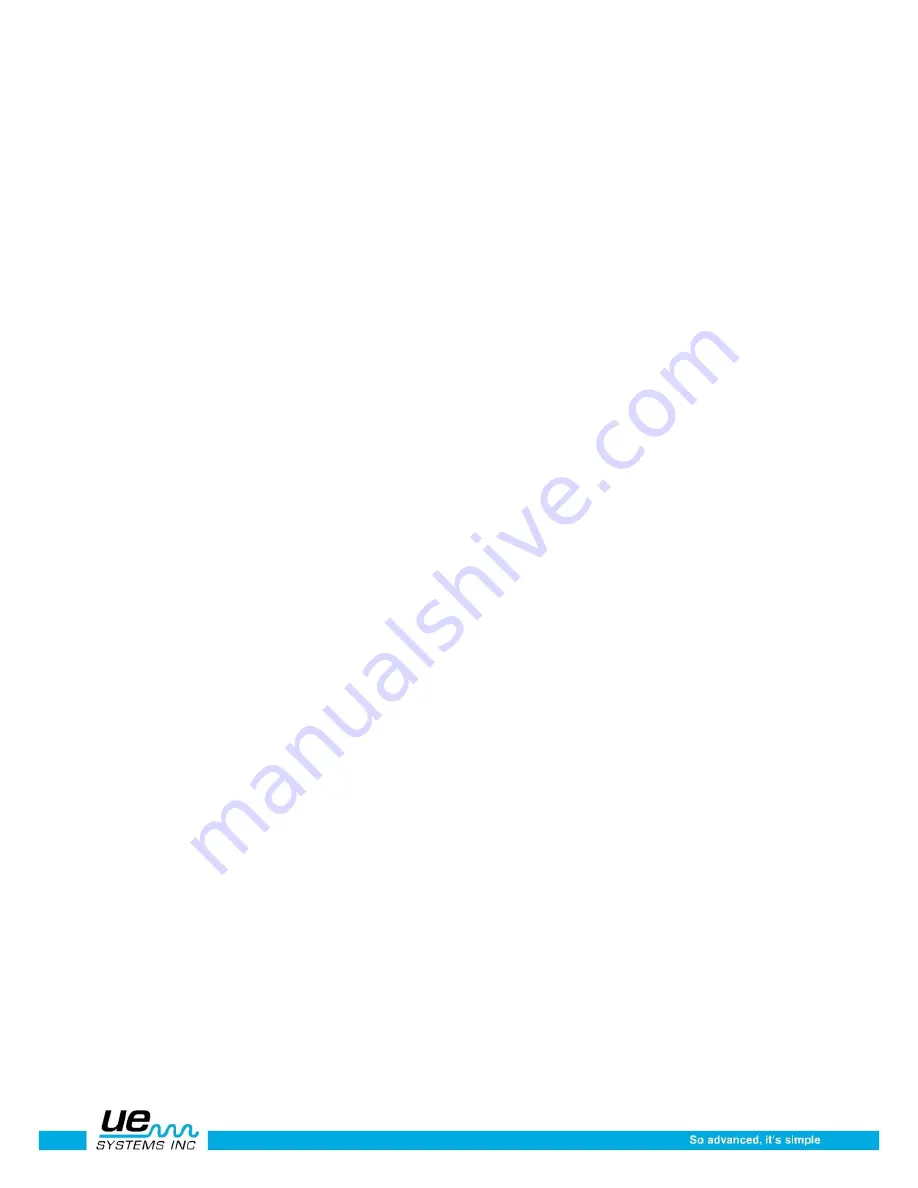
Version 1
25
For Comparative Test
1. Use contact (stethoscope) module.
2. Select a "test spot" on the bearing housing and mark it for future reference by marking it
with a center punch or with dye or by epoxy bonding a washer to the spot. Touch that spot
with the contact module. In ultrasonic sensing, the more mediums or materials ultrasound
has to travel through, the less accurate the reading will be. Therefore, be sure the contact
probe is actually touching the bearing housing. If this is difficult, touch a grease fitting or
touch as close to the bearing as possible.
3. Approach the bearings at the same angle, touching the same area on the bearing housing.
4. Reduce sensitivity) until the meter reads 20 (if unsure of this procedure, refer to
SENSITIVITY SELECTION DIAL (See page 6
5. Listen to bearing sound through headphones to hear the "quality" of the signal for proper
interpretation. (Refer to page 17 for discussion of audio interpretation.)
6. Select same type bearings under similar load conditions and same rotational speed.
7. Compare differences of meter reading and sound quality.
Procedure for Bearing History (Historical)
There are two methods to historically "trend" a bearing. The first is a very common, field proven
method called the "SIMPLE" method. The other provides greater flexibility in terms of decibel
selection and trending analysis. It is referred to as the "ATTENUATOR TRANSFER CURVE
method. Before starting with either of the two HISTORICAL methods for monitoring bearings, the
COMPARATIVE method must be used to determine a baseline.
Lack of Lubrication
To avoid lack of lubrication, note the following:
1. As the lubricant film reduces, the sound level will increase. A rise of about 8 dB over
baseline accompanied by a uniform rushing sound will indicate lack of lubrication.
2. When lubricating, add just enough to return the reading to base line.
3. Use caution. Some lubricants will need time to run to uniformly cover the bearing surfaces.
Lubricate a little at a time. DO NOT OVER-LUBRICATE
Over Lubrication
One of the most common causes of bearing failure is over lubrication. The excess stress of
lubricant often breaks bearing seals or causes a build up of heat which can create stress and
deformity.
To avoid over lubrication:
1. Don't lubricate if the base line reading and base line sound quality is maintained.
2. When lubricating, use just enough lubricant to bring the ultrasonic reading to baseline.
3. As mentioned in 3 above, use caution. Some lubricants will need time to uniformly cover the
bearing surfaces.
SLOW SPEED BEARINGS
Monitoring slow speed bearings is possible with the Ultraprobe 3000. Due to the sensitivity range, it
is quite possible to listen to the acoustic quality of bearings. In extremely slow bearings (less than
25 RPM), it is often necessary to disregard the meter and listen to the sound of the bearing. In
these extreme situations, the bearings are usually large (1"-2" and up) and greased with high
viscosity lubricant. Most often no sound will be heard as the grease will absorb most of the acoustic
energy. If a sound is heard, usually a crackling sound, there is some indication of deformity
occurring.
On most other slow speed bearings, it is possible to set a base line and monitor as described. It is
suggested that the Attenuator Transfer Curve method be used since the sensitivity will usually have
to be higher than normal.
Содержание Ultraprobe 3000
Страница 1: ...Version 1 1 Ultraprobe 3000 Instruction Manual ...
Страница 6: ...Version 1 6 Ultraprobe 3000 ...