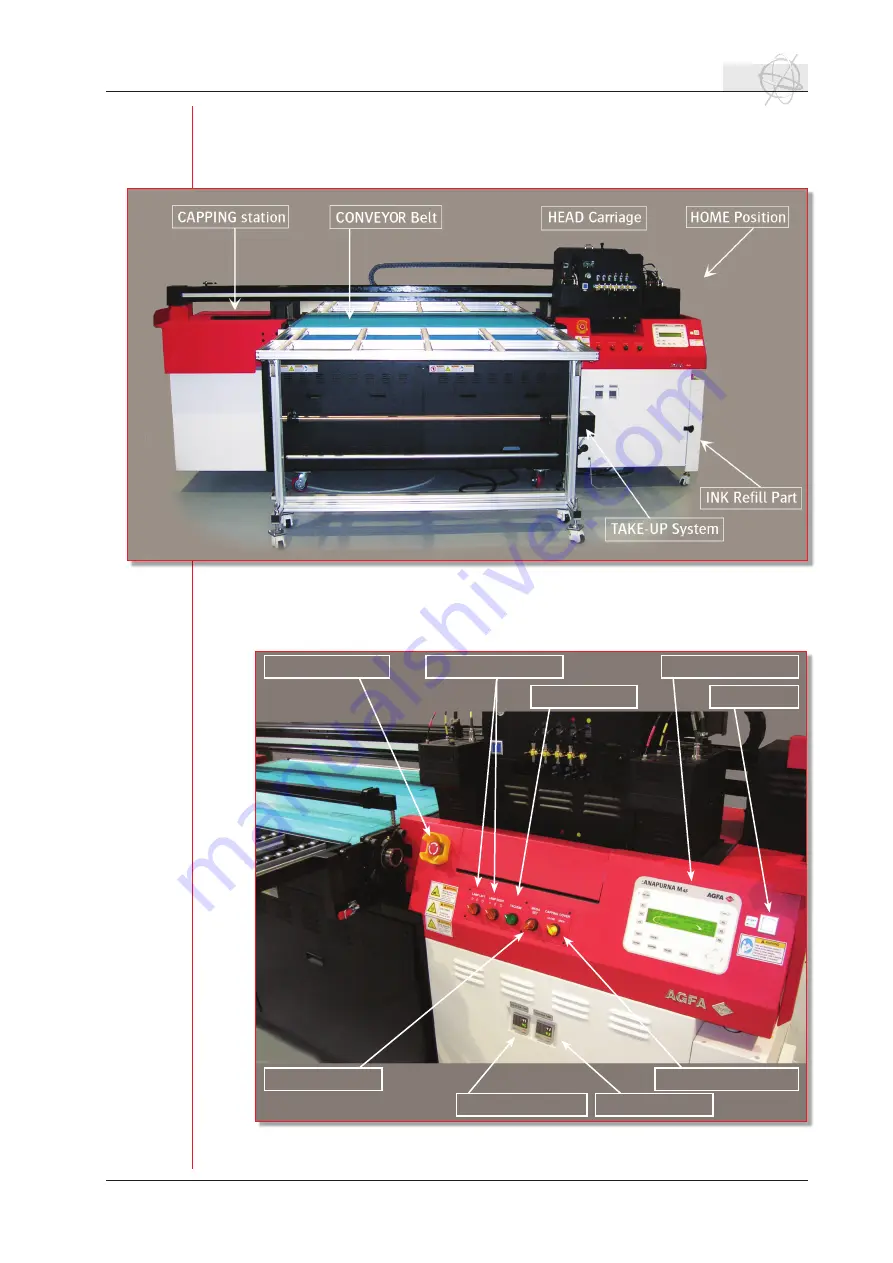
Stay ahead. With Agfa Global Services.
:Anapurna M
4F
- Operator Manual
Information - Printer overview
9
2. Printer overview.
2.1
Front view, parts & locations.
The roll to roll system is optional for the :Anapurna M4f
and is not delivered with a standard system.
2.2
Home view, parts & locations.
EMERGENCY Stop
UV LAMP R-L Switch
LCD Operation Panel
Start Button
Sub Ink Tank Temp.
Head Base Temp.
Vacuum Switch
Capping Cover Switch
Media Set