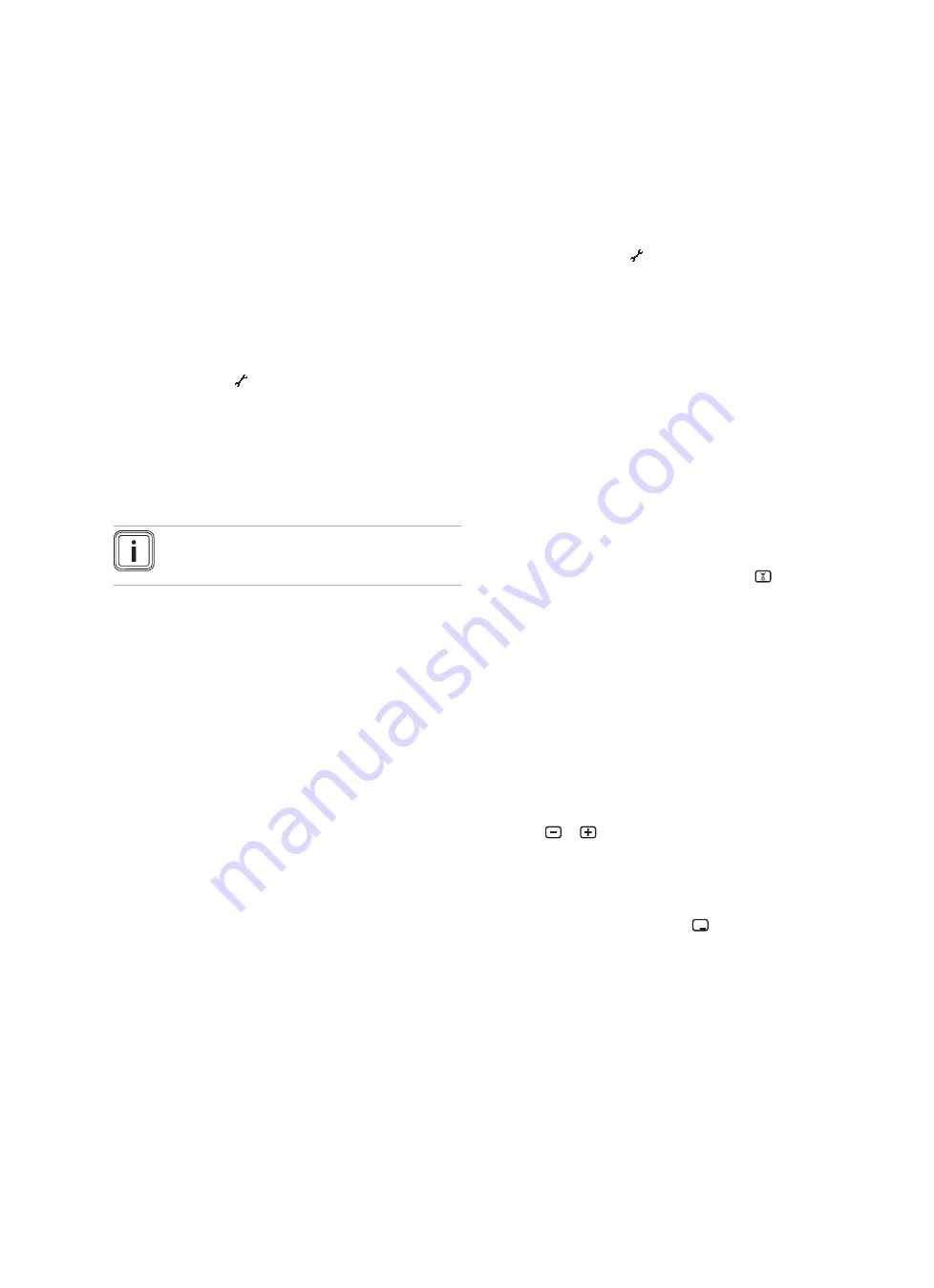
9 Handing over to the end user
28
Installation and maintenance instructions ecoTEC plus 0020261188_00
8.2.6
Setting the maximum flow temperature
You can use diagnostics code
D.071
to set the required
maximum flow temperature for the heating mode (factory
setting: 75 °C).
8.2.7
Setting the return temperature control
If the product is connected to an underfloor heating system,
the temperature control setting can be changed from flow
temperature control (factory setting) to return temperature
control using diagnostics code
D.017
.
8.3
Setting the maintenance interval
If you set the maintenance interval, after a configurable num-
ber of burner operating hours, the message that the product
must be serviced appears in the display, together with the
maintenance symbol
.
▶
Use diagnostics code
D.084
to set the operating hours
until the next maintenance work is due.
You can set the operating hours in increments of ten from 0
to 3010 h (hours).
If you do not set a numerical value but do set the symbol "
–
",
the function
Maintenance messages
is not active.
Note
On completion of the set operating hours, you
must set the maintenance interval again.
9
Handing over to the end user
1.
When you have finished the installation, attach the
sticker supplied in the end user's language to the front
of the product.
2.
Explain to the end user how the safety devices work
and where they are located.
3.
Inform the end user how to handle the product. Answer
any questions the end user may have. In particular,
draw attention to the safety warnings which the end
user must follow.
4.
Inform the end user that they must have the product
maintained in accordance with the specified intervals.
5.
Pass all of the instructions and documentation for the
product to the end user for safe-keeping.
6.
Instruct the end user about measures taken to ensure
the combustion air supply and flue system. Point out,
in particular, that the end user must not make any
changes, however minor.
10 Troubleshooting
You can find an overview of the fault codes in the appendix.
Fault messages
–
Overview (
→
Page 43)
10.1
Contacting your service partner
If you contact your service partner, if possible, please men-
tion
–
The fault code that is displayed (
F.xx
),
–
The product status that is displayed (
S.xx
).
10.2
Calling up service messages
If the maintenance symbol
appears in the display, there is
a service message that has to be called up.
The maintenance symbol appears if you have set a mainten-
ance interval, for example, and it has elapsed. The product is
not in fault mode.
▶
To obtain more information about the service message,
call up the
Live Monitor
. (
→
Page 19)
10.3
Reading off the fault codes
If a fault occurs in the unit or in the system, the display
shows an
F.xx
code.
Fault messages
–
Overview (
→
Page 43)
Fault codes have priority over all other displays.
If multiple faults occur at the same time, the display shows
the corresponding fault codes for two seconds each in se-
quence.
▶
Eliminate the fault.
▶
To restart the product, press the reset button
( Oper-
ating instructions).
▶
If you are unable to remedy the fault and the fault recurs
despite reset attempts, contact customer service.
10.4
Querying the fault memory
Menu
→
Installer level
→
Fault list
The product has a fault memory. You can use this to query
the last ten faults that occurred in chronological order.
The display shows:
–
Number of faults that occurred
–
The fault that is currently selected with fault number
F.xx
–
A plain text display explaining the fault.
▶
Use the
or
button to display the last ten faults that
occurred.
Fault messages
–
Overview (
→
Page 43)
10.5
Resetting the fault memory
▶
To delete the fault memory, press
(
Delete
,
OK
) twice.
10.6
Performing diagnostics
▶
You can use the diagnostics codes during fault dia-
gnostics to change individual parameters or to display
further information. (
→
Page 26)