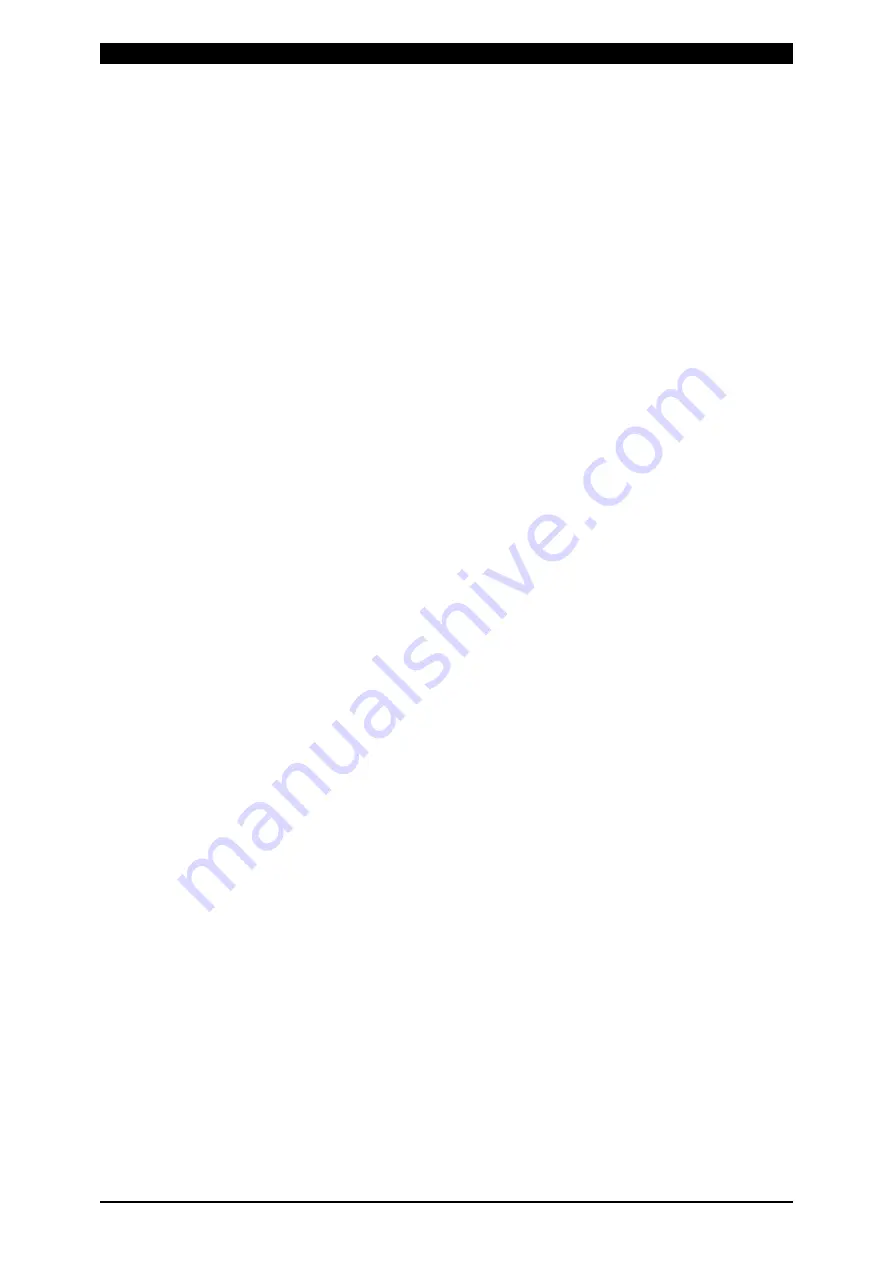
MU-100A
4. Name and Functions of Each Section
4-4
8
RS232C/485 connector: Connects the RS-232C/RS-485.
9
RS485 connector:
Connects the RS-485.
SENSOR3 connector:
Connects the displacement sensor 2. When connecting the
displacement sensor, use the dedicated adapter or extension
cable.
○
11
SENSOR4 connector:
Connects the load cell 2. When connecting the load cell, use
the dedicated extension cable or connector.
○
12
INPUT2 connector:
Connects the input signals of SENSOR3 and 4.
○
13
OUTPUT2 connector:
Connects the output signals of SENSOR3 and 4.