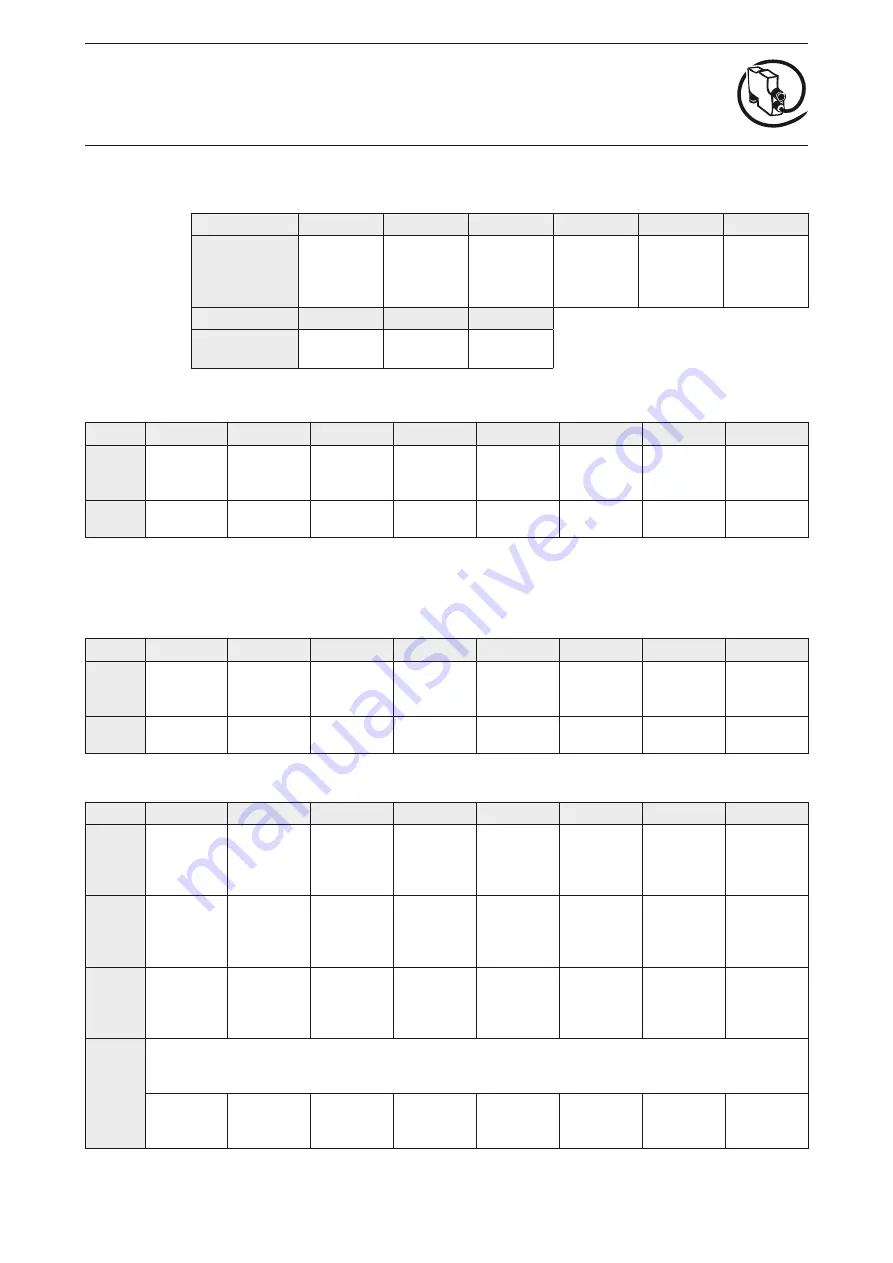
- 97 -
UMC22-FBP
FieldBusPlug / Issue: 02.2008
V 6
Universal Motor Controller UMC22-FBP
Software version 4.0
7.4.3 Interface and data overview
Hardware Inputs / Outputs
Terminal
13
14
15
16
17
18
Device input
(to bus)
DI0
1)
(Multi-function
input or
check-back)
DI1
1)
(Multi-function
input)
DI2
1)
(Multi-function
input)
DI3
1)
(Local:
reverse On)
DI4
1)
(Local:
forward On)
DI5
1)
(Local: Off)
Terminal
7
8
9
Device output
(from bus)
DO0
Forward
DO1
Reverse
DO2
1)
(Fault output)
Chapter 7.4.3~1 Revesing starter
Monitoring telegram, digital
Bit No.
7
6
5
4
3
2
1
0
Byte 0
WARNING
FAULT
LOCAL
CONTROL
REVERSE
LOCK-OUT
TIME
-
RUN
FORWARD
OFF
RUN
REVERSE
Byte 1
DI5
1)
(UMCinput)
DI4
1)
(UMCinput)
DI3
1)
(UMCinput)
DI2
1)
(UMCinput)
DI1
1)
(UMCinput)
DI0
1)
(UMCinput)
-
-
Monitoring telegram, analog
Byte 0 and Byte 1: Motorcurrent in % of set current
Command telegram, digital only
Bit Nro
7
6
5
4
3
2
1
0
Byte 0
-
FAULT
RESET
AUTO
MODE
PREPARE
EMERGENCY
START
SELF
TEST
RUN
FORWARD
OFF
RUN
REVERSE
Byte 1
DO2
1)
(UMC output)
-
-
-
-
-
-
Diagnosis telegram
Bit No.
7
6
5
4
3
2
1
0
Fault
Byte 0
-
Self test failed
F010
2)
Fault signal
on DI0, DI1
or DI2
1)
F011
2)
-
-
-
-
-
Fault
Byte 1
Overload (trip)
fault
trip
2)
Motor blocked
F002
2)
Communi-
cation fault
F003
2)
Parameter out
of range
F004
2)
Current
check-back
fault
1)
F005
2)
-
Relay 1
check-back
fault
1)
F007
2)
Relay 0
check-back
fault
1)
F008
2)
Warning
Byte 2
Motor current
high threshold
1)
Motor current
low threshold
1)
-
Cooling time
running
°C
2)
-
Self test
running
buSy
2)
Emergency
start
prepared
-
Warning
Byte 3
If Parameter out of range: Pamameter number (leading two stages of the parameter, e.g. "02" Current factor)
If Self test fauled: Self test error number (only for service)
In all other cases:
Phase loss
trip
2
Fault on DI2
F024
2)
Faut on DI1
F023
2)
Fault on DI0
F022
2)
Earth fault
F020
2)
PTC
short-circuit
F019
2)
PTC
wire break
F018
2)
PTC
temperature
F017
2)
1)
depending on parameterization
2)
displayed on the Control Panel
Busdata details see 4.2.2.
Summary of Contents for UMC22-FBP
Page 167: ......