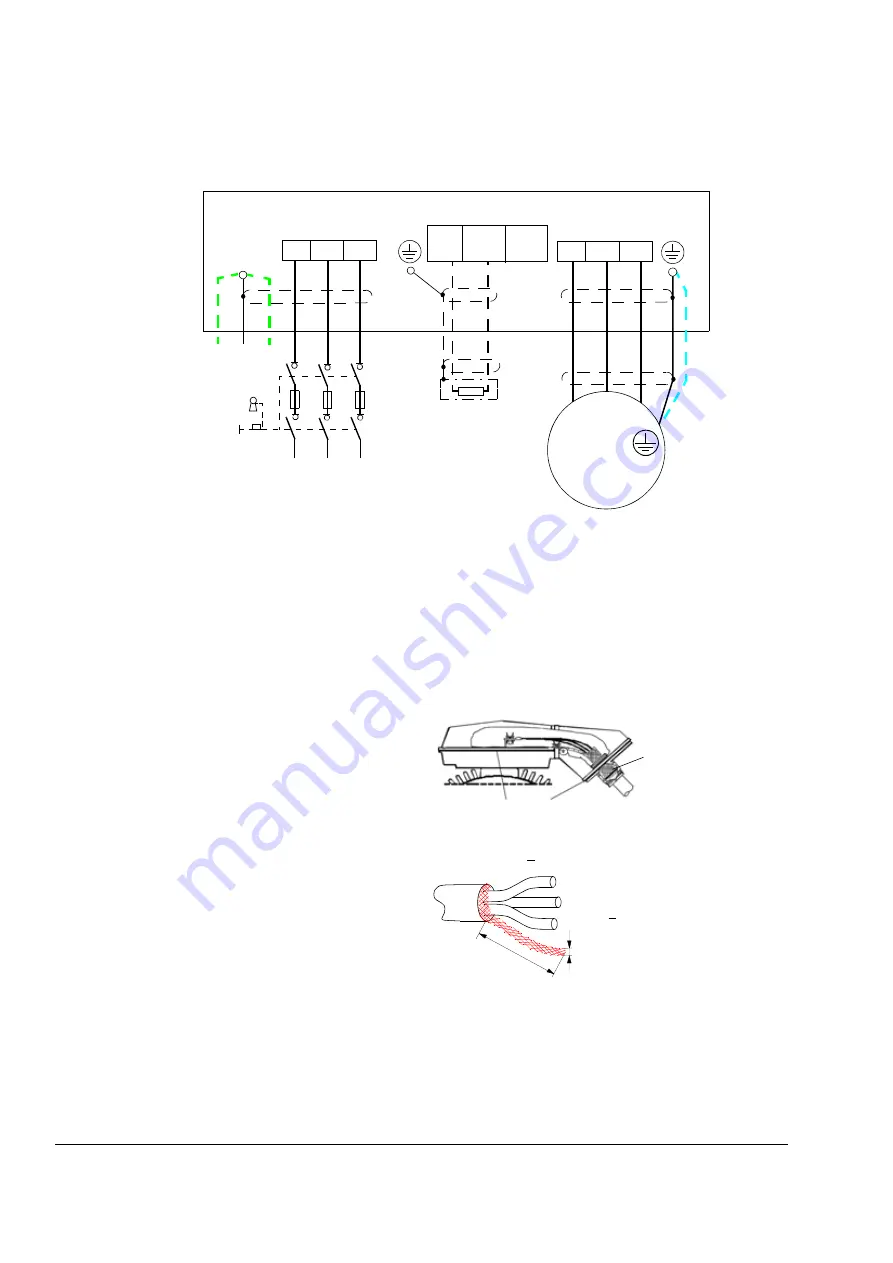
Electrical installation
58
Power cable connection diagram
INPUT
OUTPUT
U1 V1 W1
1)
U2 V2 W2
UDC+
R+
UDC
-
R
-
L1
L2
L3
(PE)
(PE)
PE
2)
Drive module
PE
* For alternatives, see
Planning the electrical
installation
*
Grounding of the motor cable shield at the cabinet entry
Ground the cable shield 360 degrees at the lead-through of the
cabinet.
Grounding of the motor cable shield at the motor end
For minimum radio frequency interference:
• ground the cable shield 360 degrees at the lead-through of
the motor terminal box
• or ground the cable by twisting the shield as follows:
flattened width > 1/5 · length.
360 degrees grounding
Conductive gaskets
a
b
b > 1/5 · a
1), 2)
If shielded cable is used (not required but
recommended) and the conductivity of the shield is
< 50 % of the conductivity of the phase conductor,
use a separate PE cable (1) or a cable with a
grounding conductor (2).
Ground the other end of the input cable shield or PE
conductor at the distribution board.
3) 360 degrees grounding recommended at the cabinet
entry if shielded cable
4) 360 degrees grounding required at the cabinet entry
in first environment installations **
5) Use a separate grounding cable if the conductivity of
the cable shield is < 50 % of the conductivity of the
phase conductor and there is no symmetrically
constructed grounding conductor in the cable (see
Planning the electrical installation
).
Note:
If there is a symmetrically constructed grounding
conductor in the motor cable in addition to the
conductive shield, connect the grounding conductor to
the grounding terminal at the drive and motor ends.
Do not use an asymmetrically constructed motor cable.
Connecting its fourth conductor at the motor end
increases bearing currents and causes extra wear.
External brake
resistor
3)
4)
U1
V1
W1
3
~
Motor
5)
4)
**
First environment EMC compliance is defined in
Summary of Contents for ACS800-04
Page 4: ......
Page 12: ...Safety instructions 12 ...
Page 54: ...Planning the electrical installation 54 ...
Page 72: ...Motor control and I O board RMIO 72 ...
Page 116: ...Resistor braking 116 ...
Page 117: ......