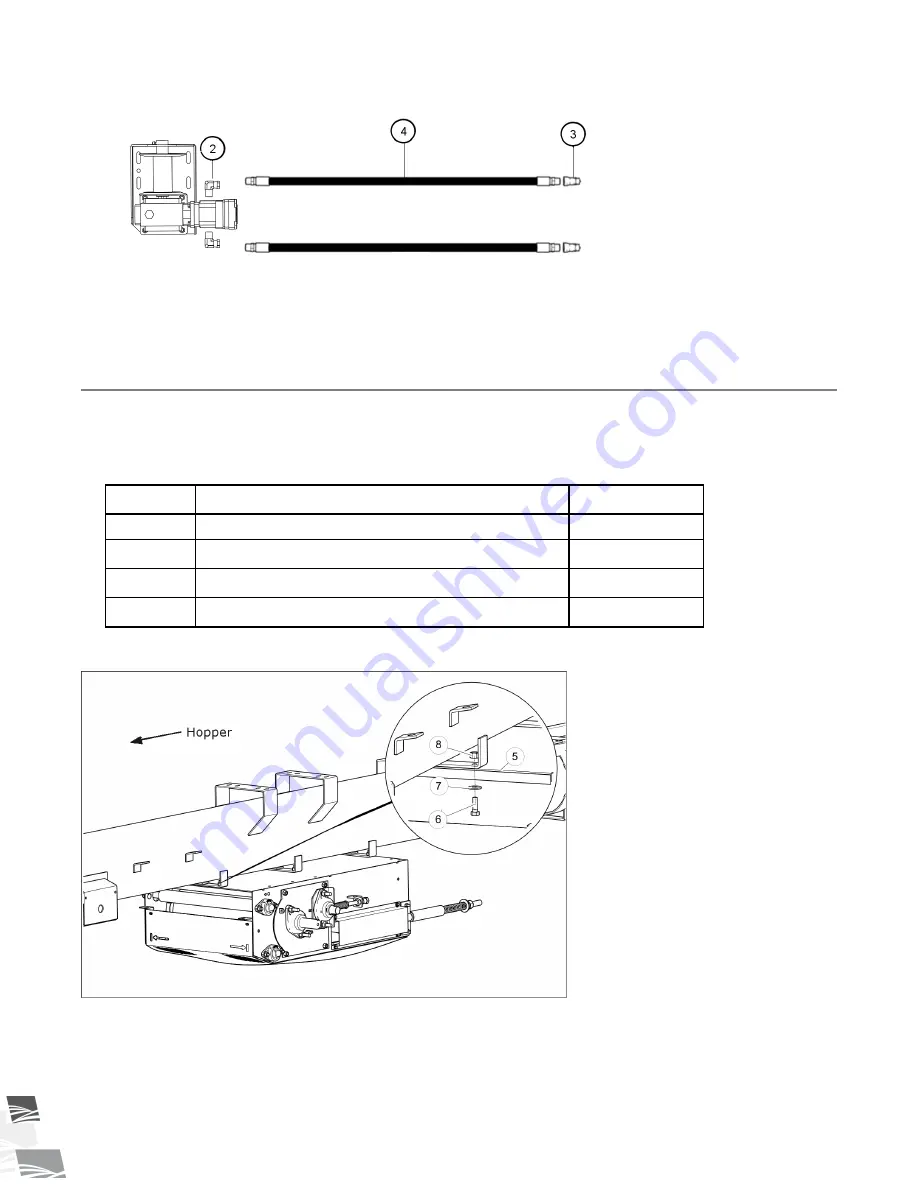
40
P1512115 R8
Figure 17.
Attaching the Hydraulic Hoses
4.11. Attach the S-Drive
1. Attach the s-drive (5) to the brackets with 7/16" x 1" bolts (6), 7/16" flat washers (7), and 7/16" locknuts (8)
(see
Table 9.
Components to Install S-Drive
Item
Description
Quantity
5
S-Drive
1
6
7/16" x 1" Hex Bolt
6
7
7/16" Flat Washer USS
6
8
7/16" Nylock Nut
6
Figure 18.
Attaching the S-Drive
PORTABLE GRAIN BELT CONVEYOR – FIELD LOADER