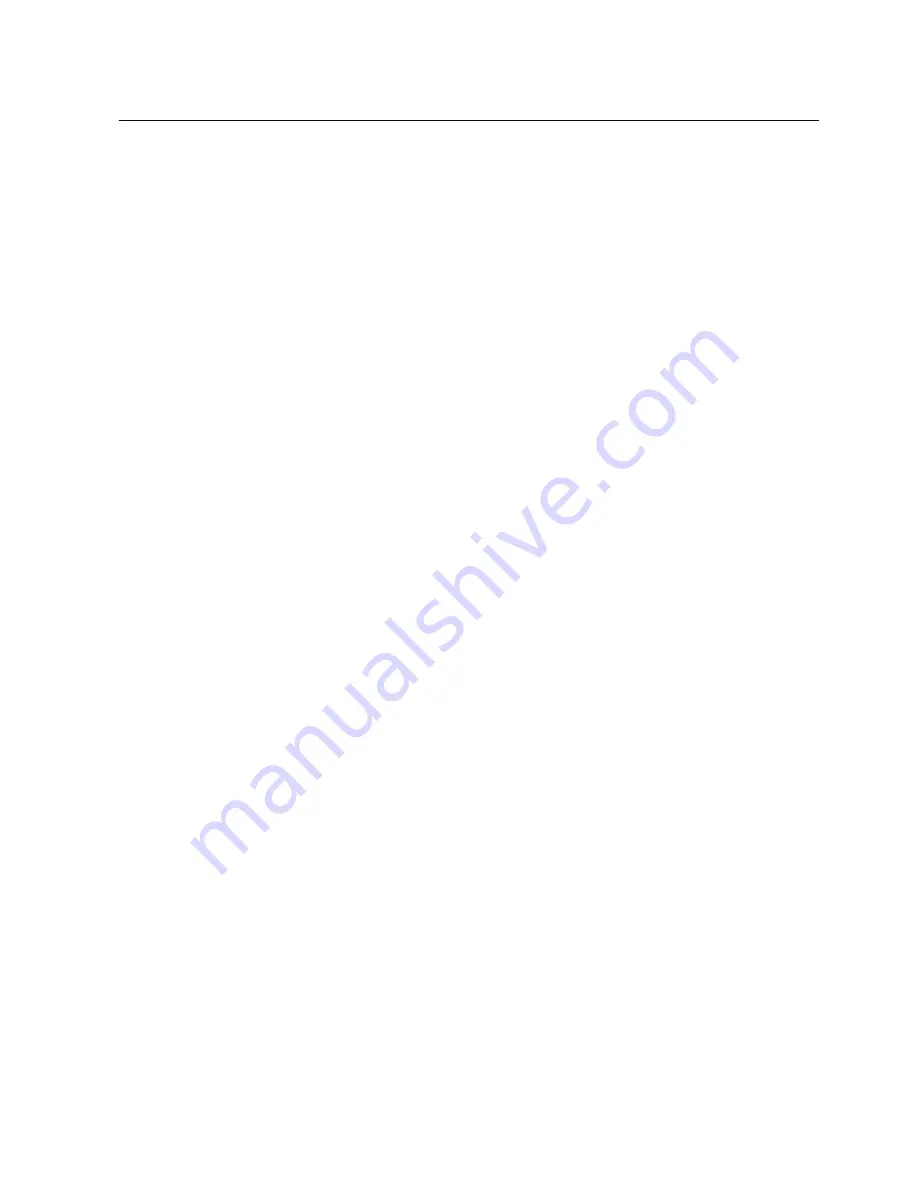
The adequate performance of the CT should be checked when the setting of the high
set stage overcurrent protection is defined. The operate time delay caused by the CT
saturation is typically small enough when the overcurrent setting is noticeably lower
than F
a
.
When defining the setting values for the low set stages, the saturation of the CT does
not need to be taken into account and the start current setting is simply according to the
formula.
Delay in operation caused by saturation of current transformers
The saturation of CT may cause a delayed protection relay operation. To ensure the
time selectivity, the delay must be taken into account when setting the operate times
of successive protection relays.
With definite time mode of operation, the saturation of CT may cause a delay that is
as long as the time the constant of the DC component of the fault current, when the
current is only slightly higher than the starting current. This depends on the accuracy
limit factor of the CT, on the remanence flux of the core of the CT, and on the operate
time setting.
With inverse time mode of operation, the delay should always be considered as being
as long as the time constant of the DC component.
With inverse time mode of operation and when the high-set stages are not used, the AC
component of the fault current should not saturate the CT less than 20 times the
starting current. Otherwise, the inverse operation time can be further prolonged.
Therefore, the accuracy limit factor F
a
should be chosen using the formula:
F
a
> 20 ×
Current start value
/ I
1n
The
Current start value
is the primary start current setting of the protection relay.
4.1.1.3
Example for non-directional overcurrent protection
The following figure describes a typical medium voltage feeder. The protection is
implemented as three-stage definite time non-directional overcurrent protection.
1MRS757456 D
Section 4
Requirements for measurement transformers
REF611
171
Application Manual
Summary of Contents for REF611
Page 1: ...Relion 611 series Feeder Protection and Control REF611 Application Manual ...
Page 2: ......
Page 10: ...4 ...
Page 174: ...168 ...
Page 184: ...178 ...
Page 187: ...181 ...