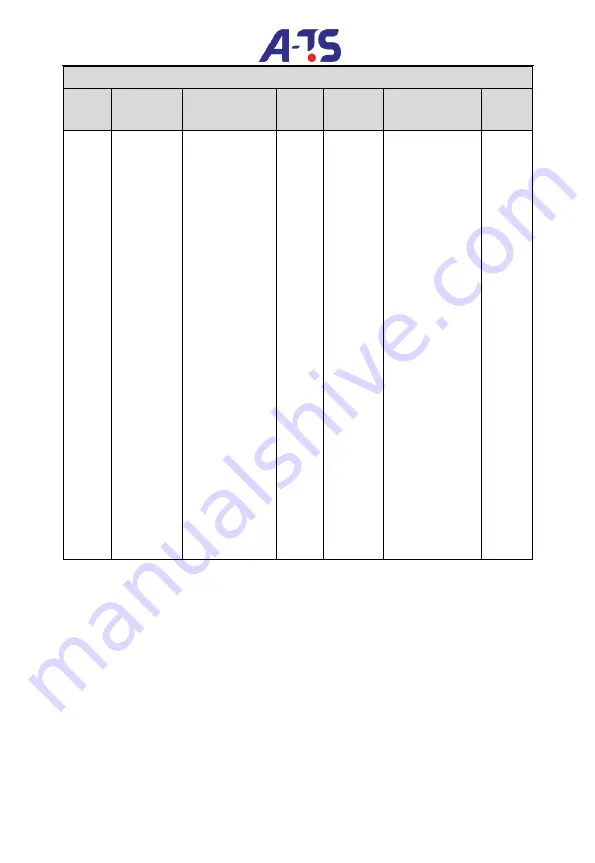
A-TS
117
https://a-ts.cn/en/
FL Group: Fault Protection Parameters ( total 22 )
Code
Name
Setting Scope
Min
Unit
Defaulte
d Value
Address
Chang
e
PL.15
Fault type
of the
previous
time
run at
acceleration
( F.oC1 )
2: Overcurrent
run at
deceleration
( F.oC2 )
3: Overcurrent
run at constant
speed
( F.oC3 )
4: Overvoltage
run at
acceleration
( F.oU1 )
5: Overvoltage
run at
deceleration
( F.oU2 )
6: Overvoltage
run at constant
speed
( F.oU3 )
7: Overvoltage
at control
voltage
( F.PoU )
8: Reserved
9: Phaseloss
at outpput
( F.oPL )
1
0
110EH
*