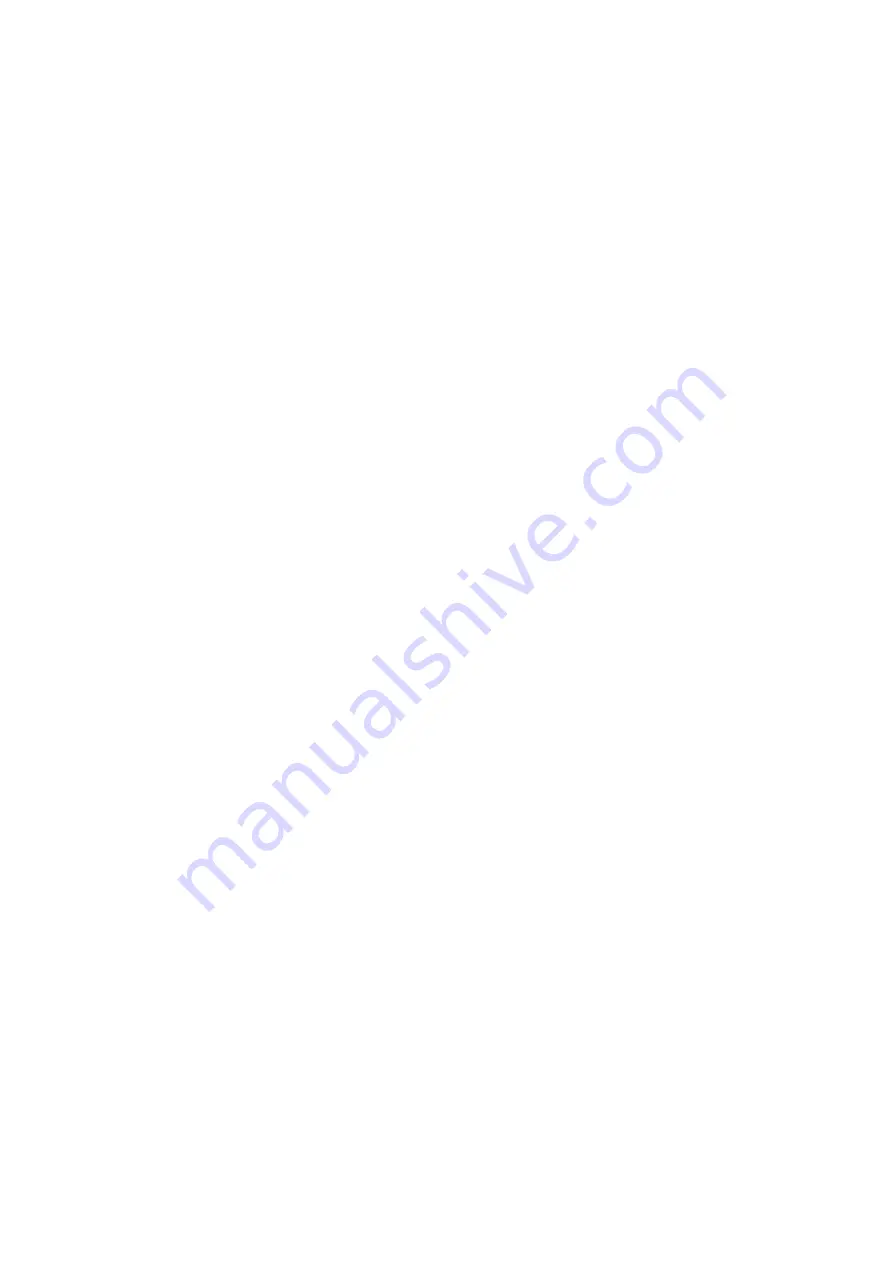
87
arm to trigger collision protection. If the load or installation direction
is not set accurately, it may cause false alarms. During certain high
loads or high speed movements, if you confirm that the load or
installation direction is set accurately, you can try to lower the
collision sensitivity, but it is not recommended to lower it to less than
3.
Teach sensitivity:
•
The level of Teach sensitivity is from 1 to 5. The higher the set value,
the smaller the force required to drag the joint in manual mode.
1.4.1.4 Initial Position
Setting the Initial Position of the robotic arm can help the user to return
the robotic arm to a relatively safe position when planning the motion
trajectory.
Steps for setting the initial position:
1.
Click
【
Settings
】
button on the homepage.
2.
Enter
【
Motion, then click the
【
Set
】
button next to the
Initial Position.
3.
Set the initial position of the xArm in Live-control.
【
Confirm
】
: Save the changes.
【
Cancel
】
: Cancel the changes.
Содержание xArm
Страница 1: ...1...
Страница 29: ...29 Working space of xArm7 unit mm Note The following working range diagrams are only for safety assessment...
Страница 78: ...78 Step3 Open the Properties Step4 Open the IPV4...
Страница 81: ...81 1 2 4 Return to the Search Interface PC Click Tool Search to return to the search interface...
Страница 116: ...116 1 4 9 3 Advanced Tools...
Страница 119: ...119 Friction Identification...
Страница 136: ...136 7 Restart the control box enter your modified IP in the xArm Studio search box and connect the robotic arm...