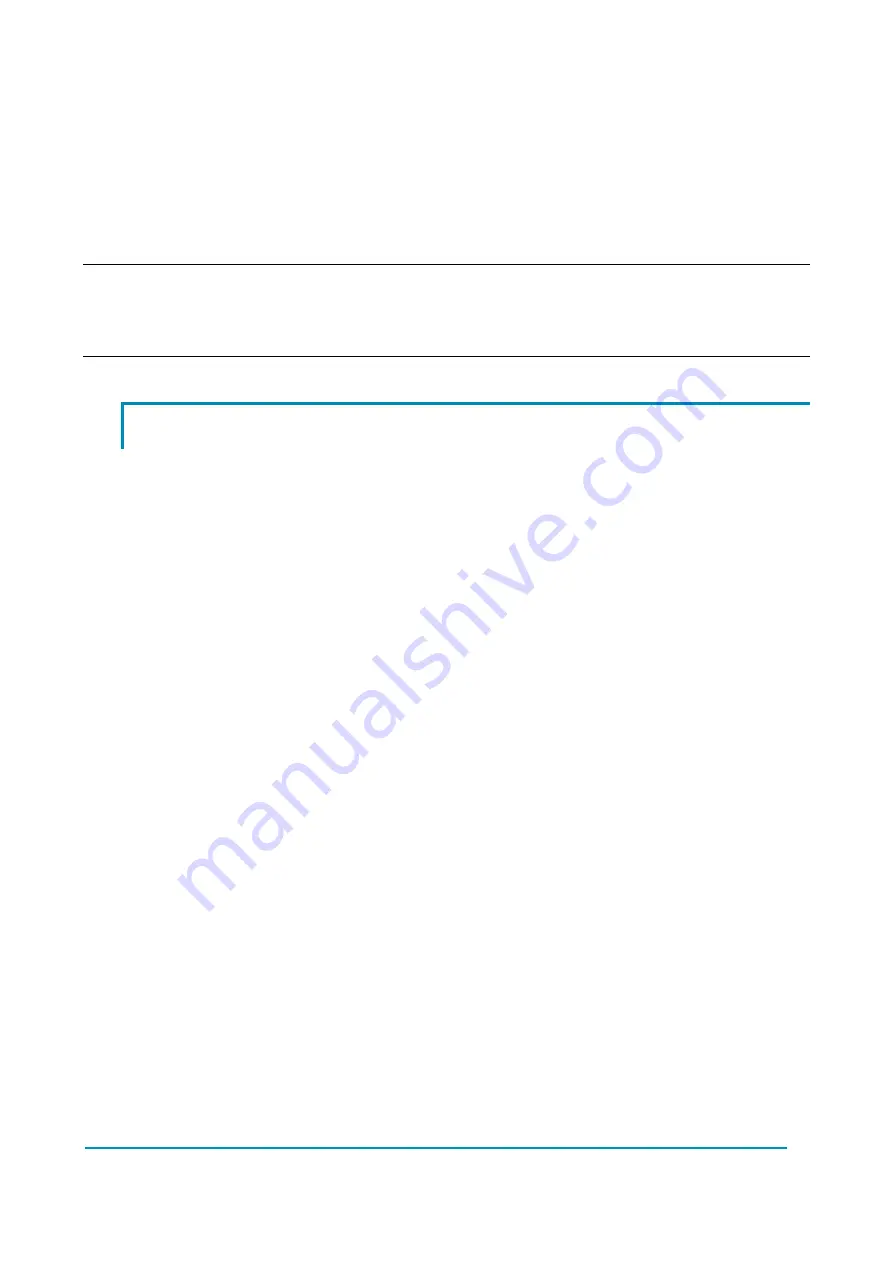
Page – 72/139
AFFZP0BB – ACE3 – User Manual
-
In HARDWARE SETTING increase the ABS.SENS. ACQ.ID parameter (the
motor current used for the open-loop phase) so to have more torque and
perhaps solve some friction problems (ID RMS MAX must be set
congruently).
-
If increasing ABS.SENS. ACQ.ID is not enough, increase the
ABS.SENS.A.KTETA parameter. It manages the speed in the open-loop
phase and in some situations faster speed can help to achieve a more even
rotation.
4
Offset angle can also be manually refined using the MAN.OFFSET ANGLE
parameter. However, sensor voltage range must be first acquired using the
automatic procedure.
7.5 Set-up procedure for pump inverter
This section describes the basic set-up procedure for the ACE3 inverter in pump
configuration. If you need to replicate the same set of settings on different
controllers, use the SAVE and RESTORE sequence (see chapter 8); otherwise go
down the following sequence.
-
In ADJUSTMENT, set BATTERY VOLTAGE according to your set-up (see
paragraph 7.2.3).
-
Check the wiring and that all commands are functioning. Use the TESTER
function to have real-time feedback about their state.
-
Perform the accelerator acquisition using the PROGRAM VACC procedure
(see paragraph 8.1).
-
Set the maximum current for lift and lowering in MAX. CURRENT TRA and
MAX. CURRENT BRK (see paragraph 7.2.1).
-
Set the motor-related parameters. It is suggested to discuss them with Zapi
technicians.
-
Set SET MOT.TEMPERAT according to the type of the motor thermal
sensor adopted.
-
Set the acceleration delay (ACCEL MODULATION and ACCEL DELAY
parameters). Test the behavior in both directions.
-
Set the FREQUENCY CREEP starting from 0.3 Hz. The pump should just
run when the request is active. Increase the level accordingly.
-
Set SPEED REDUCTION as required by your specifications.
-
Set the other performance-related parameters such as MAX SPEED LIFT,
1ST SPEED COARSE, 2ND SPEED COARSE, 3RD SPEED COARSE.
-
Set hydraulic-steering-related parameters, such as HYD SPEED FINE and
HYDRO TIME.
-
Test the pump in all operative conditions (with and without load, etc.).
At the end of your modifications, re-cycle the key switch to make them effective.
Содержание ACE3
Страница 14: ...Page 14 139 AFFZP0BB ACE3 User Manual 3 2 Connection drawing ACE3 Traction Standard...
Страница 15: ...AFFZP0BB ACE3 User Manual Page 15 139 3 3 Connection drawing ACE3 Traction Premium...
Страница 16: ...Page 16 139 AFFZP0BB ACE3 User Manual 3 4 Connection drawing ACE3 Pump Standard...
Страница 17: ...AFFZP0BB ACE3 User Manual Page 17 139 3 5 Connection drawing ACE3 Pump Premium...