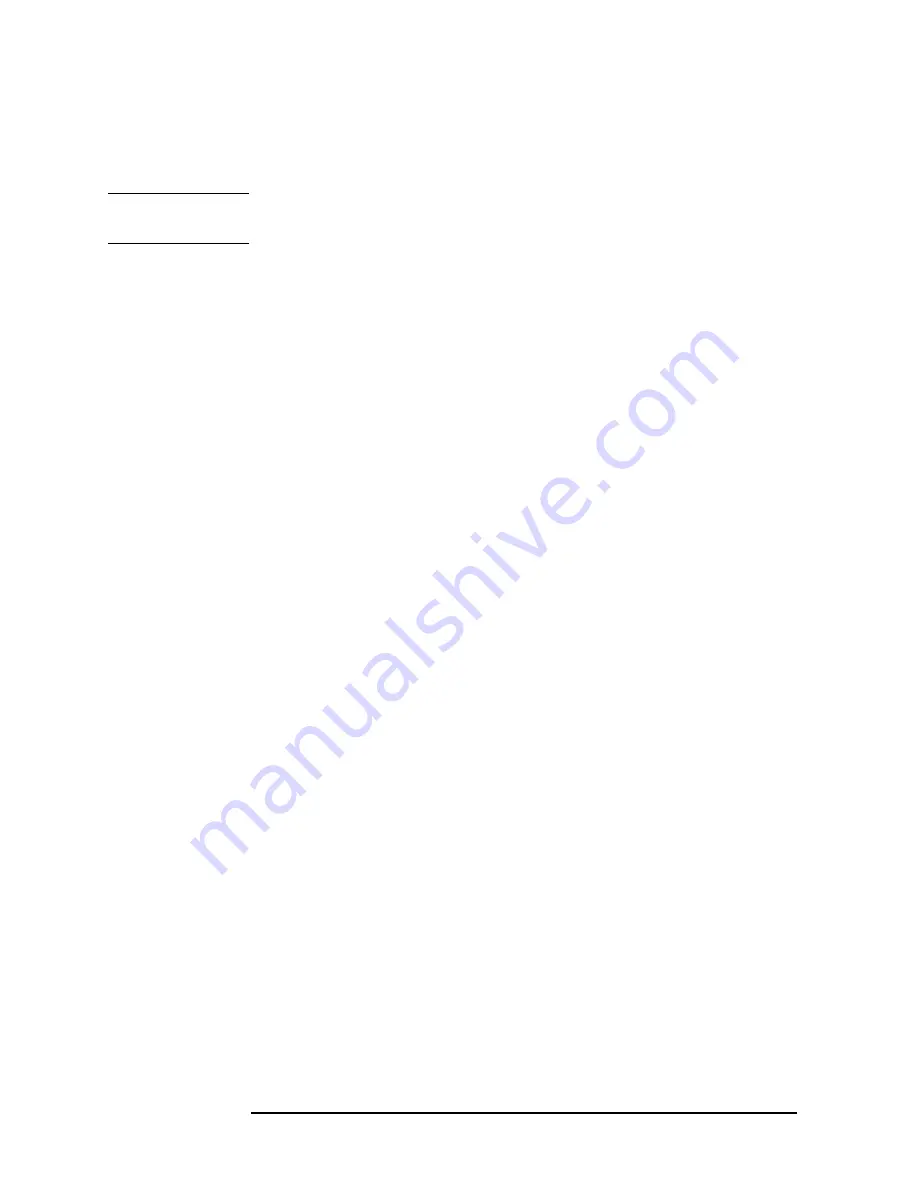
624
Chapter 12
RF Section
A15 RF Assembly
b. For maximum gain (flatness data equals 0), RF GAIN (A15U909
pin 10) should be at approximately 0 Vdc and the current through
each attenuator section should be close to 0 mA.
CAUTION
As long as the flatness data just entered is not stored, the
previously-stored flatness data will be present after the power is cycled.
14.Move the WR PROT/WR ENA jumper on the A2 controller assembly
to the WR PROT position.
15.Reconnect the cable to A15J801.
Flatness Compensation Control
Refer to function block G on A15 RF Section Schematic Diagram in the
8560 E-Series Spectrum Analyzer Component Level Information.
The Flatness Compensation Control consists of a buffer amp (U909C)
and two identical voltage-to-current converters (U909B and U909D).
The thermistor RT901 in the buffer amp provides temperature
compensation for the PIN diodes in the gain stages and the SAW filters.
PIN Switch Drivers
Refer to function block H on A15 RF Section Schematic Diagram in the
8560 E-Series Spectrum Analyzer Component Level Informatio
n.
The control latches control the PIN Switch Drivers illustrated in
Function Block I.
1. Connect the positive lead of a DVM to A15J901 pin 15 (HEXTMIX).
Connect the negative lead to A15J901 pin 6. The measured signal
controls the switching between internal and external IF signals.
2. On the spectrum analyzer, press
AUX CTRL
and
EXTERNAL MIXER
.
The voltage on the DVM should measure approxi5 Vdc (TTL
high).
3. On the spectrum analyzer, press
AUX CTRL
and
INTERNAL MIXER
.
The voltage on the DVM should measure approximately 0 Vdc (TTL
low).
4. Connect the DVM positive lead to A15J901 pin 13 (LSID). The signal
measured turns on the SIG ID oscillator.
5. On the spectrum analyzer, press
SIG ID ON
(if present),
SGL SWP
.
6. Subsequent pushes of
SGL SWP
should cause the signal measured on
the DVM to toggle between TTL high and low levels.
7. Connect an oscilloscope probe to A15U902 pin 7 (LRDIR) and the
probe ground lead to A15J901 pin 6. The signal measured controls
the flatness compensation circuit.
Summary of Contents for 8564EC
Page 17: ...25 1 General Information ...
Page 37: ...47 2 Adjustment Diagnostic Software ...
Page 77: ...89 3 Manual Adjustment Procedures ...
Page 129: ...161 3a Manual Adjustment Procedures 3335A Source not Available ...
Page 142: ...175 4 Assembly Replacement ...
Page 194: ...Chapter 4 257 Assembly Replacement Procedure 13 A21 OCXO Figure 4 34 A21 OCXO Mounting Screws ...
Page 196: ...259 5 Replaceable Parts ...
Page 218: ......
Page 219: ......
Page 220: ......
Page 221: ......
Page 222: ......
Page 223: ......
Page 224: ...303 6 Major Assembly and Cable Locations ...
Page 234: ...315 7 General Troubleshooting ...
Page 238: ...Chapter 7 319 General Troubleshooting Introduction Figure 7 2 Ribbon Cable Connections 1 of 3 ...
Page 239: ...320 Chapter7 General Troubleshooting Introduction Figure 7 3 Ribbon Cable Connections 2 of 3 ...
Page 242: ...Chapter 7 323 General Troubleshooting Introduction Figure 7 5 Service Cal Data Menu ...
Page 271: ...352 Chapter7 General Troubleshooting Block Diagram Description Figure 7 6 Functional Sections ...
Page 283: ...364 Chapter7 General Troubleshooting Block Diagram Description ...
Page 284: ......
Page 285: ......
Page 286: ......
Page 287: ...377 8 ADC Interface Section ...
Page 291: ...Chapter 8 381 ADC Interface Section Introduction Figure 8 2 A3 Test Connector Pin Locations ...
Page 321: ......
Page 322: ...427 9 IF Section ...
Page 356: ...Chapter 9 461 IF Section A5 IF Assembly Figure 9 13 Detailed IF Adjust Signature 5 ...
Page 376: ......
Page 377: ......
Page 378: ......
Page 379: ...487 10 Controller Section ...
Page 394: ...521 11 Synthesizer Section ...
Page 451: ......
Page 452: ......
Page 453: ......
Page 454: ...593 12 RF Section ...
Page 489: ...628 Chapter12 RF Section A15 RF Assembly Figure 12 10 10 MHz TTL Reference at U304 Pin 13 ...
Page 491: ......
Page 492: ...633 13 Display Power Supply Section ...
Page 504: ......
Page 505: ...671 14 Component Level Information Packets ...
Page 507: ......