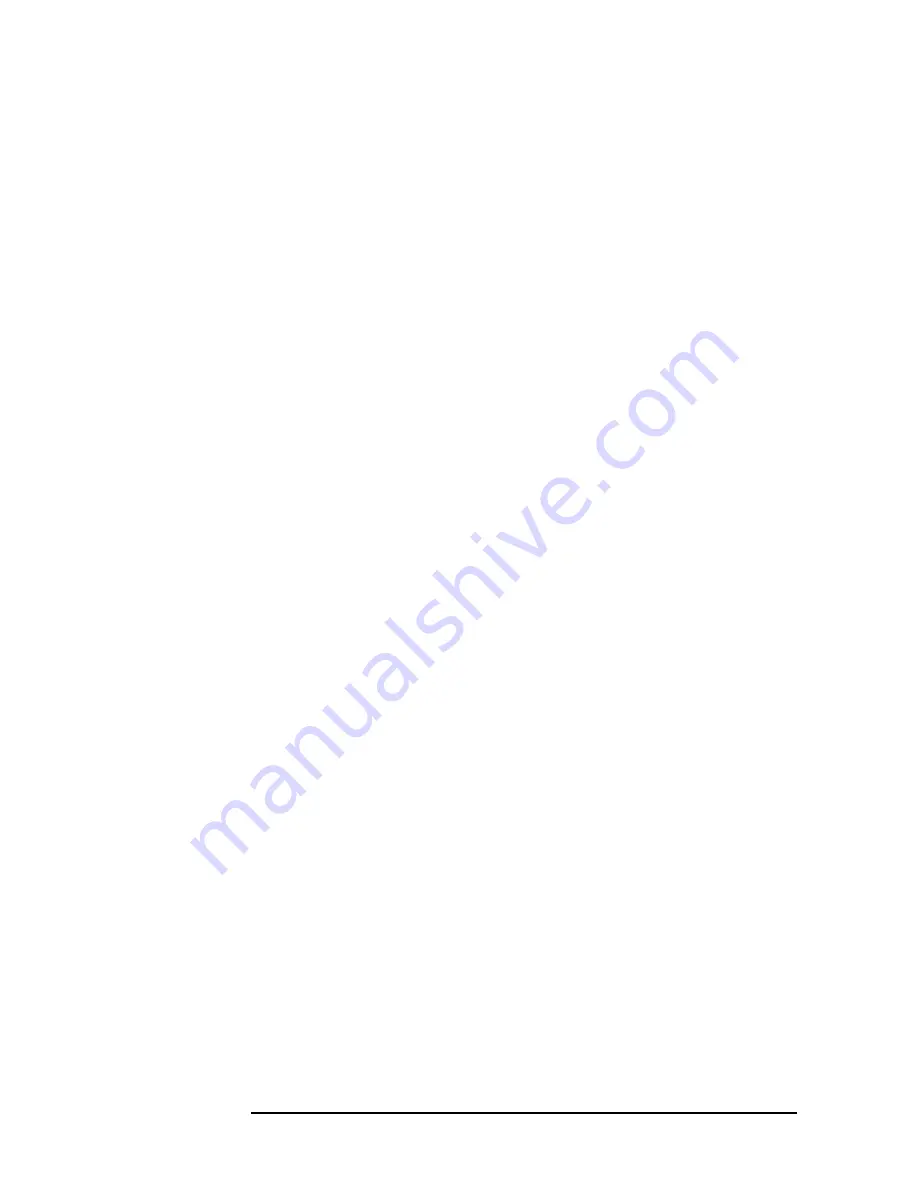
356
Chapter 7
General Troubleshooting
Block Diagram Description
A13 Second Converter
The A13 second converter down-converts the 3.9107 GHz 1st IF
(low-band and millimeter band) to a 310.7 MHz 2nd IF. In the
microwave band, it passes the 310.7 MHz 1st IF from the A10
YIG-tuned filter/mixer to the A15 RF assembly. The converter
generates a 3.6 GHz second LO by multiplying a 600 MHz reference.
Bandpass filters remove unwanted harmonics of the 600 MHz driving
signal. 1st IF and 2nd LO signals are filtered by cavity filters.
Second IF Amplifier (part of A15)
The second IF amplifier (SIFA) amplifies and filters the second IF.
Access to this pre-filtered signal is available at the rear panel 2ND IF
OUTPUT (Option 001 only).
The external mixing input from the front panel IF INPUT connector is
also directed through the SIFA. A dc bias is placed onto the IF INPUT
line for biasing external mixers.
Third Converter (part of A15)
The third converter down-converts the 310.7 MHz IF to 10.7 MHz. A
PIN-diode switch selects the LO signal used. For normal operation, a
300 MHz LO signal is used. The signal is derived from the 600 MHz
reference PLL. During signal identification (SIG ID ON), the 298 MHz
SIG ID oscillator is fed to the double balanced mixer on alternate
sweeps.
Flatness Compensation Amplifiers (part of A15)
The flatness compensation amplifiers amplify the output of the
double-balanced mixer. The variable gain of the amplifier (0 to 45 dB)
compensates for flatness variations within a band. Band conversion loss
is compensated by step gain amplifiers in the IF section.
Control for the amplifiers originates from two DACs on the A3 Interface
assembly. (DAC values are interpolated approximately every 17 MHz
based on data obtained during the frequency response adjustment.) The
flatness-compensation control circuitry on A15 converts the RF GAIN
voltage, from A3, into two currents: RF GAIN1 and RF GAIN2. These
currents drive PIN diodes in the flatness compensation amplifiers.
Summary of Contents for 8564EC
Page 17: ...25 1 General Information ...
Page 37: ...47 2 Adjustment Diagnostic Software ...
Page 77: ...89 3 Manual Adjustment Procedures ...
Page 129: ...161 3a Manual Adjustment Procedures 3335A Source not Available ...
Page 142: ...175 4 Assembly Replacement ...
Page 194: ...Chapter 4 257 Assembly Replacement Procedure 13 A21 OCXO Figure 4 34 A21 OCXO Mounting Screws ...
Page 196: ...259 5 Replaceable Parts ...
Page 218: ......
Page 219: ......
Page 220: ......
Page 221: ......
Page 222: ......
Page 223: ......
Page 224: ...303 6 Major Assembly and Cable Locations ...
Page 234: ...315 7 General Troubleshooting ...
Page 238: ...Chapter 7 319 General Troubleshooting Introduction Figure 7 2 Ribbon Cable Connections 1 of 3 ...
Page 239: ...320 Chapter7 General Troubleshooting Introduction Figure 7 3 Ribbon Cable Connections 2 of 3 ...
Page 242: ...Chapter 7 323 General Troubleshooting Introduction Figure 7 5 Service Cal Data Menu ...
Page 271: ...352 Chapter7 General Troubleshooting Block Diagram Description Figure 7 6 Functional Sections ...
Page 283: ...364 Chapter7 General Troubleshooting Block Diagram Description ...
Page 284: ......
Page 285: ......
Page 286: ......
Page 287: ...377 8 ADC Interface Section ...
Page 291: ...Chapter 8 381 ADC Interface Section Introduction Figure 8 2 A3 Test Connector Pin Locations ...
Page 321: ......
Page 322: ...427 9 IF Section ...
Page 356: ...Chapter 9 461 IF Section A5 IF Assembly Figure 9 13 Detailed IF Adjust Signature 5 ...
Page 376: ......
Page 377: ......
Page 378: ......
Page 379: ...487 10 Controller Section ...
Page 394: ...521 11 Synthesizer Section ...
Page 451: ......
Page 452: ......
Page 453: ......
Page 454: ...593 12 RF Section ...
Page 489: ...628 Chapter12 RF Section A15 RF Assembly Figure 12 10 10 MHz TTL Reference at U304 Pin 13 ...
Page 491: ......
Page 492: ...633 13 Display Power Supply Section ...
Page 504: ......
Page 505: ...671 14 Component Level Information Packets ...
Page 507: ......