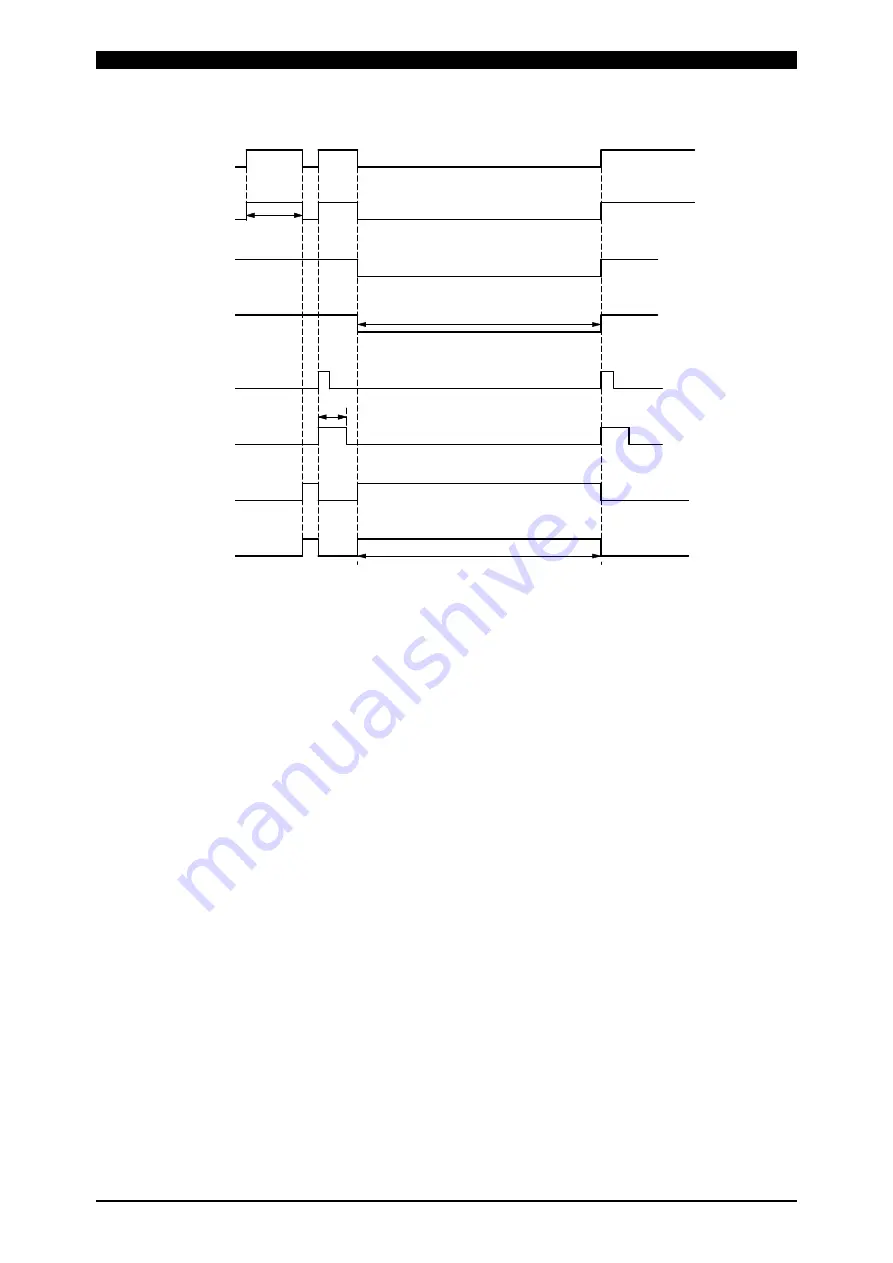
MAWA-300B
6. Timing Chart
6-8
The following a timing chart for option input/output signals (M-READY, H-STOP and H-RESET).
READY出力
通電開始可能状態
M-READY 出力
RESET 入力
H-ERROR入力
ERROR出力
H-RESET 出力
非常停止
H-STOP 出力
*1
*2
*3
*4
*1 The M-READY signal is output when
MAWA-300B
is ready for welding.
*2 When
MAWA-300B
is in an emergency stop status, the H-STOP signal output is turned off. (b contact) The STOP signal is
output after the emergency stop status is cleared.
*3 When
MAWA-300B
receives the RESET input signal, it outputs the H-RESET output signal. The H-RESET signal is output for
the set time of “H-RESET signal output time.”
Refer to “4. (6) Switch Select Screen.”
*4 When
MAWA-300B
receives the H-ERROR signal, it outputs the ERROR signal, being put into an alarm status.
READY output
welding start enable status
M-READY output
Emergency stop
H-STOP output
RESET input
H-RESET output
H-ERROR input
ERROR output