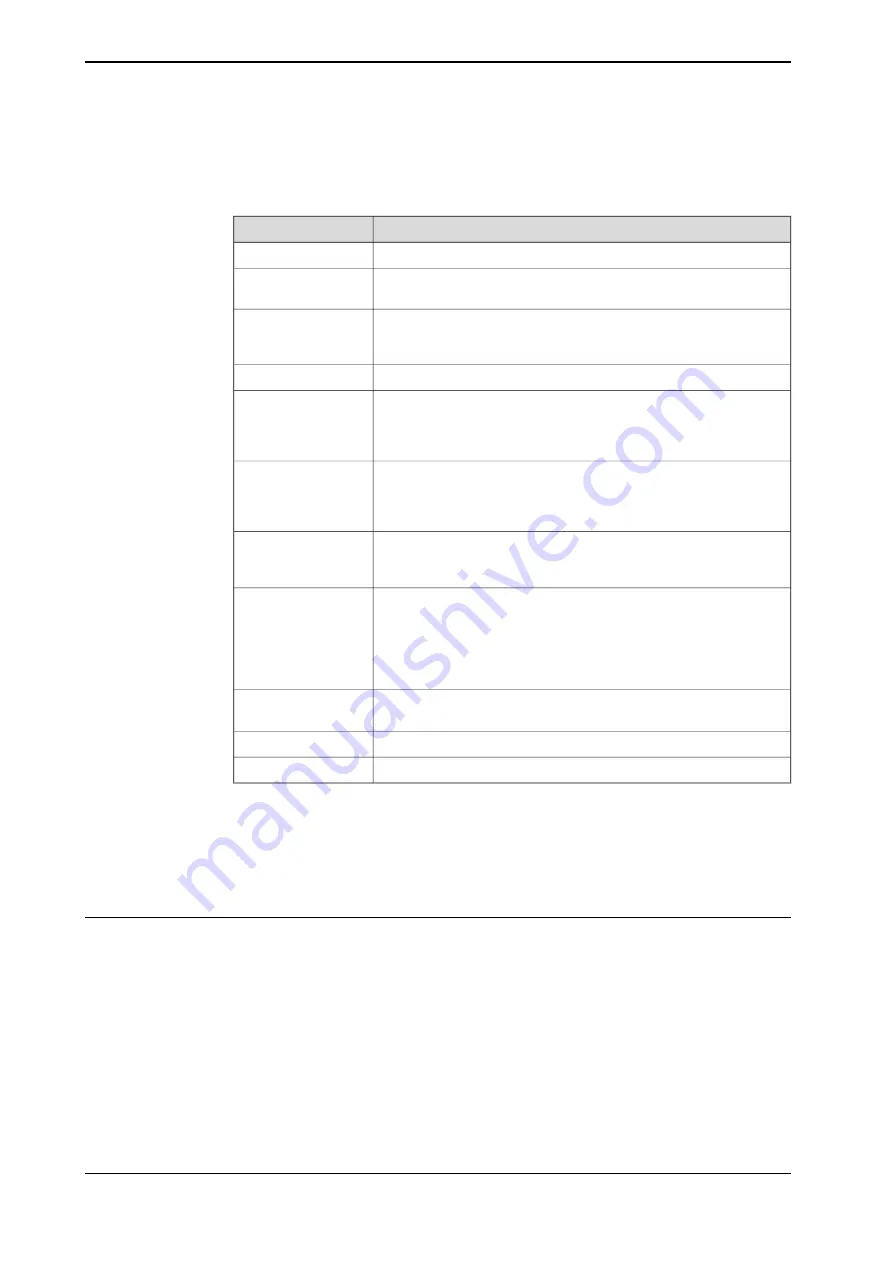
pictured, it is more accurate to measure the end of the tool where the TCP actually
is, because we do not have to worry about variation in location.
Here is an explanation of the
be_tooldesign
parameters with comments:
Description
Parameter
This we want
TRUE
so we define orientation also.
OrientBody
Set to a value at least as large as the largest section diameter. 30
mm, in this case.
MaxBodyDia
We want to put a very small number here so that BullsEye will not
think it has reached the end of the tool until it makes slices all the
way past the end of the ball. We will use 1 mm.
MinBodyDia
Searchable portion of tool. 50 mm, in this case.
ScanRange
The ball is almost 7 mm in diameter. Putting 3.5 mm here will force
the final measurement to be near the middle of the ball. If BullsEye
misses the end of the ball during the setup process, this number
could be increased.
RangeShift
6 mm is a good number. Small numbers are important when there
are features that you don't want to miss when BullsEye is taking
slices. Big numbers are good when you want the setup process to
take less time.
SliceGap
This should be
FALSE
. The tool does not have a wire that we will
mathematically extend out from the gas cup. Instead we will measure
all the way to the end of the tool.
ScanWire
We want the final z-axis search to be inline with the ball. So, this
parameter should be
FALSE
. In contrast, a welding gun has a wire
that is too narrow to search and the wire is always a different length.
For this reason, a welding tool definition would have this parameter
set to
TRUE
so that the z-axis search occurs next to the wire and
searches for the end of the gas cup.
OffsEndSearch
This parameter has no affect when
OffsEndSearch
and
ScanWire
are
FALSE
.
WireDia
Movement speed. This is not the search speed.
SlowMoveSpeed
Movement speed. This is not the search speed.
FastMoveSpeed
Last, the TCP extension passed into the
BESetupToolJ
instruction, must be fixed.
BESetupToolJ jtBEApprPos,jtBEStartPos,-3.375 , tdMyProbe...
A negative number will move the TCP from the end of the ball to the center of the
ball. The default settings for
be_scan
and
be_device
will work fine for a standard
ABB I/O board.
How do I proceed when BullsEye gives large deviations?
If BullsEye gives large deviations during reorientation, try rotating the BullsEye
sensor 90 degrees in order to reduce the influences from mechanical tolerances
in the robot arm.
54
Application manual - BullsEye
3HAC050989-001 Revision: C
© Copyright 2004-2018 ABB. All rights reserved.
5 User guide
5.5 Frequently asked questions
Continued
Summary of Contents for 0503060880
Page 1: ...ROBOTICS Application manual BullsEye ...
Page 6: ...This page is intentionally left blank ...
Page 22: ...This page is intentionally left blank ...
Page 28: ...This page is intentionally left blank ...
Page 84: ...This page is intentionally left blank ...
Page 88: ......
Page 89: ......