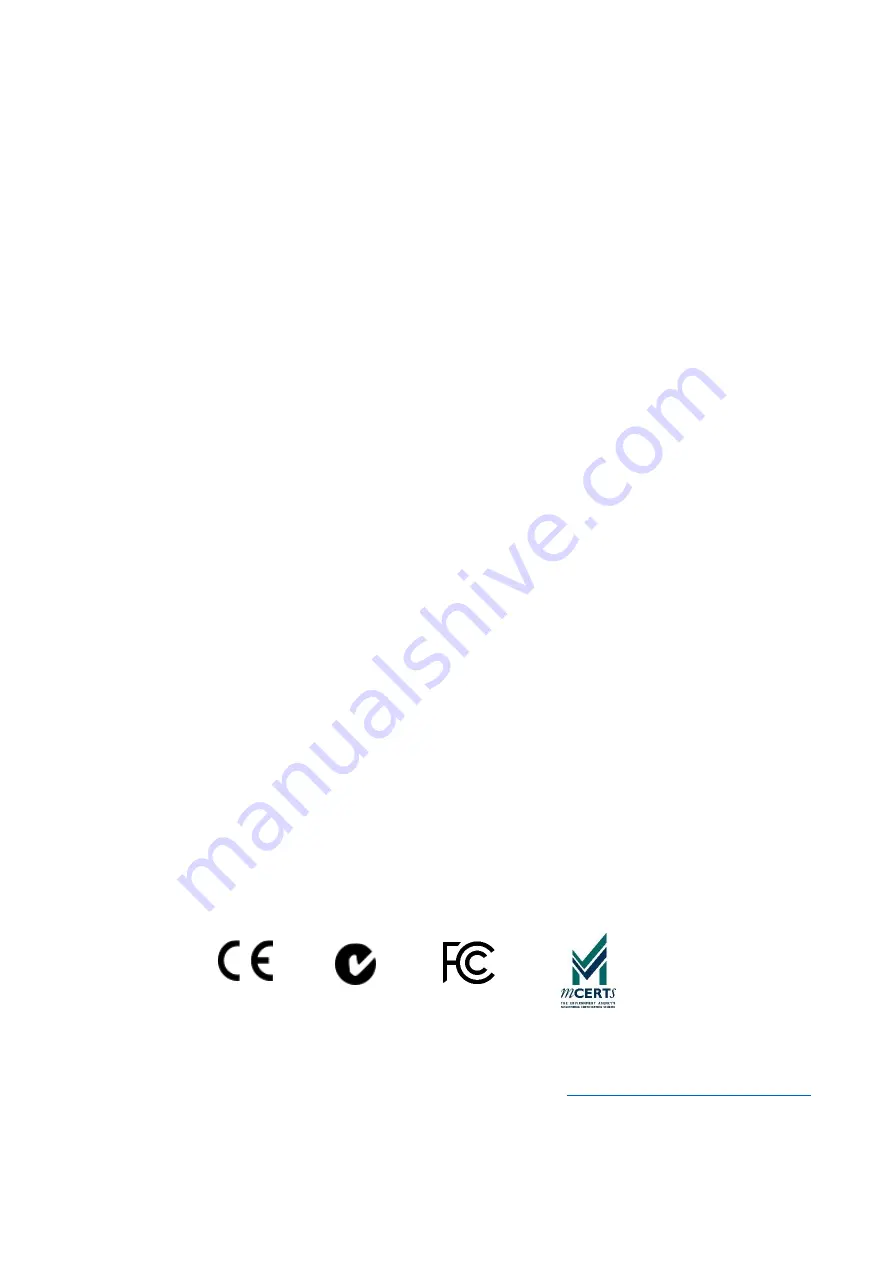
Aeroqual Dust Sentry / AQS User Guide
Page | 62
9 Copyright
Copyright Aeroqual Limited. All rights reserved. Reproduction, transfer, distribution or storage of part or all of
the contents of this document in any form without the prior written permission of Aeroqual Limited is
prohibited.
“Aeroqual” is a registered trademark of Aeroqual Limited. Other product and company names mentioned
herein may also be trademarks or trade names.
Aeroqual operates a policy of continuous development. Aeroqual reserves the right to make changes and
improvements to any of the products described in this document without prior notice.
Under no circumstances shall Aeroqual be responsible for any loss of data or income or any special,
incidental, consequential or indirect damages howsoever caused.
The contents of this document are provided "as is". Except as required by applicable law, no warranties of any
kind, either express or implied, including, but not limited to, the implied warranties of merchantability and
fitness for a particular purpose, are made in relation to the accuracy, reliability or contents of this document.
Aeroqual reserves the right to revise this document or withdraw it at any time without prior notice. The
availability of particular products may vary by region. Please check with the Aeroqual distributor nearest to
you.
10 Compliance
1. The Aeroqual Dust Sentry, Dust Sentry Pro and AQS 1 comply with the following standards:
EN 61000-6-1:2001
EN 61000-6-3:2001
Part 15 of the FCC Rules. Operation is subject to the following two conditions: (1) these devices may
not cause harmful interference, and (2) these devices must accept any interference received,
including interference that may cause undesired operation.
2. The Aeroqual Dust Sentry PM
10
has achieved MCERTs certification for indicative ambient particulate
monitor
This equipment has been tested and found to comply with the limits for a Class B digital device, pursuant to
Part 15 of the FCC Rules. These limits are designed to provide reasonable protection against harmful
interference in a residential installation. This equipment generates, uses and can radiate radio frequency
energy and, if not installed and used in accordance with the instructions, may cause harmful interference to
radio communications. However, there is no guarantee that interference will not occur in a particular
installation. If this equipment does cause harmful interference to radio or television reception, which can be
determined by turning the equipment off and on, the user is encouraged to try to correct the interference by
one or more of the following measures:
Reorient or relocate the receiving antenna.
Increase the separation between the equipment and receiver.
Connect the equipment into an outlet on a circuit different from that to which the receiver is
connected.
Consult your Aeroqual distributor or an experienced radio/TV technician for help.
11 Warranty
The monitor warranty policy can be found on the main company website:
www.aeroqual.com/support/warranty