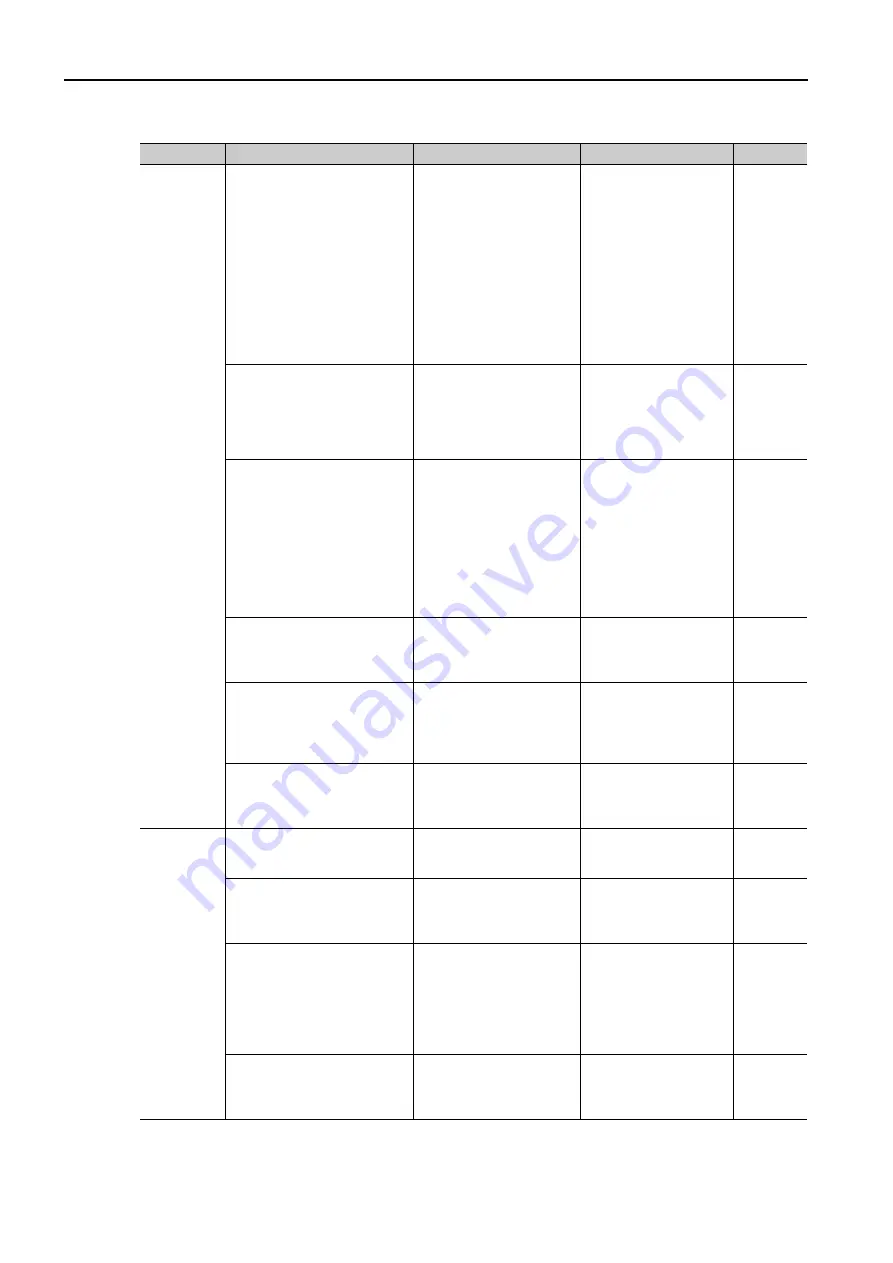
8.3 Troubleshooting Based on the Operation and Conditions of the Servomotor
8-60
Position
Deviation
(without
Alarm)
The encoder was subjected
to excessive vibration or
shock.
Turn OFF the power sup-
ply to the servo system.
Check to see if vibration
from the machine
occurred.
Check the Servomotor
installation (mounting sur-
face precision, securing
state, and alignment).
Check the linear encoder
installation (mounting sur-
face precision and secur-
ing method).
Reduce machine vibra-
tion. Improve the
mounting state of the
Servomotor or linear
encoder.
–
The coupling between the
machine and Servomotor is
not suitable.
Turn OFF the power sup-
ply to the servo system.
Check to see if position
offset occurs at the cou-
pling between machine
and Servomotor.
Correctly secure the
coupling between the
machine and Servomo-
tor.
–
Noise interference occurred
because of incorrect I/O sig-
nal cable specifications.
Turn OFF the power sup-
ply to the servo system.
Check the I/O signal
cables to see if they sat-
isfy specifications. Use a
shielded twisted-pair wire
cable or a screened
twisted-pair cable with
conductors of at least
0.12 mm
2
.
Use cables that satisfy
the specifications.
–
Noise interference occurred
because an I/O signal cable
is too long.
Turn OFF the power sup-
ply to the servo system.
Check the lengths of the
I/O signal cables.
The I/O signal cables
must be no longer than
3 m.
–
An encoder fault occurred.
(The pulse count does not
change.)
–
Turn OFF the power
supply to the servo
system. Replace the
Servomotor or linear
encoder.
–
A failure occurred in the SER-
VOPACK.
–
Turn OFF the power
supply to the servo
system. Replace the
SERVOPACK.
–
Servomotor
Overheated
The surrounding air tempera-
ture is too high.
Measure the surrounding
air temperature around
the Servomotor.
Reduce the surround-
ing air temperature to
40
°
C or less.
–
The surface of the Servomo-
tor is dirty.
Turn OFF the power sup-
ply to the servo system.
Visually check the surface
for dirt.
Clean dirt, dust, and oil
from the surface.
–
There is an overload on the
Servomotor.
Check the load status
with a monitor.
If the Servomotor is
overloaded, reduce the
load or replace the
Servo Drive with a
SERVOPACK and Ser-
vomotor with larger
capacities.
–
Polarity detection was not
performed correctly.
Check to see if electrical
angle 2 (electrical angle
from polarity origin) at any
position is between
±
10
°
.
Correct the settings for
the polarity detection-
related parameters.
–
Continued from previous page.
Problem
Possible Cause
Confirmation
Correction
Reference