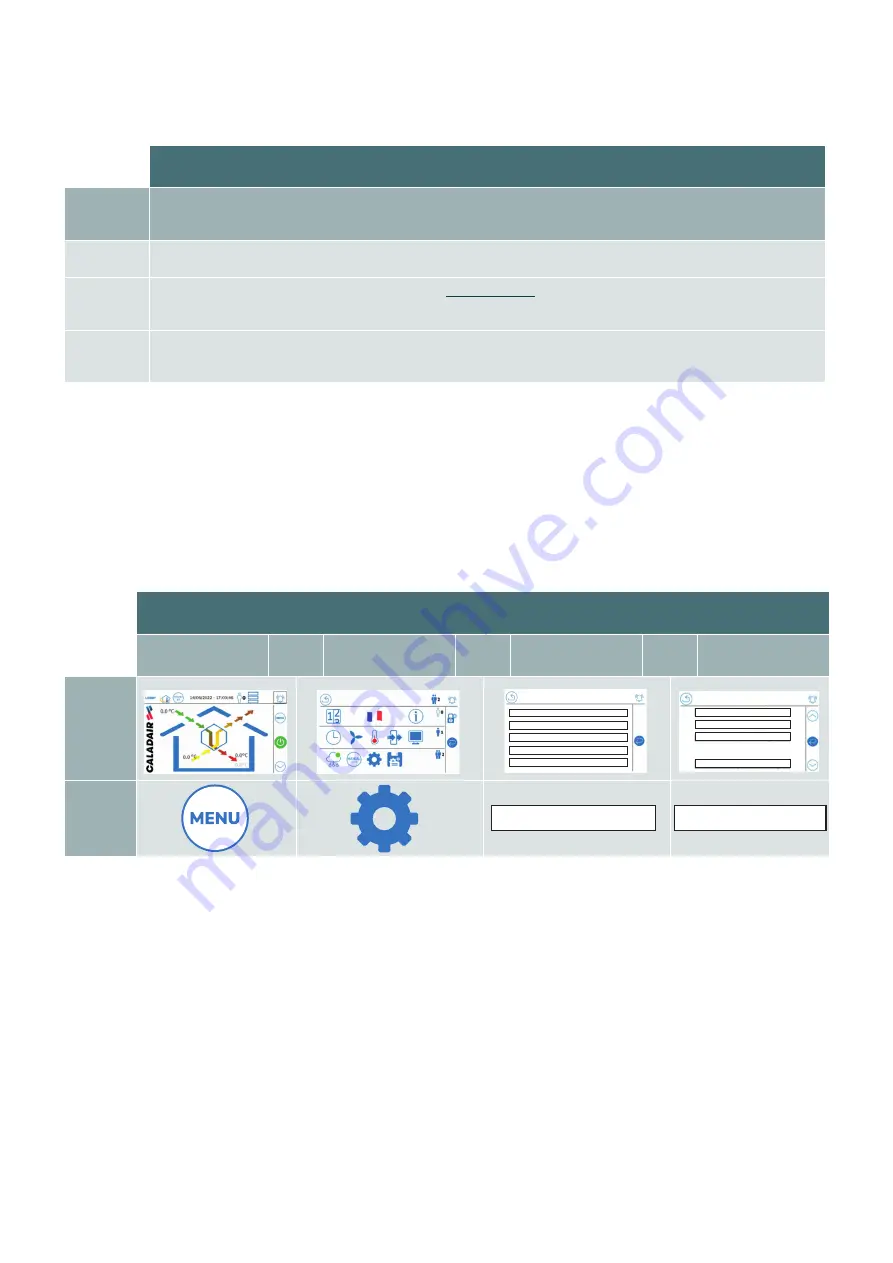
Zehnder EASY 5.0
58
The 3 CO
2
and offset terminals can be changed by the user.
When setting the time schedule, it is important to set only one time slot for reduced operation as all the offsets apply to
this operation. If a normal operating period is set, the CO
2
will not be effective and nor will the night cooling.
20. Control of the electric heating coil (BE)
20.1. Modulation of thermal output
The electric heating coil is managed by the heating sequence and therefore has its own PID control loop which
calculates a heating requirement from the supply (or return) temperature setpoint and the measured supply (or return)
temperature. This requirement is converted into a PWM (Pulse Width Modulation) control signal used to drive the solid
state power relays that provide power to the battery heating elements. The PWM signal period is 60 secs (not
adjustable).
The PWM value is directly proportional to the calculated heating requirement. The PWM is translated directly to the DO
output of the controller as follows:
QUATTRO
ppm CO
2
(adjustable)
Fan offset (m
3
/h)
(different for each machine model)
(adjustable value)
800
0
(no offset = reduced volume flow in MAC2 version of the corresponding AHU model)
900
Offset
1000
+Offset
800
2
1000
Value that depends on the AHU model to obtain the volume of normal operation in MAC2 version of the
corresponding AHU model)
See XV.11 Fan feedback and difference thresholds
Access path to the function (Access level: Expert)
Step 1
→
Step 2
→
Step 3
→
Step 4
From
screen
Area to
click
Actuators
Electric heating coil
Settings and configuration
Sensors
Alarms
PID loops
Functions
Actuators
Main menu
Actuator settings 2/2
Cooling
Bypass exchanger
Electric heating coil
Electric preheating coil
Z-MASTER-V1122-CSY-INM-Zehnder Easy5.0