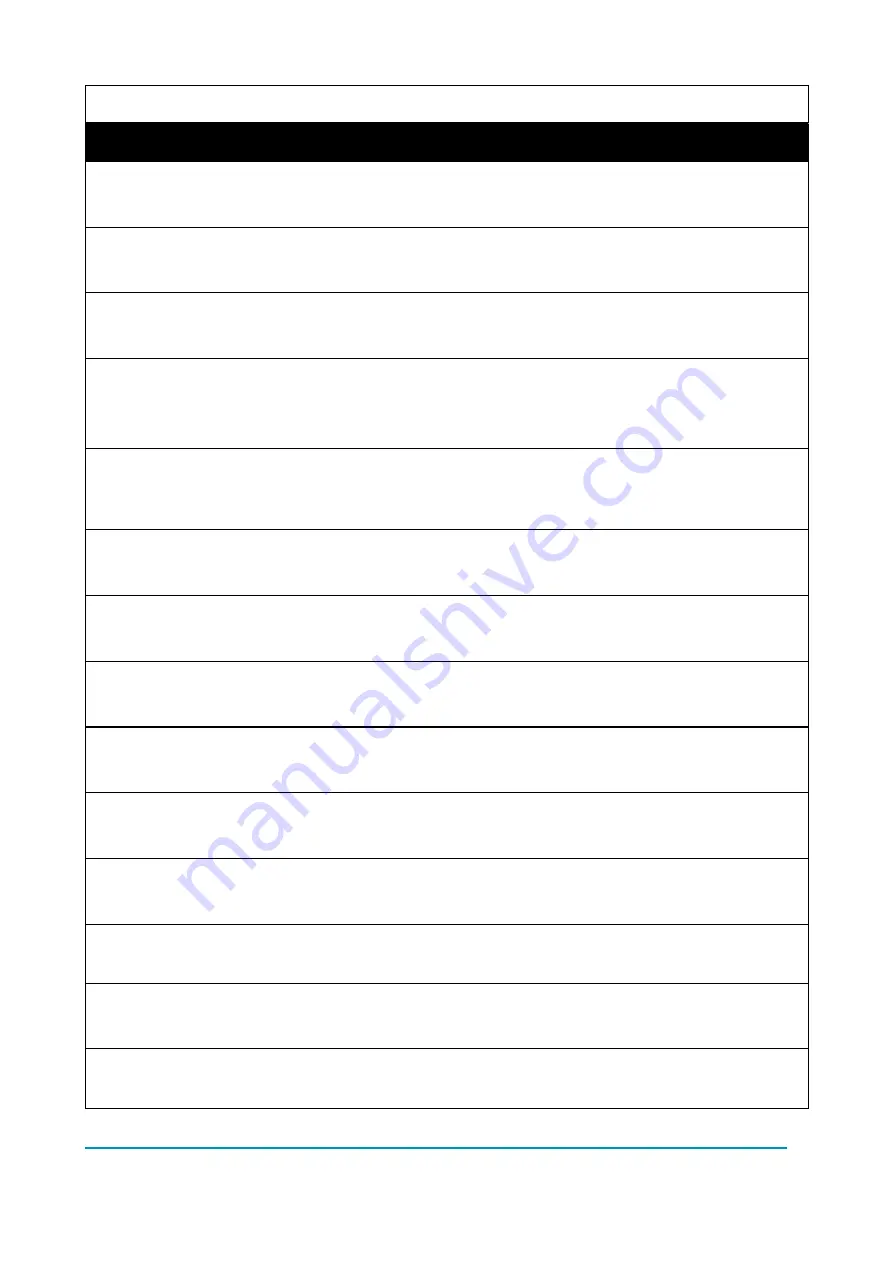
AFFZP0BB – ACE3 – User Manual
Page – 43/139
PARAMETER CHANGE
Parameter
Allowable range
Description
HYD PUMP SPEED
(P)
0% ÷ 100%
(by 1% steps)
This parameter defines the speed of the pump motor used for the
steering, when HYDRO FUNCTION is ON. It represents a
percentage of the maximum pump speed.
CUTBACK SPEED 1
(T, TM, P)
10% ÷ 100%
(by 1% steps)
This parameter defines the maximum speed performed when
cutback input 1 is active. It represents a percentage of TOP MAX
SPEED.
CUTBACK SPEED 2
(T, TM, P)
10% ÷ 100%
(by 1% steps)
This parameter defines the maximum speed performed when
cutback input 2 is active. It represents a percentage of TOP MAX
SPEED.
H&S CUTBACK
(T, TM)
10% ÷ 100%
(by 1% steps)
This parameter defines the maximum speed performed when the
Hard-and-Soft function is active. It represents a percentage of
TOP MAX SPEED.
Note: by default H&S function is not present on ACE3.
CTB. STEER ALARM
(T, TM)
0% ÷ 100%
(by 1% steps)
This parameter defines the maximum traction speed when an
alarm from the EPS is read by the microcontroller, if the alarm is
not safety-related. The parameter represents a percentage of TOP
MAX SPEED.
CURVE SPEED 1
(T, TM)
0% ÷ 100%
(by 1% steps)
This parameter defines the maximum traction speed when the
steering angle is equal to the STEER ANGLE 1 angle. The
parameter represents a percentage of TOP MAX SPEED.
CURVE CUTBACK
(T, TM)
1% ÷ 100%
(by 1% steps)
This parameter defines the maximum traction speed when the
steering angle is equal to the STEER ANGLE 2 angle. The
parameter represents a percentage of TOP MAX SPEED.
FREQUENCY CREEP
(T, TM, P)
0.6 Hz ÷ 25 Hz
(by steps of 0.1 Hz)
This parameter defines the minimum speed when the forward- or
reverse-request switch is closed, but the accelerator is at its
minimum.
TORQUE CREEP
(T, TM, P, CO)
0% ÷ 100%
(255 steps)
This parameter defines the minimum torque applied when torque
control is enabled and the forward- or reverse-request switch is
closed, but the accelerator is at its minimum.
MAX. CURRENT TRA
(T, TM, P, CO)
0% ÷ 100%
(by 1% steps)
This parameter defines the maximum current applied to the motor
during acceleration, as a percentage of the factory-calibrated
maximum current.
MAX. CURRENT BRK
(T, TM, P, CO)
0% ÷ 100%
(by 1% steps)
This parameter defines the maximum current applied to the motor
during deceleration, as a percentage of the factory-calibrated
maximum current.
ACC SMOOTH
(T, TM, P, CO)
1 ÷ 5
(by steps of 0.1)
This parameter defines the acceleration profile: 1 results in a
linear ramp, higher values result in smoother parabolic profiles.
INV SMOOTH
(T, TM, CO)
1 ÷ 5
(by steps of 0.1)
This parameter defines the acceleration profile performed when
the truck changes direction: 1 results in a linear ramp, higher
values result in smoother parabolic profiles.
STOP SMOOTH
(T, TM, P, CO)
3 Hz ÷ 100 Hz
(by steps of 1 Hz)
This parameter defines the frequency at which the smoothing
effect of the acceleration profile ends.
Содержание ACE3
Страница 14: ...Page 14 139 AFFZP0BB ACE3 User Manual 3 2 Connection drawing ACE3 Traction Standard...
Страница 15: ...AFFZP0BB ACE3 User Manual Page 15 139 3 3 Connection drawing ACE3 Traction Premium...
Страница 16: ...Page 16 139 AFFZP0BB ACE3 User Manual 3 4 Connection drawing ACE3 Pump Standard...
Страница 17: ...AFFZP0BB ACE3 User Manual Page 17 139 3 5 Connection drawing ACE3 Pump Premium...