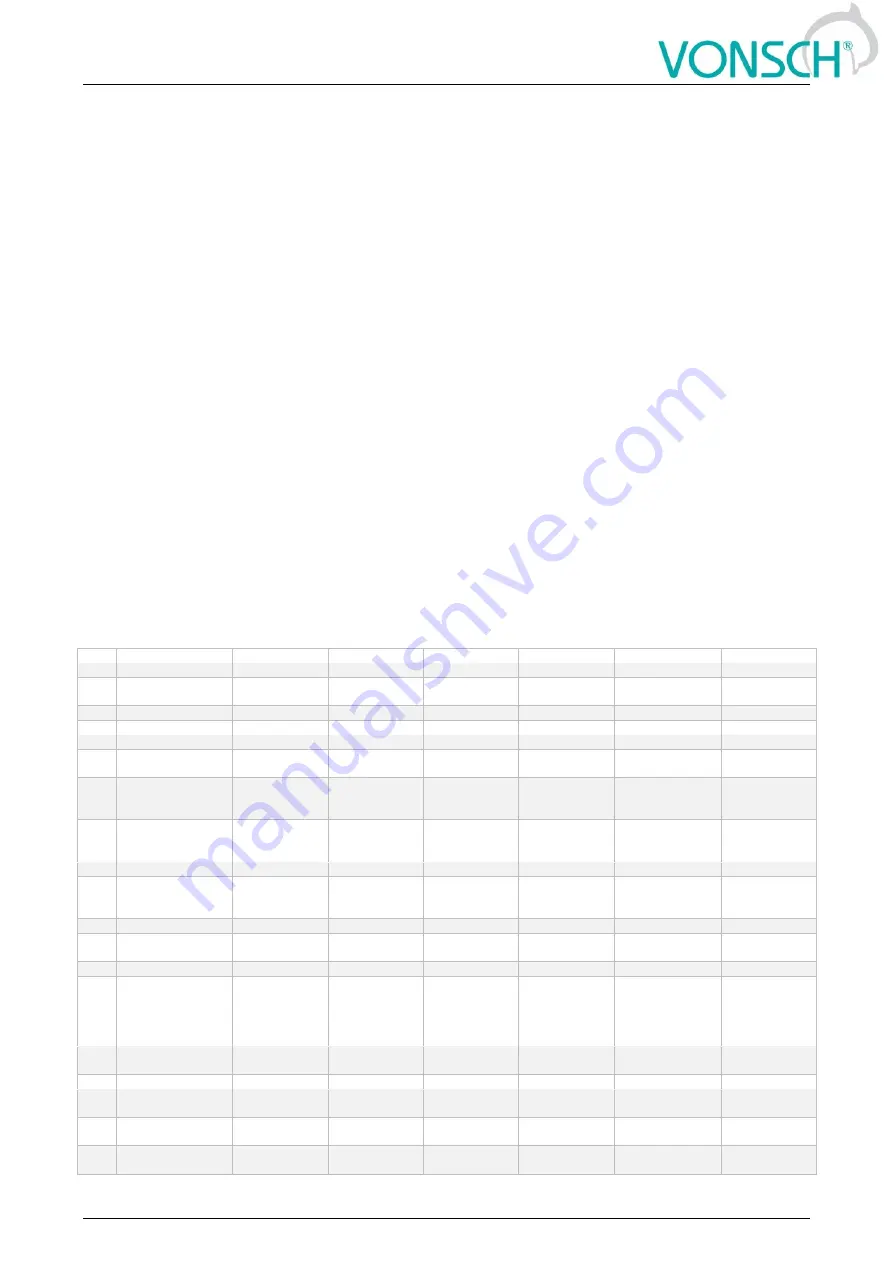
UNIFREM v.3.41x
10 May 2017
Page 38 from 180
In the second step, the converter asks for motor nameplate data. After selecting the power, the
nearest motor macro is applied, which preconfigures some system parameters.
When changing power, motor voltage or power factor, the system automatically recalculates the
nominal motor current to estimated value from the power equation. This automatic preset is
suitable for estimating the nominal current in the case where it is not available, e.g. the motor is
physically inaccessible or rewound and nameplate data do not match. After you manually change
the nominal current value, this value will not be recalculated anymore.
Motor overloading [27]
This parameter is used to preset the motor temperature model. When selecting the "Self-cooling",
converter uses thermal model considering its own cooling system, where the cooling effect
increases with speed. In case of using "Forced cooling" thermal model considers the forced
cooling, the effect is constant. The option "Not evaluated" is recommended where the thermal
model should not be evaluated, e.g. when the motor is well cooled or there is another thermal
protection. Setting the External Thermal Protection is out of scope of the wizard, it can be set up
later.
Sine filter [237]
Is there a sine filter connected between the converter and the motor?
7.1.4 Application macros
UNIFREM offers 5 application macros. They are used to preset some of the essential parameters
required for the application. Complete list of these parameters can be found in Table 1 below. The
preset value does not need to be suitable for all variants of the application, however it is very
simple to change it as needed.
ID
Parameter
Pump
Fan
Compressor
Heavy Load
Conveyor/travel
Lift
23 Operation mode
Variable load
Variable load
Constant load
Constant load
Constant load
Constant load
24 Permanent
current
Service
settings
Service
settings
Service
settings
Service
settings
Service settings
Service
settings
347 V/f Type
ST controller
ST controller
ST controller
ST controller
ST controller
ST controller
91 V/f exponent
1.5
1.5
1
1
1
1
98 Frequency shift
10Hz
10Hz
40Hz
35Hz
35Hz
35Hz
352 Max. current
controller
Motoric
Auto adaptivity
Motoric
Auto adaptivity
Motoric
Motoric
Auto adaptivity
-
-
5 Max. mot.
current
Nom. motor
current
(ID151)
Nom. motor
current
(ID151)
Max. inv.
current
Max. inv.
current
Max. inv. current
Max. inv.
current
549 Max. regen.
current
Same as Max.
mot. current
ID5)
Same as Max.
mot. current
ID5
Same as Max.
mot. current
ID5
Same as Max.
mot. current
ID5
Same as Max.
mot. current ID5
Same as Max.
mot. current
ID5
110 Min. frequency
20
20
0
0
0
0
111 Max. frequency
Nom. motor
frequency
(ID4)
Nom. motor
frequency
(ID4)
Nom. motor
frequency
(ID4)
Nom. motor
frequency
(ID4)
Nom. motor
frequency (ID4)
Nom. motor
frequency
(ID4)
116 Ramp-up 1 time
20
60
5
15
10
5
119 Ramp-down 1
time
20
60
5
15
10
5
807 Quick reverse
100%
100%
100%
100%
100%
100%
766 Power restriction
(PR)
- overload
- cooler
temperature
- overload
- cooler
temperature
- motor
overload
- overload
- cooler
temperature
- motor
overload
- overload
- cooler
temperature
- motor
overload
-
-
748 Kinetic backup
(KB)
Turned on
Turned on
Turned off
Turned off
Turned off
Turned off
374 Flying start
Turned off
Turned off
Turned off
Turned off
Turned off
Turned off
346 Brake module
Turned off
Turned off
Turned off
Turned off
Turned on when
running
Turned on
when running
195 Freq. reverse
source
No reverse
No reverse
No change
No change
No change
No change
163 STC Current
0.8 x inverter
rated current
0.8 x ID155
60s inverter
maximum
60s inverter
maximum
60s inverter
maximum
60s inverter
maximum
Содержание Quatrofrem Series
Страница 2: ...UNIFREM v 3 41x 10 May 2017 Page 2 from 180...
Страница 127: ...UNIFREM v 3 41x 10 May 2017 Page 127 from 180...