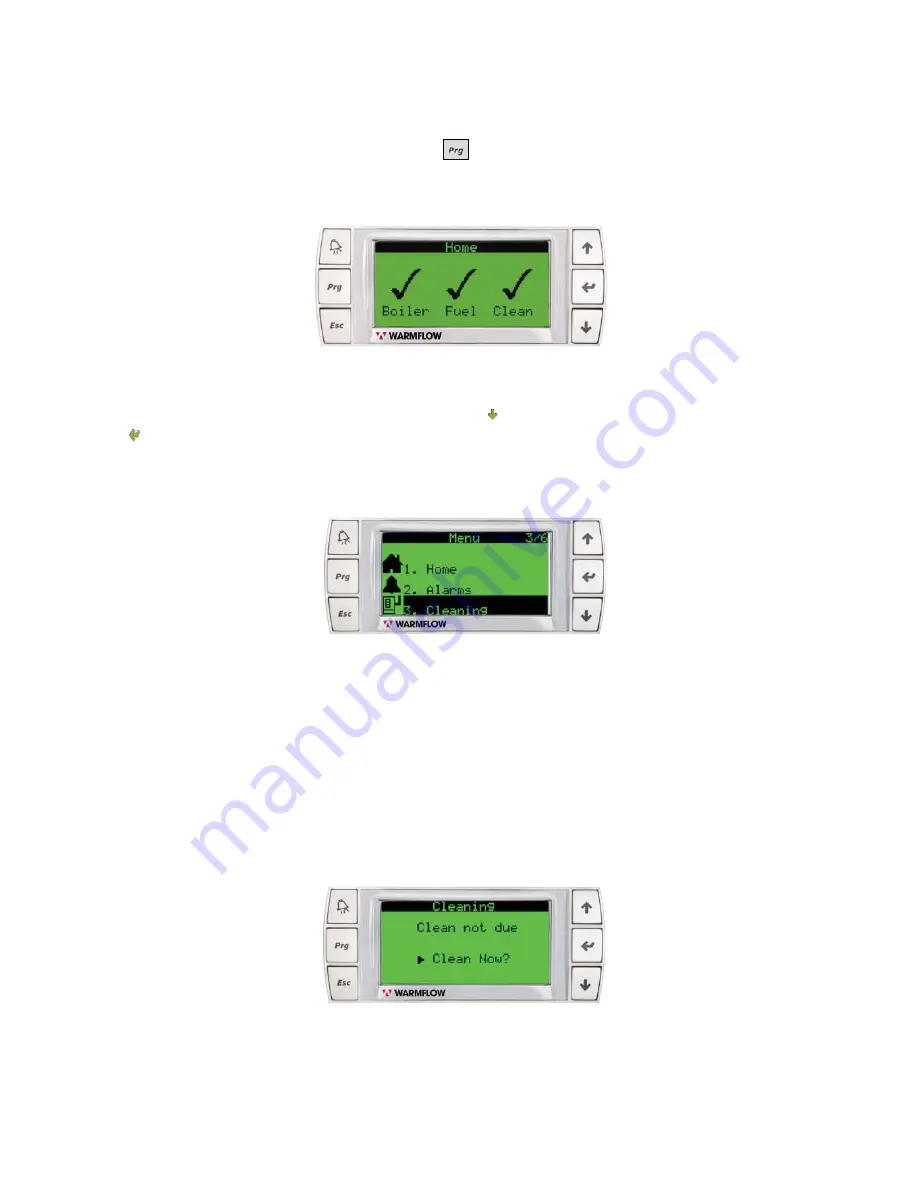
21
2.3.2 Cleaning Status
The cleaning status of the appliance can be viewed at any time.
From the home screen (Figure 24), press the
‘Program key’ to view the main menu.
Scroll to “3. Cleaning” in the Main Menu using the
‘Down Arrow’ and confirm selection using
the ‘Enter key’. (Figure 25)
The cleaning status screen should now be displayed.
If the cleaning status screen in Figure 26 is displayed, a scheduled clean is not yet due.
Insufficient operating hours have elapsed for the cleaning scheduler to trigger a cleaning alert.
Figure 24: Home Screen
Figure 25: Main Menu - Cleaning
Figure 26: Cleaning Status – Not Due
Содержание WS18
Страница 85: ...84 INTENTIONALLY LEFT BLANK...
Страница 97: ...96 9 APPENDIX A SUPPLEMENTARY INSTALLATION AND OPERATING INSTRUCTIONS FOR THE UK MARKET...
Страница 105: ...104 10 APPENDIX B CUSTOMER CONNECTION WIRING SCHEMATIC...
Страница 106: ...105...