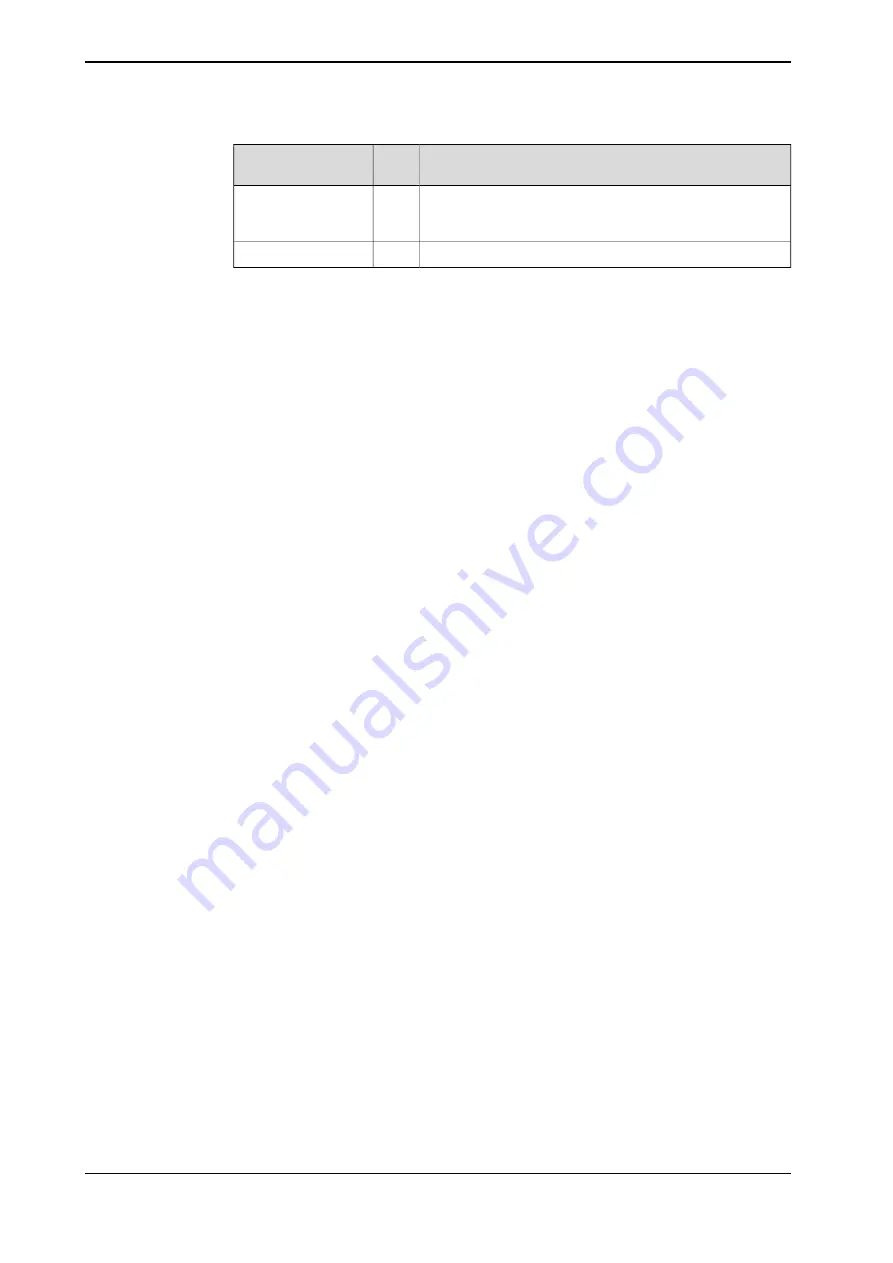
Description
Error
code
Error name
This tool has been initialized with the optional
UserFramePos
. The optional functionality is not working
correctly and the execution has been aborted.
44
BEGetGantryErr
An unknown error has occurred.
300
BEUnknownErr
50
Application manual - BullsEye
3HAC050989-001 Revision: C
© Copyright 2004-2018 ABB. All rights reserved.
5 User guide
5.4 BullsEye status codes
Continued
Summary of Contents for 0503060880
Page 1: ...ROBOTICS Application manual BullsEye ...
Page 6: ...This page is intentionally left blank ...
Page 22: ...This page is intentionally left blank ...
Page 28: ...This page is intentionally left blank ...
Page 84: ...This page is intentionally left blank ...
Page 88: ......
Page 89: ......