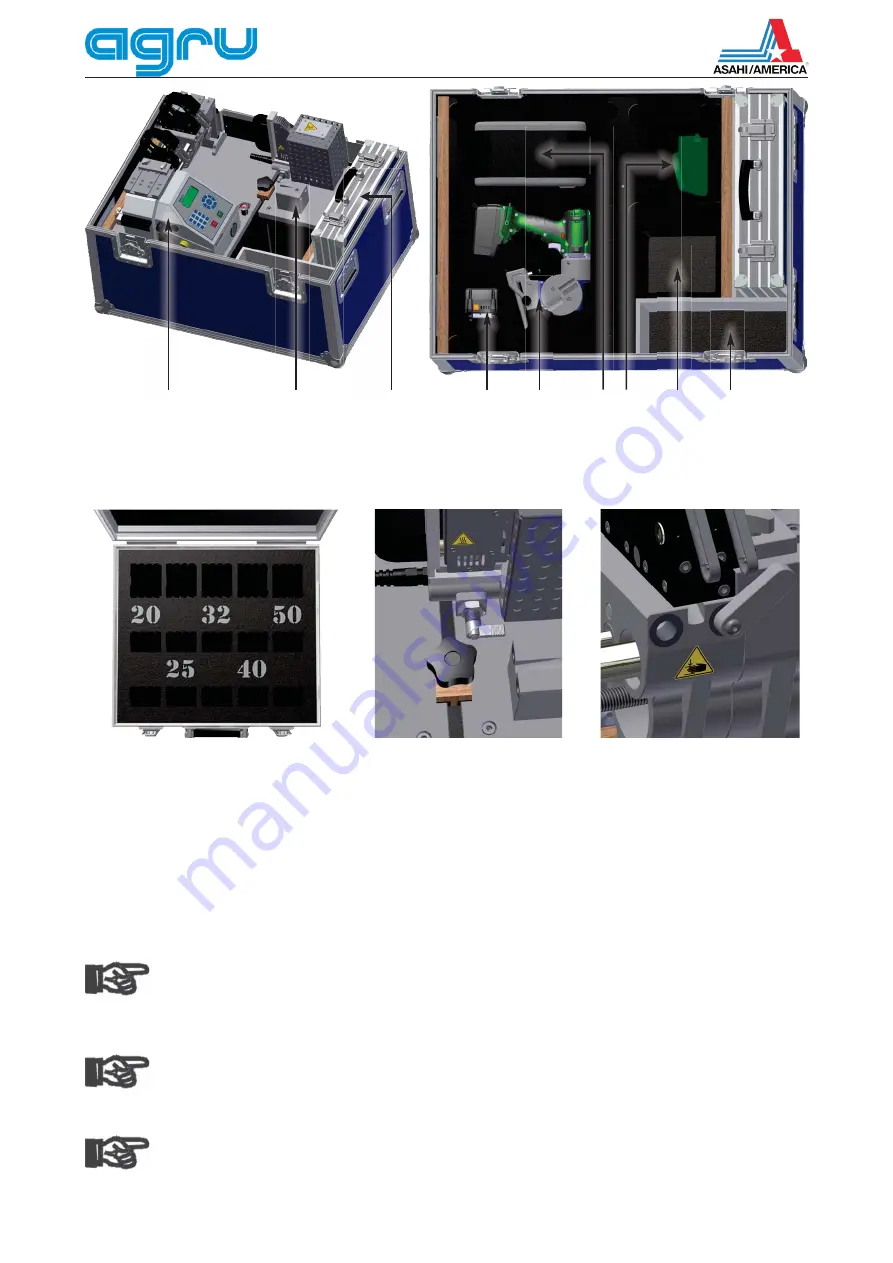
Version October 2014
12
EN
agru SP 63-mobile User’s Manual
Inside view of the case for the
reducer inserts
Star knob securing the base
and tabletop plates, and
transport lock (self-locking
pin) of heating element
Transport lock of facing tool/
heating element carrier and
movable carriage (locking ball
pin on the back to unlock
locking bar)
may have to be repositioned or removed. To do so, loosen the locking
thumb screws and either remove the clamp or re-adjust it and secure it
by tightening the locking screws again.
If the diameter of the pieces to be welded is smaller than the clamp, insert
the reducer inserts. This can be done without using any tools since the
inserts are fastened in the clamps by magnetic attraction.
Important
Pipe clamps and reducer inserts have to be clean or must be
cleaned before welding starts. To insert or remove the inserts,
do not use heavy tools (hammer, wrench). They may damage
the inserts and the magnets.
Important
The surfaces of the heating plate have to be free of grease and
clean, or they have to be cleaned. Clean the heating element
only when it is cold. Refer to a service point for detailed infor-
mation on the procedures for cleaning the heating element.
Important
Make sure all connectors are tight in their sockets and make
sure that the machine is operated only if the conditions for safe
and intended use are met (see also section 2).
Mechanics and
Electronics on Base
Plate
Tabletop Plate with
Heating Element in it
Guard
Case with
Reducer
Inserts
Second Battery
for Facing
Tool
Box for
Accessories
Box for
Extension Cord
and User's
Manual
Facing T
ool
Label T
ag
Printer
Charger for Fac-
ing T
ool
Battery