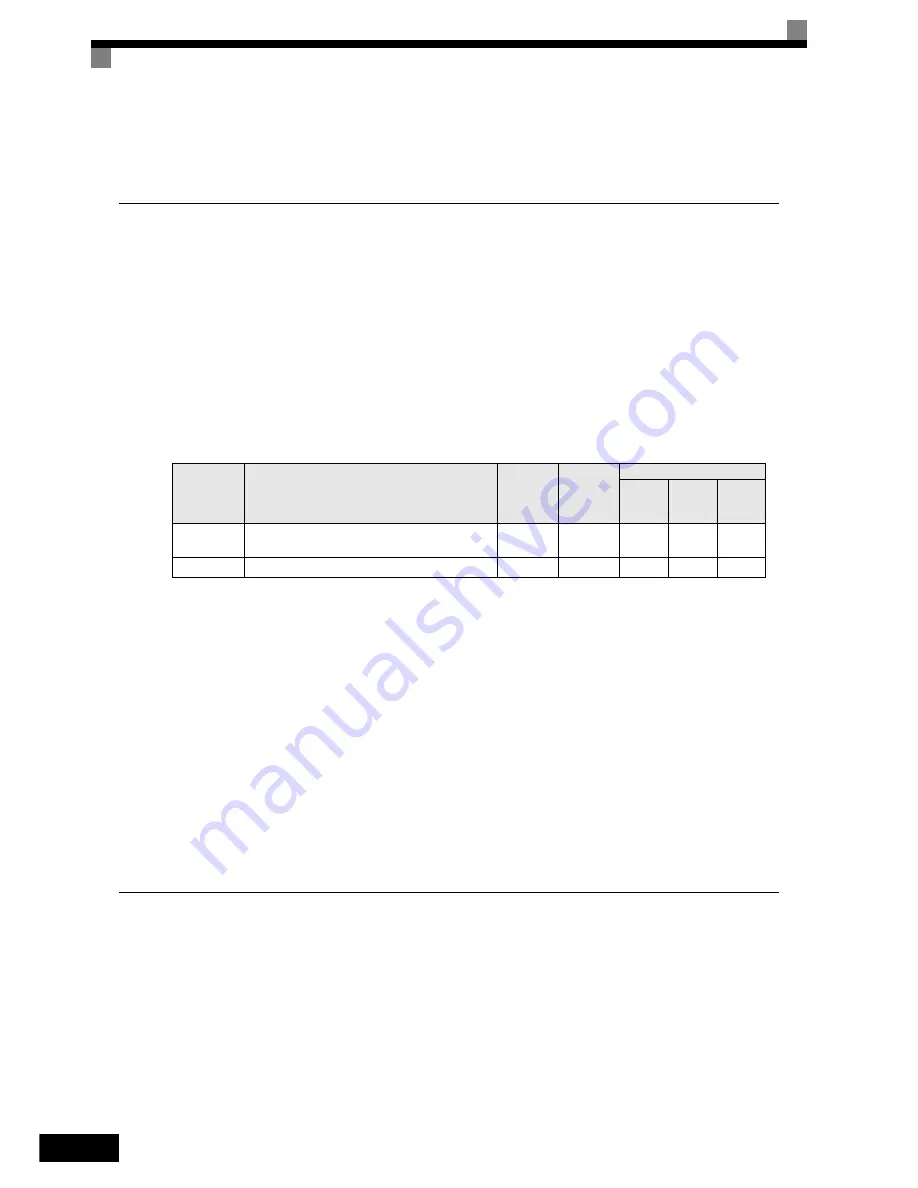
5
-34
Protective Functions
Preventing Motor Stalling During Operation
Stall prevention during operation prevents the motor from stalling by automatically lowering the inverter out-
put frequency when a transient overload occurs while the motor is operating at a constant speed.
Stall prevention during operation can be enabled in V/f control only. If the Inverter output current continues to
exceed the setting in parameter L3-06 for 100 ms or longer, the motor speed is reduced. Enable or disable the
stall prevention using parameter L3-05. Set the according deceleration times using C1-02 (Deceleration time
1) or C1-04 (Deceleration Time 2).
If the Inverter output current reaches the set value in L3-06 – 2%, the motor will accelerate again to the set fre-
quency.
Related Parameters
Precautions
If the motor capacity is smaller than the Inverter capacity or the motor stalls when operating at the factory set-
tings, lower the stall prevention level during operation.
Setting Precautions
•
Set the parameters as a percentage taking the inverter rated current to be 100%.
•
Do not increase the stall prevention level unnecessarily. An extremely high setting can reduce the inverter
lifetime. Also do not disable the function.
•
If the motor stalls with the factory settings check the V/f pattern (E1-
) and the motor setup (E2-
).
•
If the stall level has to be increased very much to get the elevator running check the mechanical system or
consider to use a one size bigger inverter.
Motor Torque Detection / Stacked Car Detection
The inverter provides a torque detection function to detect overtorque or undertorque. An alarm signal can be
output to the digital output terminals M1-M2, M3-M4, or M5-M6.
To use the overtorque/undertorque detection function, set B, 17, 18, 19 (overtorque/undertorque detection
NO/NC) in one of the parameter H2-01 to H2-03 (digital output terminals M1 to M6 function selection).
Overtorque/undertorque is detected by:
•
observing the output current in V/f control (the inverter rated output current is equal to 100%).
•
observing the torque reference value in Open Loop and Closed Loop Vector control (the motor rated torque
is equal to 100%).
Parameter
No.
Name
Factory
Setting
Change
during
Operation
Control Methods
V/f
Open
Loop
Vector
Closed
Loop
Vector
L3-05
Stall prevention selection during running function
selection
1
No
A
No
No
L3-06
Stall prevention level during running
150%
No
A
No
No
http://nicontrols.com
Содержание Varispeed L7
Страница 3: ...http nicontrols com...
Страница 55: ...2 30 http nicontrols com...
Страница 129: ...4 62 http nicontrols com...
Страница 197: ...5 68 http nicontrols com...
Страница 219: ...6 22 http nicontrols com...
Страница 243: ...9 14 http nicontrols com...