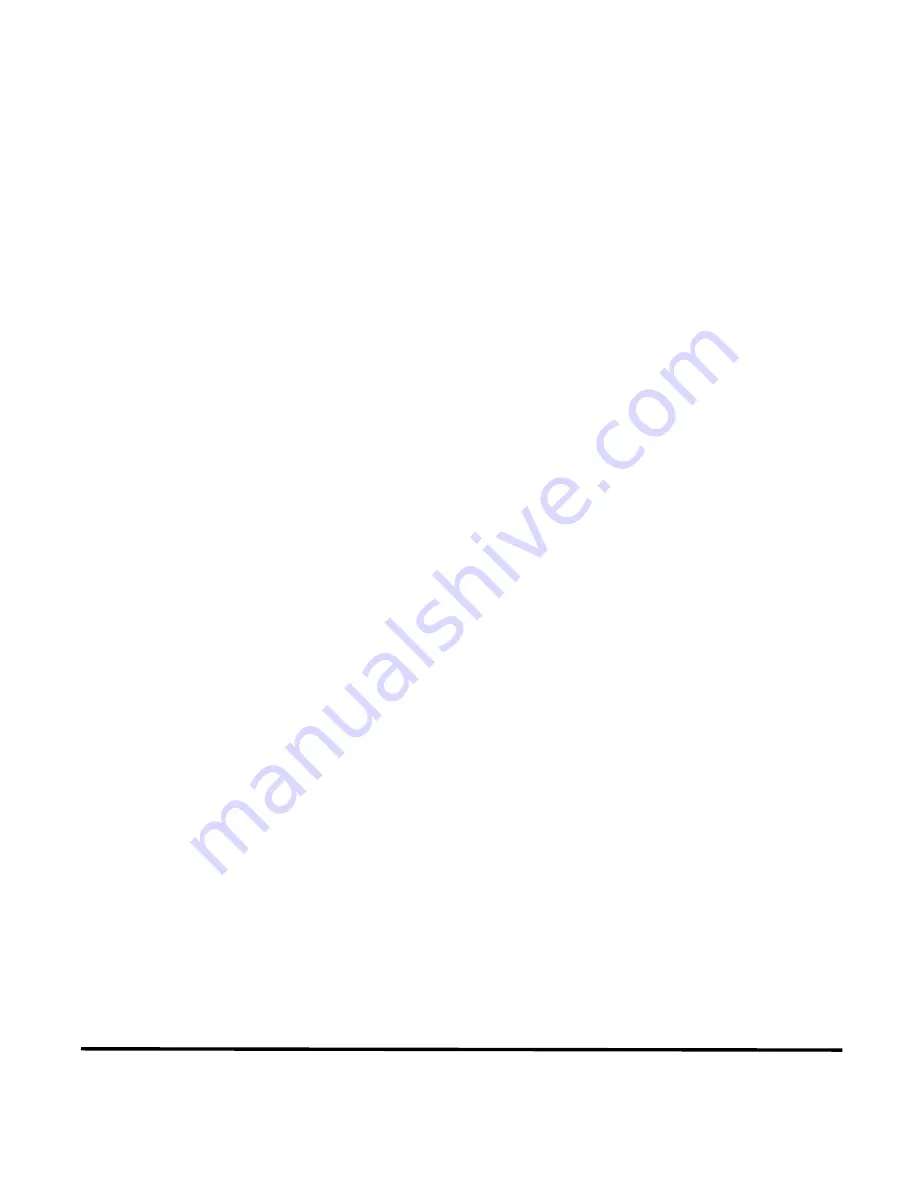
2 KHZ INVERTER WEDLING POWER SUPPLY
990-057
H-1
APPENDIX H
Quality Resistance Welding Solutions:
Defining the Optimum Process
Introduction
A quality resistance welding solution both meets the application objectives and produces stable, repeatable
results in a production environment. In defining the optimum process the user must approach the
application methodically and consider many variables. In this article we will look at the following key
stages and principles to be considered when defining the optimum resistance welding process:
•
Materials and their properties
•
Basic resistance welding
•
principles
•
Weld profiles
•
Approach to development
•
Common problems
•
Use of screening DOE’s
•
Use of factorial DOE’s
Resistance Welding -- A Material World
The first consideration in designing a quality welding solution is the properties of the materials to be
joined and the quality requirements of the desired welded joint. At this stage, it is worthwhile to review
the way the resistance welding process works and the likely outcome when the parts are resistance welded.
There are four main types of structural materials:
•
Metals (silver, steel, platinum)
•
Ceramic (alumina, sand)
•
Plastics/polymers (PVC, teflon)
•
Semiconductors (silicon, geranium)
Of these, only metals can be resistance welded because they are electrically conductive, soften on heating,
and can be forged together without breaking.