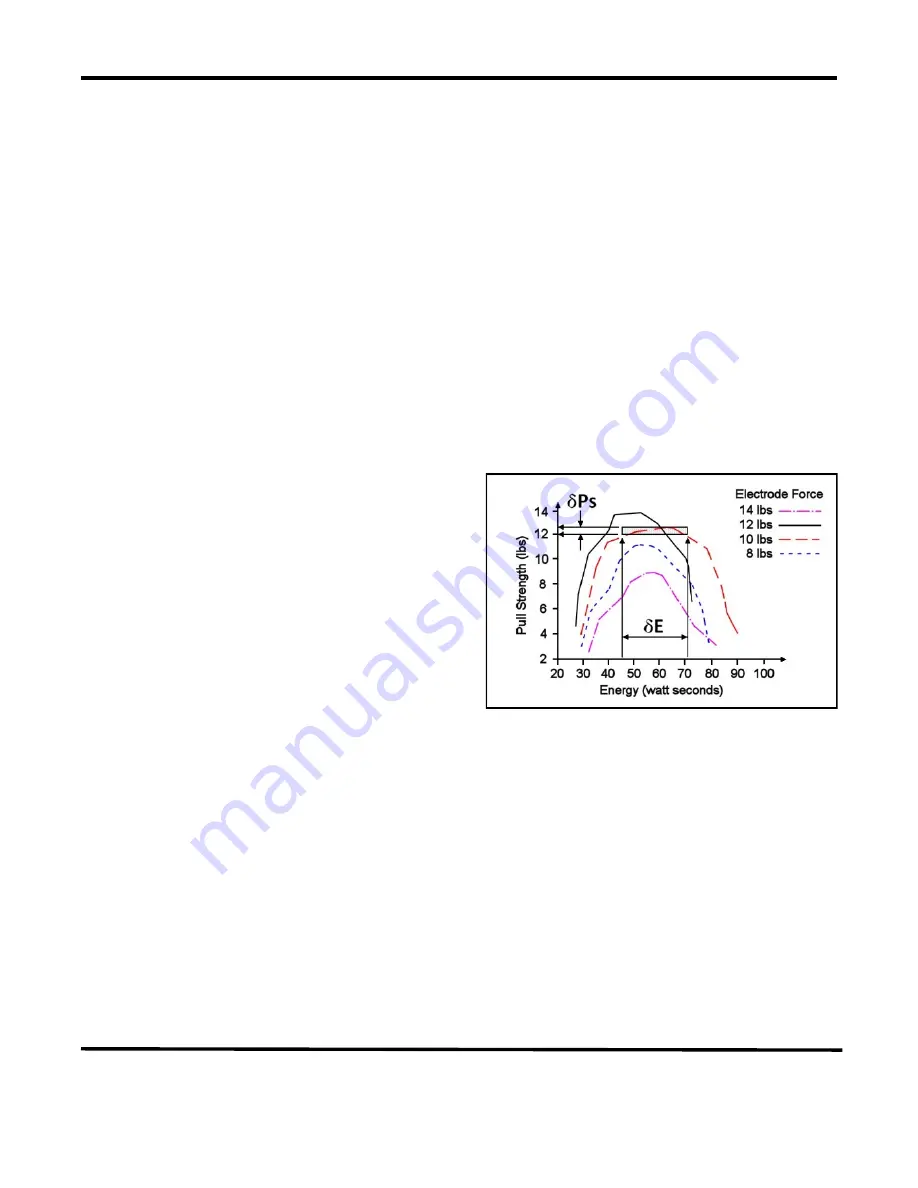
APPENDIX G: THE BASICS OF RESISTANCE WELDING
2 KHZ INVERTER WEDLING POWER SUPPLY
G-6
990-057
Weld Strength Profiles
Creating a weld strength profile offers the user a scientific approach to determining the optimum set of
welding parameters and then displaying these parameters in a graphical form.
1
Start at a low weld current, voltage, or power, making five or more welds, then perform pull tests
for each weld. Calculate the average pull strength. Increase weld current, voltage, or power and
repeat this procedure. Do not change the weld time, weld force, or electrode area.
2
Continue increasing weld current, voltage, or power until any unfavorable characteristic occurs,
such as sticking or spitting.
3
Repeat steps 1 through 3 for different weld forces, then create a plot of part pull strength versus
weld current, voltage, or power for different weld forces as shown in the illustration below,
Typical Weld Strength Profile
.
4
Repeat steps 1 through 3 using a different but fixed weld time.
Typical Weld Strength Profile
The picture on the right illustrates a typical weld
strength profile. The 14 lb. electrode force curve
shows the highest pull strengths but the lowest
tolerance to changes in weld current, voltage, or
power. The 12 lb. electrode force curve shows a
small reduction in pull strength, but considerably
more tolerance to changes in weld energy. Weld heat
will vary as a result of material variations and
electrode wear.
The 12 lb. electrode force curve is preferred. It
shows more tolerance to changes in weld current,
voltage, or power and has nearly the same bond
strength as the 14 lb. electrode force curve.
A comparison of weld schedules for several different
applications might show that they could be
consolidated into one or two weld schedules. This
would have obvious manufacturing advantages.
Typical Weld Strength Profile