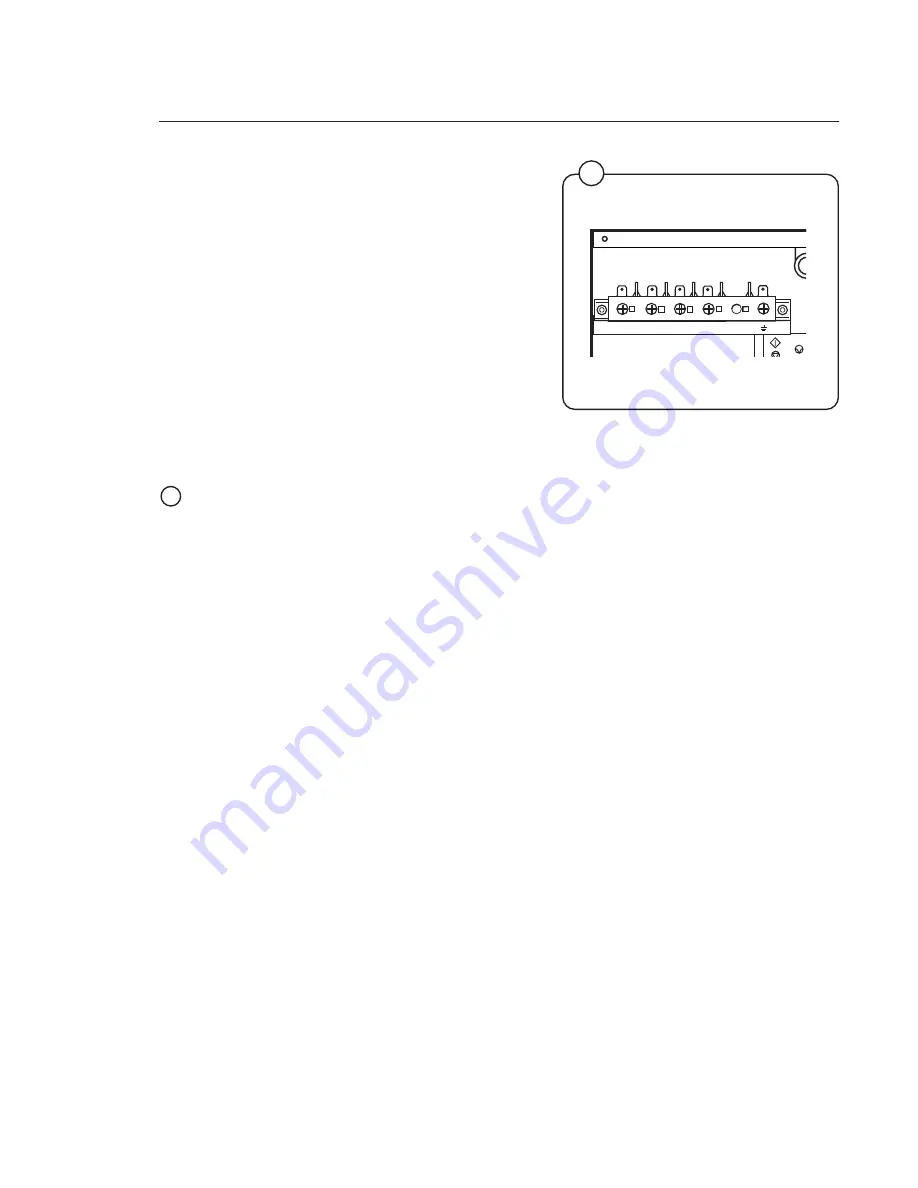
15
Installation
Electrical installation
Although the machines are fitted with a thermal
overload in the motor windings and fuses for the
control circuit, a separate circuit breaker must be
installed for each machine.
For proper overcurrent protection, check the data
plate at the rear of the machine. Also consult
local electrical code for special requirements.
The machine is equipped with a control circuit
transformer, mounted on the control unit and
connected for 220 volt operation.
If your incoming voltage is below 210 volts move
the wire connection to the 208 volt tab on the
transformer. If it is above 230 volts move the wire
to the 240 volt tab on the transformer.
Connect L1, L2 and ground wires according to
the markings of the terminal block. The cable is
to hang in a large loose loop, supported by the
clamp below the terminal block.
11
4940 A
Fig.
11
L1
L2
Содержание EXSM 230 S
Страница 4: ......
Страница 6: ......
Страница 32: ...32 Mechanical and electrical design Control unit ...
Страница 93: ...93 Trouble shooting If machine vibrates excessively A Tighten mounting bolts Fig 101 101 2408 ...
Страница 94: ......
Страница 123: ......