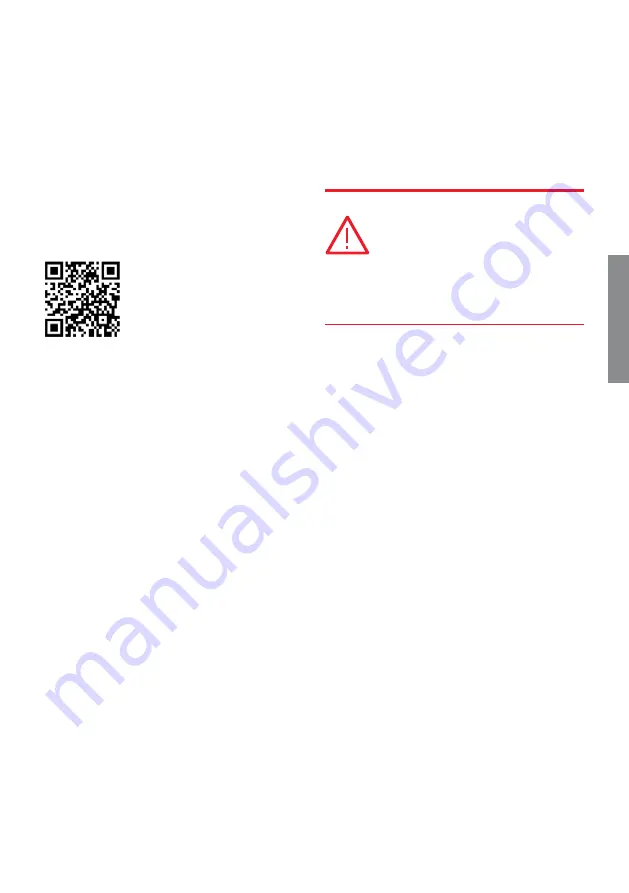
2
79
3 4ZBT S _ 3 0 -1 2 0 0A rev. A / 1 S CC 3 0 3 0 4 3 M 0 2 01
—
8. Mounting of Accessories
More information, see animation:
Installation of accessories - TruONE
™
ATS
(https://youtu.be/qV2KoIv38GY).
—
8.1 Ekip -Modules
Both switches already have a factory-in-
stalled auxiliary power supply module and
I/O signal modules Ekip Signaling 2K-1
and Ekip Signaling 2K-2.
NOTE!
It is still possible to add two pieces
of Ekip modules to the switch if the
switch is a fixed version, and one Ekip-
module to the Connection Module of
draw-out switch version. Eg. if more I/O
signal modules are needed, it is possible
to add an Ekip Signaling 2K-3 and/or alter-
natively a communication module Ekip
Com module, if required.
The wiring route instruction for Ekip
-modules in the cabinet, see the Part 1,
Chapter 4.
Danger
Hazardous voltage. Only an authorised elec-
trician may perform the electrical installation
and maintenance of OX_ automatic transfer
switches. Do not attempt any installation or
maintenance actions when Bypass-isolation
automatic transfer switch is connected to the
electrical mains. Before starting work, make
sure that the switch is de-energised.
Summary of Contents for Zenith ZBTS T Series
Page 2: ...2 Zenith ZBTS T series 100 1200A INSTALL ATION AND OPER ATING INSTRUCTION 1 ...
Page 6: ...6 Zenith ZBTS T series 100 1200A INSTALL ATION AND OPER ATING INSTRUCTION 1 ...
Page 10: ...10 Zenith ZBTS T series 100 1200A INSTALL ATION AND OPER ATING INSTRUCTION 1 ...
Page 44: ...44 Zenith ZBTS T series 100 1200A INSTALL ATION AND OPER ATING INSTRUCTION 1 ...
Page 58: ...58 Zenith ZBTS T series 100 1200A INSTALL ATION AND OPER ATING INSTRUCTION 1 ...
Page 68: ...68 Zenith ZBTS T series 100 1200A INSTALL ATION AND OPER ATING INSTRUCTION 1 ...
Page 100: ...2 100 Zenith ZBTS T series 100 1200A INSTALL ATION AND OPER ATING INSTRUCTION 3 ...
Page 103: ...2 103 34ZBTS _ 30 1200A rev A 1SCC303043M0201 4 ...
Page 105: ...2 105 34ZBTS _ 30 1200A rev A 1SCC303043M0201 4 ...
Page 107: ...2 107 34ZBTS _ 30 1200A rev A 1SCC303043M0201 4 ...
Page 108: ...2 108 Zenith ZBTS T series 100 1200A INSTALL ATION AND OPER ATING INSTRUCTION 4 ...
Page 109: ...2 109 34ZBTS _ 30 1200A rev A 1SCC303043M0201 4 ...