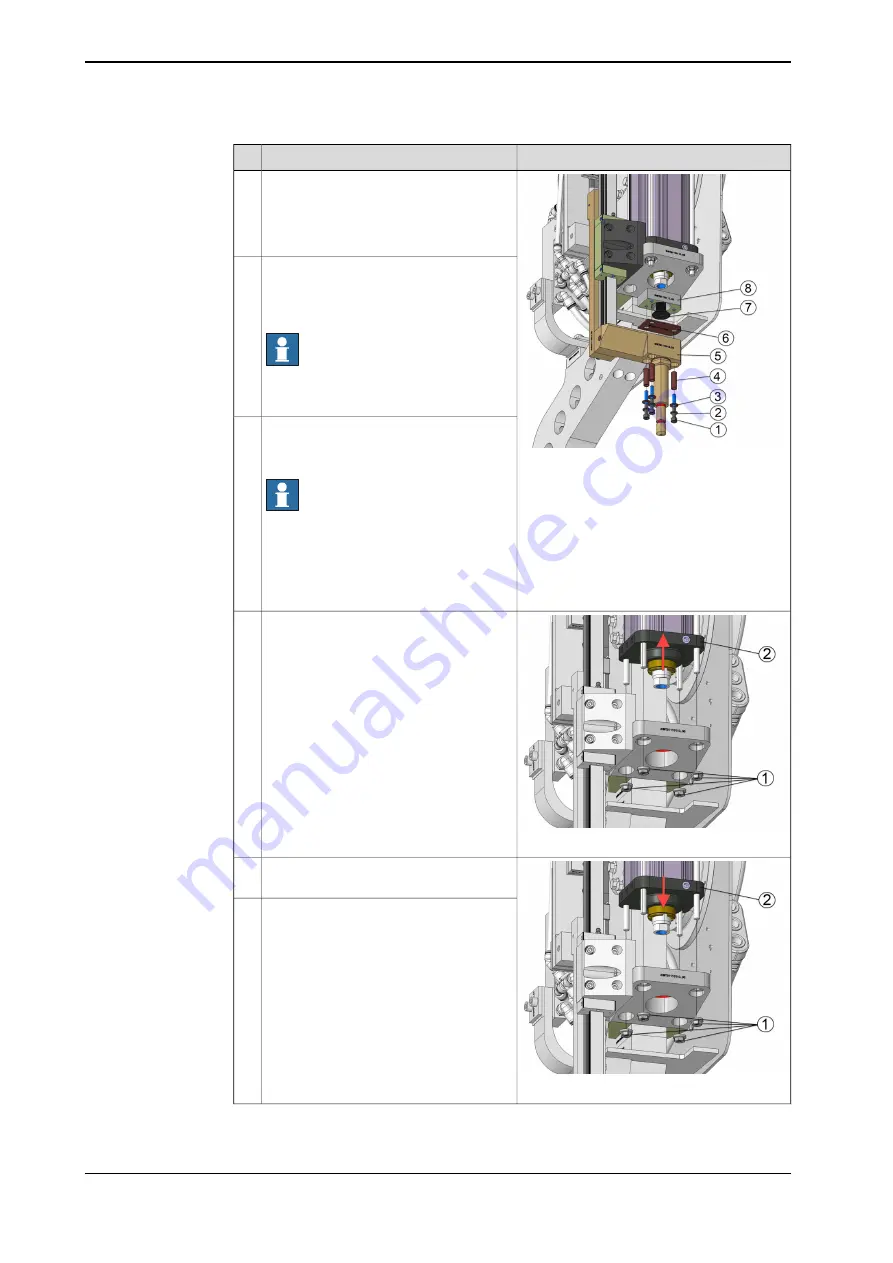
Illustration
Action
xx2200000339
Unscrew the three screws (pos. 1) fixing
the electrode holder. Remove them togeth-
er with the three washers (pos. 2), the
three insulation washers (pos. 3) and the
three insulation sleeves (pos. 4).
6
Hold on to the electrode parts as they
slide down and let them rest on the fixed
electrode. Remove the insulation plate
(pos. 6).
Note
Make sure the guide rail doesn´t slide out
of the runner block.
7
Unscrew the M16 screw (pos. 7) connect-
ing the piston rod and piston rod coupling
(pos. 8). Remove gently.
Note
The M16 screw is secured with Loctite
243 so if needed, heat the screw (pos. 7)
with a hot air gun or equal to loosen it.
Use a wrench to hold piston rod coupling
in place while loosening the M16 screw.
8
xx2200000340
Remove the four nuts holding the actuat-
or.
9
xx2200000341
Position the new actuator and slide it into
place (pos. 2).
10
Apply thread locking fluid - Loctite 243 to
the nuts, before reassembling the nuts
and washers (pos. 1) holding the actuator.
If flange nuts are used there is no need
to apply Loctite 243. Tighten the nuts with
a tightening torque of 23 Nm.
11
Continues on next page
92
Product manual - GWT C9
3HAA010198-001 Revision: A
© Copyright 2022 ABB. All rights reserved.
5 Repair
5.6 Replacement of the actuator
Continued
Summary of Contents for GWT C9
Page 1: ...ROBOTICS Product manual GWT C9 ...
Page 62: ...This page is intentionally left blank ...
Page 124: ...This page is intentionally left blank ...
Page 126: ......
Page 127: ......