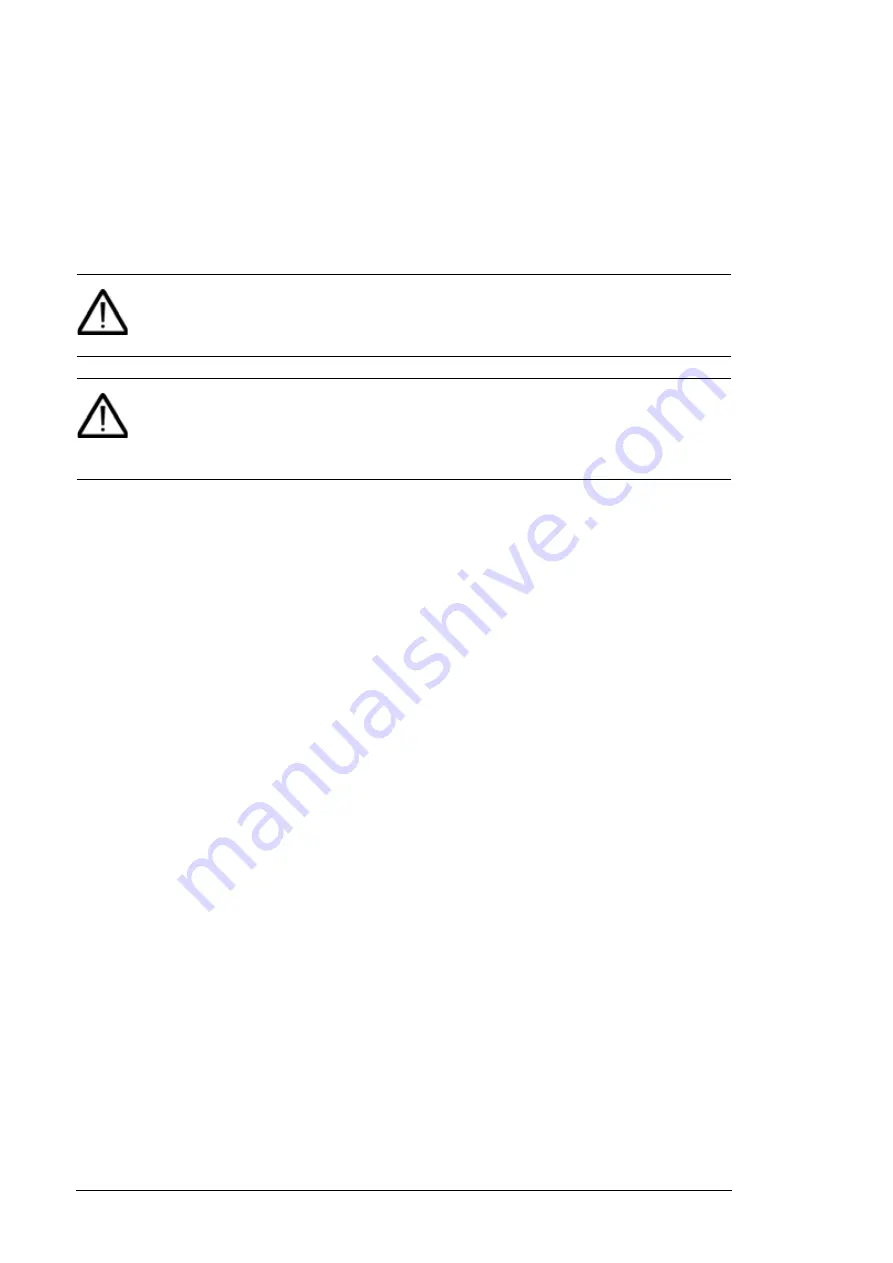
116 The internal cooling circuit
Maintenance
Filling up and bleeding the internal cooling circuit
Converter line-ups with a customer cooling unit
Both the converter and coolant must be at room temperature before filling in the cooling
circuit.
WARNING!
Ensure that the maximum permissible operating pressure is not
exceeded. When necessary regulate the pressure to appropriate level by draining
excess coolant out of the system.
WARNING!
Bleeding of the cooling circuit is very important and has to be done
with great care. Air bubbles in the cooling circuit may reduce or completely block
coolant flow and lead to overheating. Let the air out of the cooling system while
filling in coolant and, eg, after any power module replacements.
Notes:
•
The bleed valves in the line-up are used only to vent the air from the circuit so that it
can be displaced by the coolant. The actual bleeding of the circuit must be done via an
external bleed valve installed at the highest point of the cooling circuit. The most
practical location for the valve is usually near or at the cooling unit.
•
Observe the instructions given by the manufacturer of the cooling unit. Pay special
attention to filling up and bleeding the pumps properly as they may be damaged if
operated when dry.
•
Draining liquid into the sewer system is not allowed (it may contain harmful
substances like propylene glycol).
1. Open the main bleed valve at the cooling unit.
2. Open the inlet, outlet and bleed valves of one converter cubicle.
3. Lead the bleed hoses into buckets or other suitable containers. Extend the standard
hoses if necessary.
4. Fill the circuit with coolant. For coolant specification, see below.
5. After the converter unit is filled up, coolant will start flowing from the bleed hose of the
converter cubicle. Let some coolant flow out before closing the bleed valve.
6. Close the inlet, outlet and bleed valves of the converter cubicle.
7. Open the inlet and outlet valves in converter cubicle. Let any air remaining in the
system out through the bleed valve at the cooling unit.
8. Close the bleed valve at the cooling unit.
9. Continue to fill in coolant until a base pressure of 100…150 kPa (1…1.5 bar) is
achieved.
10. Open the bleed valve of the pump to allow any air out.
11. Re-check the pressure and add coolant if necessary.
12. Start the coolant pump. Let any air remaining in the system out through the bleed
valve at the cooling unit.
13. After one to two minutes, stop the pump or block the coolant flow with a valve.
14. Re-check the pressure and add coolant if necessary.
Summary of Contents for ACS800-67LC
Page 1: ... ABB WIND TURBINE CONVERTERS ACS800 67LC wind turbine converters Hardware manual ...
Page 4: ......
Page 16: ...16 Safety instructions ...
Page 22: ...22 Introduction to the manual ...
Page 42: ...42 Operation principle and hardware description ...
Page 52: ...52 Mechanical installation ...
Page 79: ...Electrical installation 79 3 3 Rotor side cable connection terminals U2 V2 W2 ...
Page 92: ...92 Maintenance 4 6 5 5 ...
Page 103: ...Maintenance 103 Bussmann fuses Mersen fuses ...
Page 109: ...Maintenance 109 5 6 7 ...
Page 131: ...Technical data 131 Declaration of incorporation ...
Page 136: ...136 Dimension drawings ACS800 67LC 1075 0575 7 and 1375 0575 7 ...
Page 137: ...Dimension drawings 137 With 400 mm wide incoming cubicle option C111 ...
Page 138: ...138 Dimension drawings ACS800 67LC 1375 1125 7 ...
Page 139: ...Dimension drawings 139 With 400 mm wide incoming cubicle option C111 ...
Page 140: ...140 Dimension drawings ACS800 67LC 1595 0865 7 and 2035 1125 7 ...
Page 141: ...Dimension drawings 141 With 400 mm wide incoming cubicle option C111 ...
Page 143: ...Dimension drawings 143 Options 2H370 and C111 Option 1H371 ...
Page 144: ...144 Dimension drawings Options 1H371 and C111 Options 2H371 and C111 ...
Page 145: ...Dimension drawings 145 Option H378 Options H378 and C111 ...
Page 147: ...Dimension drawings 147 Option 2H372 ...
Page 148: ...148 Dimension drawings Option 3H372 ...
Page 149: ...Dimension drawings 149 Option 1H373 ...
Page 150: ...150 Dimension drawings Option 2H373 ...
Page 151: ...Dimension drawings 151 Option 3H373 ...