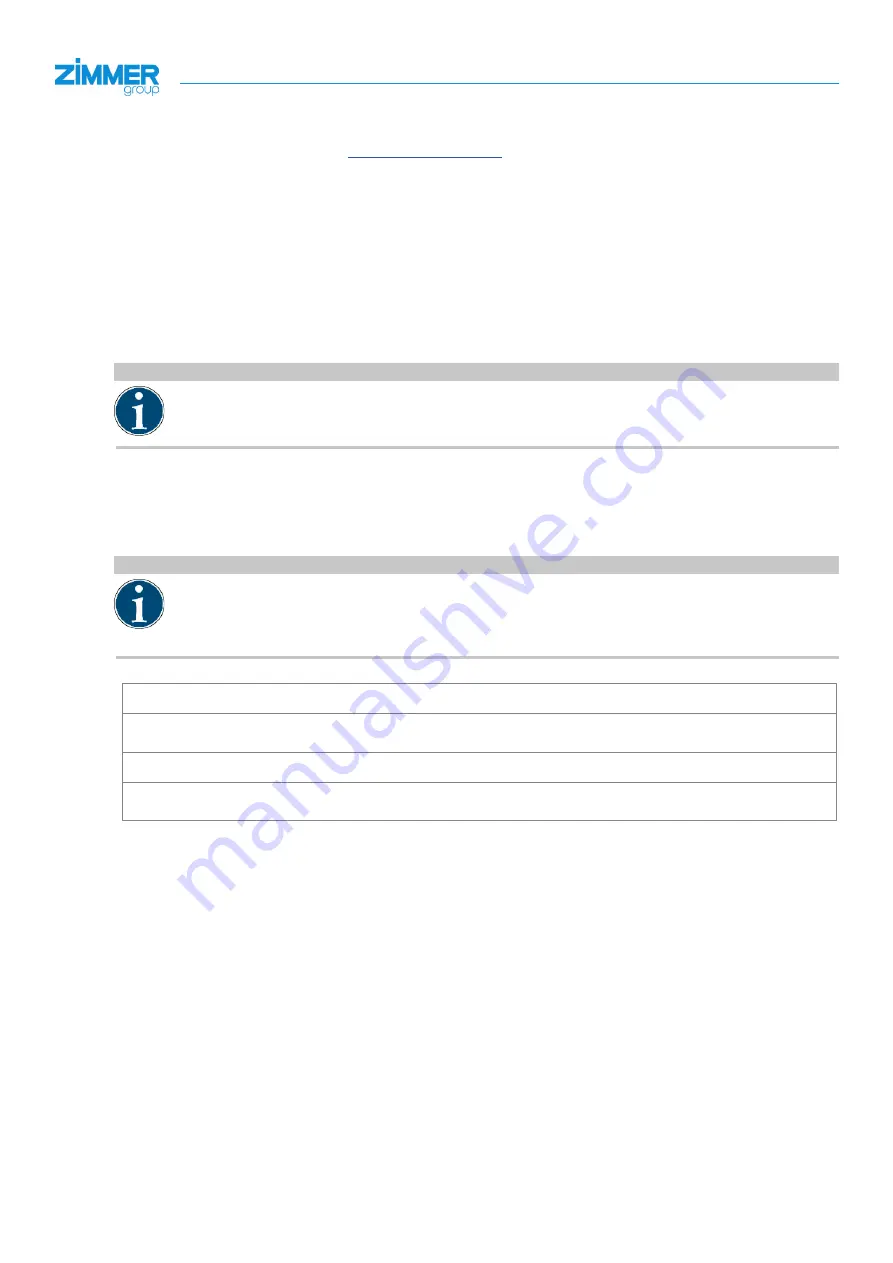
20
DDOC0021
1 / h
EN / 2020-08-15
Zimmer GmbH
•
Im Salmenkopf 5
•
77866 Rheinau, Germany
•
+49 7844 9138 0
•
+49 7844 9138 80
•
www.zimmer-group.com
INSTALLATION AND OPERATING INSTRUCTIONS:
Gripper, electric, GEP5000/GED5000 series
8.2.2 IODD import
► Importing the IODD (device description) into the control system.
Ö
Call up our website at
Ö
www.zimmer-group.com
Ö
Select the desired gripper and download the corresponding .zip file via the "Download IODD" link.
Ö
The “.zip file” is required for importing into the control system.
When the hardware configuration is complete and the IO-Link connection to the gripper is established, some
data must be visible in the process input data.
Ö
Some control systems demand a byte swap to bring this process data into a logical sequence.
► To determine whether a byte swap is necessary, you can view bit 6 (GripperPLCActive) in the "StatusWord".
► For this purpose, it is necessary to determine whether bit 6 is active in the first or second status byte.
Ö
If bit 6 is active in the first byte, the bytes already have the correct sequence and commissioning can
be continued.
Ö
If bit 6 is active in the second byte, a byte swap still has to be applied here.
Ö
For further information, refer to the "StatusWord" section.
INFORMATION:
It is mandatory to verify the process data.
The control of the gripper takes place via IO-Link by means of the cyclical process data as well as the acyclical
service data with a cycle time of 5 ms.
8.3 "Handshake" data transfer method
All process data that is transferred to the gripper and is described in the sections that follow must be transferred
using the "handshake" method.
INFORMATION:
This method is referred to as a "handshake" because it enables "clean" transfer.
The process data transfer takes place, so to speak, from "hand to hand" - from the control system to the
gripper.
The following steps are required for the "handshake":
The data transfer starts with the transfer of
"ControlWord" = 0x01
to the gripper.
Subsequently, the response of the gripper must be tested by means of
"Statusbit" 12 = TRUE
(data trans
-
fer OK).
Following this, the “ControlWord” = 0
can be sent, which ends the data transfer.
The operator automatically concludes the data transfer with the
“ControlWord” = 0x00
and the corre-
sponding response from the gripper via the
“Statusbit” 12 = FALSE
.