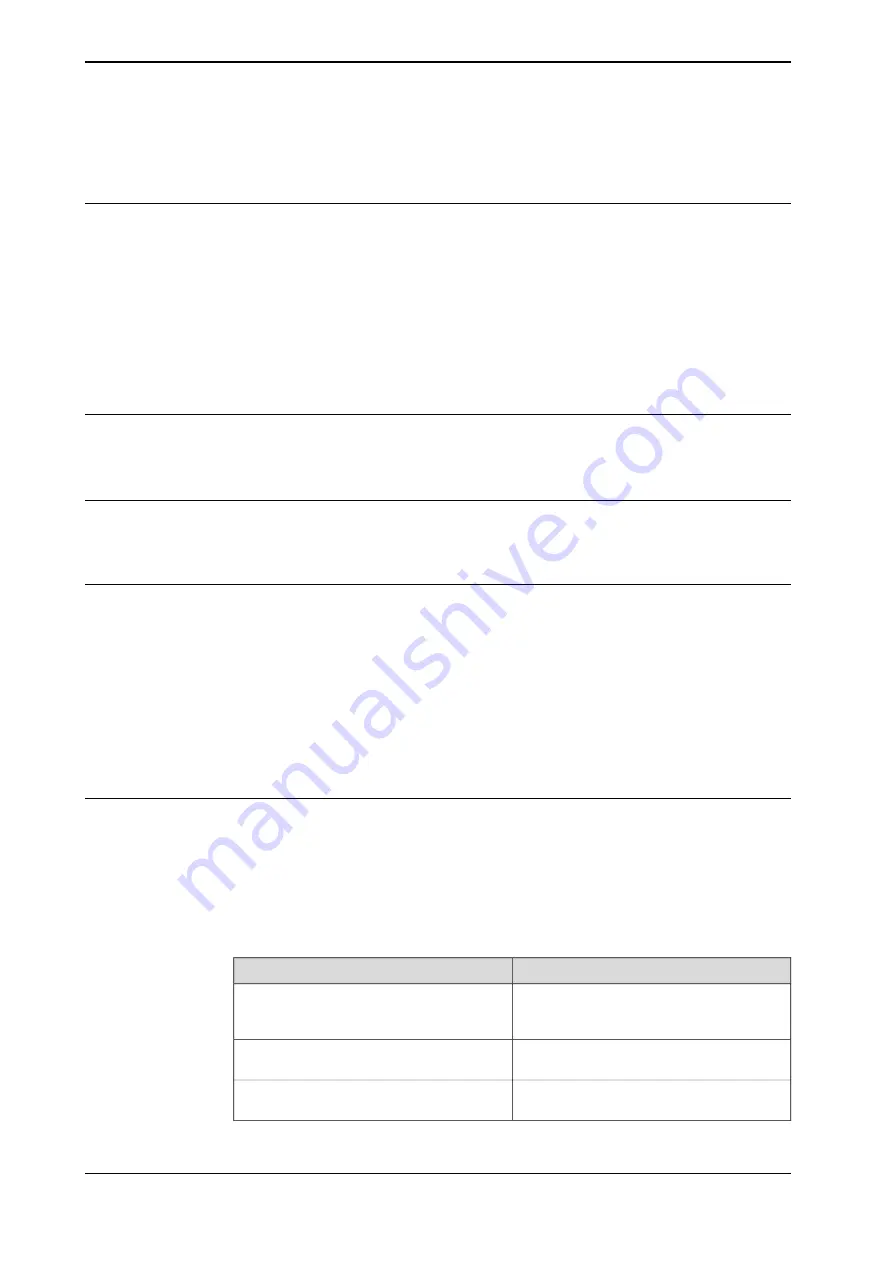
the robot also allows the possibility of executing TCP checks anywhere in the
working range of the robot carrier. This can cut TCP checking time tremendously.
How do I set up BullsEye when the robot is moved by a track?
If the BullsEye scanning device is mounted on the carrier with the robot, no changes
are needed. This is the preferred method since it negates the positional inaccuracy
of the robot carrier. If the BullsEye scanning device is fixed in the world, then a
flag must be set in the
be_device
data to inform BullsEye.
CONST be_device devYokeUpTrack:=["diBE_SENSE",
TRUE,[6,45,100,100],[40,45,100,100],0.10,FALSE, FALSE,TRUE];
The flag in the device data is called
MovedWithRobot
. For more information see
be_device - Device data on page 55
Can I change my TCP extension without rerunning the initialization?
Yes. Use the
BETcpExtend
instruction, see
BETcpExtend - BullsEye extend TCP
Can the BullsEye yoke be mounted in any orientation?
Yes, but the BullsEye scanning device must be mounted so that the scan plane is
parallel with the robot's physical base surface.
How do I set up a non-ABB supplied I/O device?
Only ABB I/O devices are guaranteed to work with BullsEye. Many I/O devices
from other vendors are too slow or too unrepeatable to allow BullsEye to work
correctly When using non-ABB devices, you may need to slow the scan speeds
substantially to improve accuracy.
A WAGO I/O device, for example, may be used in the COS (
Change of State
) mode,
but the PIT (
Production Inhibit Time
) should be reduced as much as possible,
preferably to zero. This is done in the system parameter
Production inhibit time
,
in the topic
I/O
, the type
Unit Type
.
What is a convergence error?
BullsEye measures the TCP more than once during the setup. It converges on a
solution that is within limits influenced by the
be_device
data,
Repeatability
.
If the deviation between two TCP measurements cannot be reduced to a level
specified by the
Repeatability
value, BullsEye eventually times-out and reports
a
convergence error
.
Convergence errors can occur for a variety of reasons:
Solution
Problem
This can be corrected by fixing the parameter
values to match the tool and scanning
equipment.
Incorrect parameters are used in the setup.
This can be corrected by improving the tool
mount.
The tool is not mounted securely or tool
mount bracket is too flexible.
This can be corrected by improving the
mounting structures.
The relationship between the BullsEye sensor
and the robot base is not solid.
Continues on next page
52
Application manual - BullsEye
3HAC050989-001 Revision: C
© Copyright 2004-2018 ABB. All rights reserved.
5 User guide
5.5 Frequently asked questions
Continued
Summary of Contents for 0503060880
Page 1: ...ROBOTICS Application manual BullsEye ...
Page 6: ...This page is intentionally left blank ...
Page 22: ...This page is intentionally left blank ...
Page 28: ...This page is intentionally left blank ...
Page 84: ...This page is intentionally left blank ...
Page 88: ......
Page 89: ......