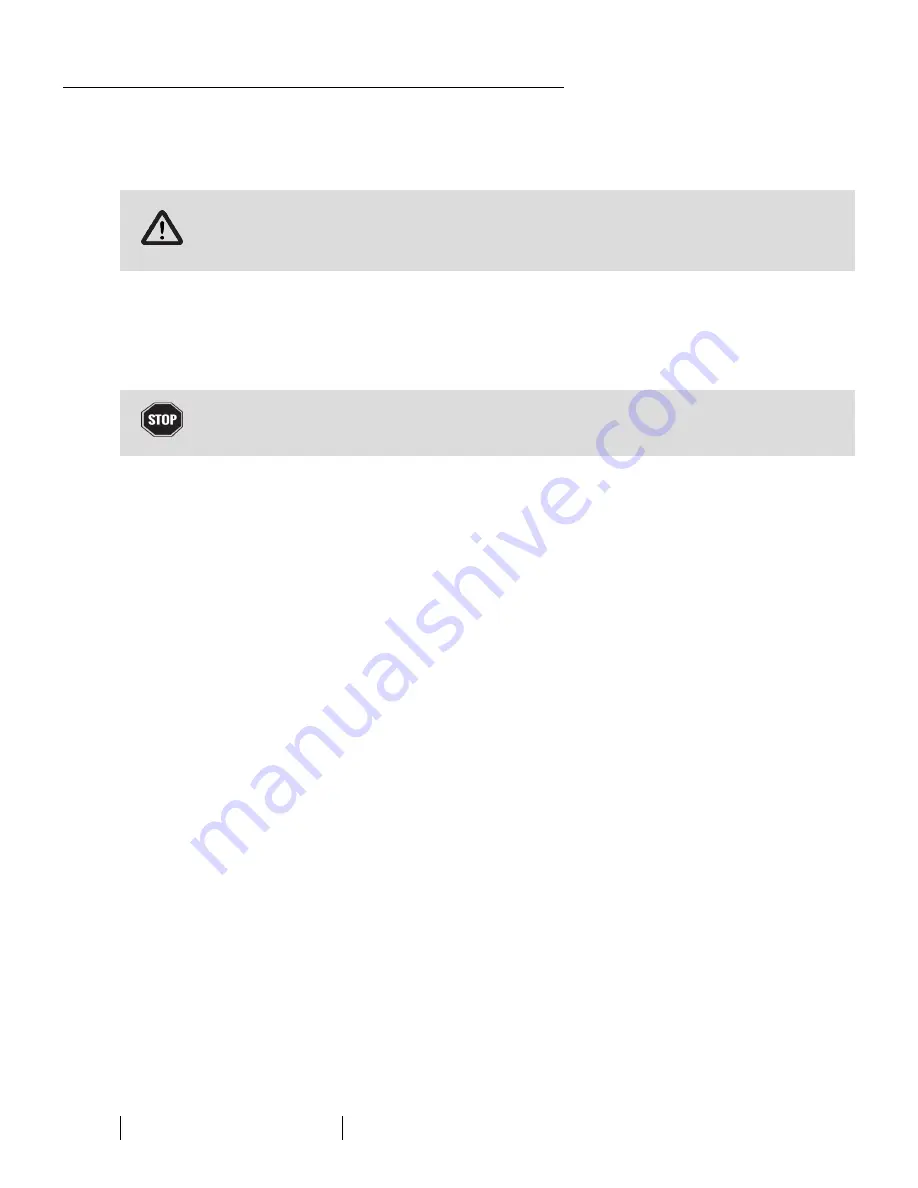
Using Pipeline Product (If Not Using Hydraulic Fluid or an Auxiliary Gas)
24.
Ensure that vent/relief valve B is closed (
25.
Slowly open the pipeline isolation valve. Check for leaks and repair as necessary.
26.
Slowly open isolation valve A (
). The insertion shaft will begin to insert into the pipeline.
Once the insertion shaft begins to insert, do not open the valve any further. The insertion shaft should be inserted slowly and
smoothly. Opening the valve too quickly or too much may cause the insertion shaft to insert into the pipeline too quickly and
may result in damage to the unit.
27.
Using the alignment indicator rod, guide the shaft slowly into the pipeline. The alignment indicator rod should be
parallel to the pipeline.
28.
As necessary, align the lock collar holes with the alignment nuts on the top cap (
).
29.
Once the lock collar seats on the alignment nuts, return the hex bolts to the alignment nuts and tighten firmly (
).
DO NOT stop applying pressure to the insertion shaft until the lock collar has been secured to the alignment nuts.
30.
Once the lock collar is secured to the top cap, close isolation valve A (
).
31.
Open vent/relief valve B to relieve pipeline pressure (
). The insertion shaft will remain in the pipeline, held in
place mechanically by the lock collar.
32.
Close vent/relief valve B (
33.
Continue to step 34 to complete installation.
14
IOM-161
MODEL: INFLOW™ ACE WITH AI CONTROL™
REV: D
13839 West Bellfort Street, Sugar Land, TX 77498
welker.com
Service Department 281.491.2331