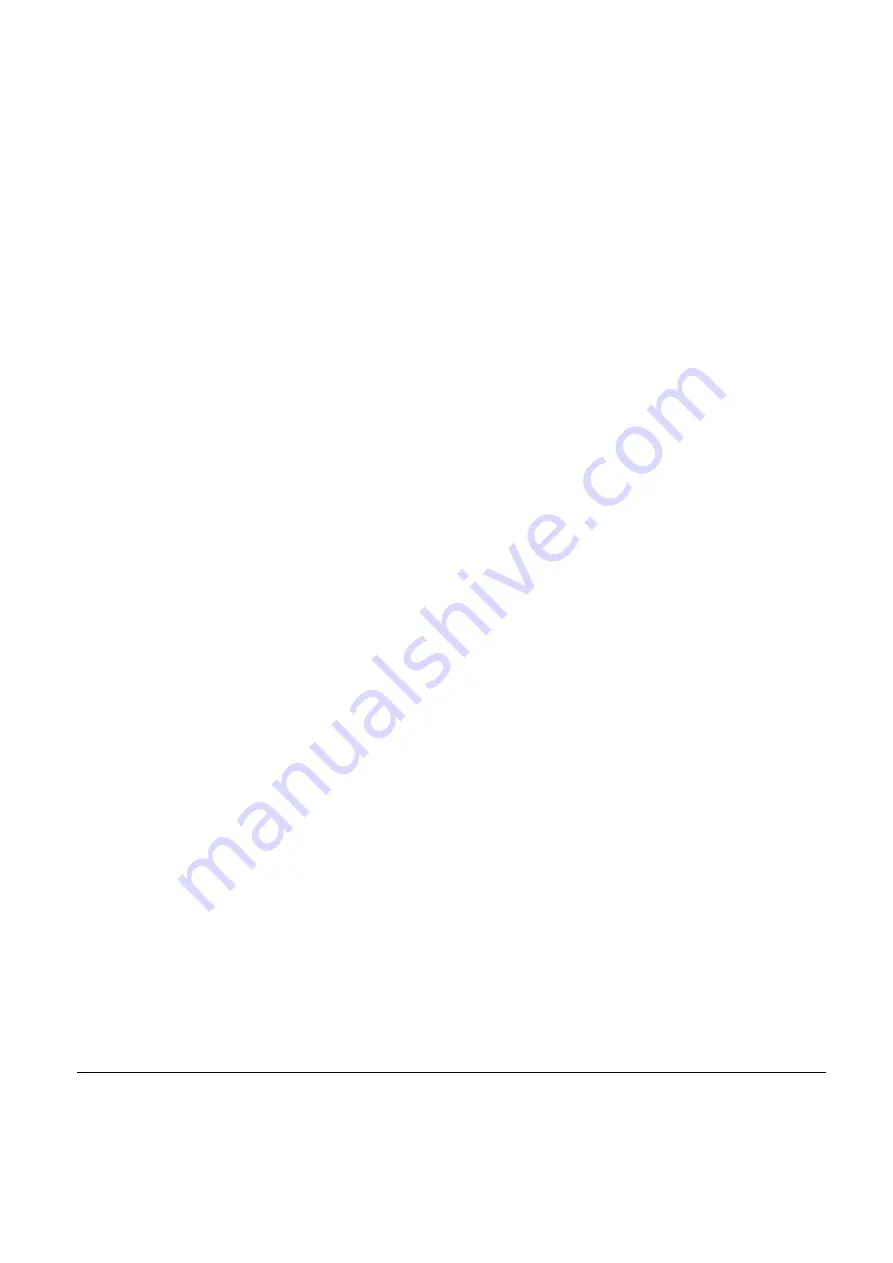
ULB PROPRIETARY RIGHTS NOTICE
- This document contains the confidential and proprietary information of ULB. You may not possess,
use, copy or disclose this document or any information in it for any purpose without express written permission. Neither receipt from any source,
nor possession of this document, constitutes such permission. Possession, use, copying or disclosure by anyone without express written
permission of ULB is not authorized and may result in criminal and/or civil liability.
U:\ILB\5_Technical Manual\TLB-R1000-480-OS_NO ALL\TLB-R1000_480_MANUAL_Rev03.docx
Page
30
of
35
Daily Maintenance Prior to Operation
1. Inspect and remove any restrictions and/or obstructions to cold-air intake and hot-air exhaust of the
Load Bank unit.
2. Check screens to make sure objects have not blocked/entered openings.
3. Verify the direction of the airflow is in the proper direction from cold-air intake to hot-air exhaust.
4. Verify that there is no possibility of re-circulation of hot-air exhaust to cold-air intake.
Quarterly Maintenance (every three months)
1. Remove all exterior access panels to Load Bank enclosure (including air intake and exhaust
covers).
2. Inspect the intake and exhaust covers. Blow or brush away any noticeable dirt or debris from air
intake and exhaust openings. Ensure covers are functional and free of debris. Replace any respective
panel that is compromised or damaged.
3. Clean any and all dirt and/or debris from the interior of the entire Load Bank. Do not exceed 40 PSI
when using clean, dry, compressed air for blowing and removing dust and debris.
4. Inspect blower motor and fan blade, clearing any debris or removing any obstruction. Check fan
blade for balance and all respective fan blade and motor mounting hardware for tightness. Torque to
proper values of tightness as required.
5. Inspect all resistor elements ensuring all hardware is tightened and elements are clear and free of
debris.
6. Inspect all resistors for mechanical and structural integrity and location. Replace any excessive
sagging resistor elements, ceramics and support rods. Replace any and all broken or cracked
termination ceramics, and ceramics on resistor support rods as required.
7. Inspect all termination ceramic insulators at resistor case ends (both sides) for breaks or cracks and
replace as necessary.
8. Inspect all support rod ceramic insulators for breaks or cracks and replace as necessary.
9. Inspect the entire inside of the enclosure for loose hardware or loose connections and tighten to
proper torque values as required.
10. Inspect all load and control wiring for signs of insulation failure or breakdown.
11. Inspect for any signs of heat stress on connections and terminals. This could be a sign of loose
hardware or corroded/oxidized connections. Repair and replace connection hardware as required.
12. Inspect all electrical connections to terminal blocks, main input load bus bars, fuses mounted to
bus bars, all resistor connections for corrosion and oxidation. Clean connections and replace hardware
as required. Tighten as necessary.
13. Inspect all load step contactors. Inspect magnetic contactor coils for oxidation and rust. Inspect
contacts that carry load if pitted, rusted or corroded. Contacts must all move freely and properly seal
when closed. Replace as necessary.
14. When replacing current transformers, mark all leads before removing to ensure proper phasing of
new current transformer. Never leave the secondary of a current transformer un-shunted.
15. Reinstall all covers ensuring all materials are well in place and all hardware is properly tightened.
16. Verify Airflow protection circuit. This can be done when unit is powered up for operation with all
access panels closed and in place, and blocking off the cold-air intake and/or hot-air exhaust.
17. Check all indicator lamps on Operator Control unit (replace as necessary).
18. Blower motor should be lubricated per manufacturer’s requirements as noted on motor nameplate.