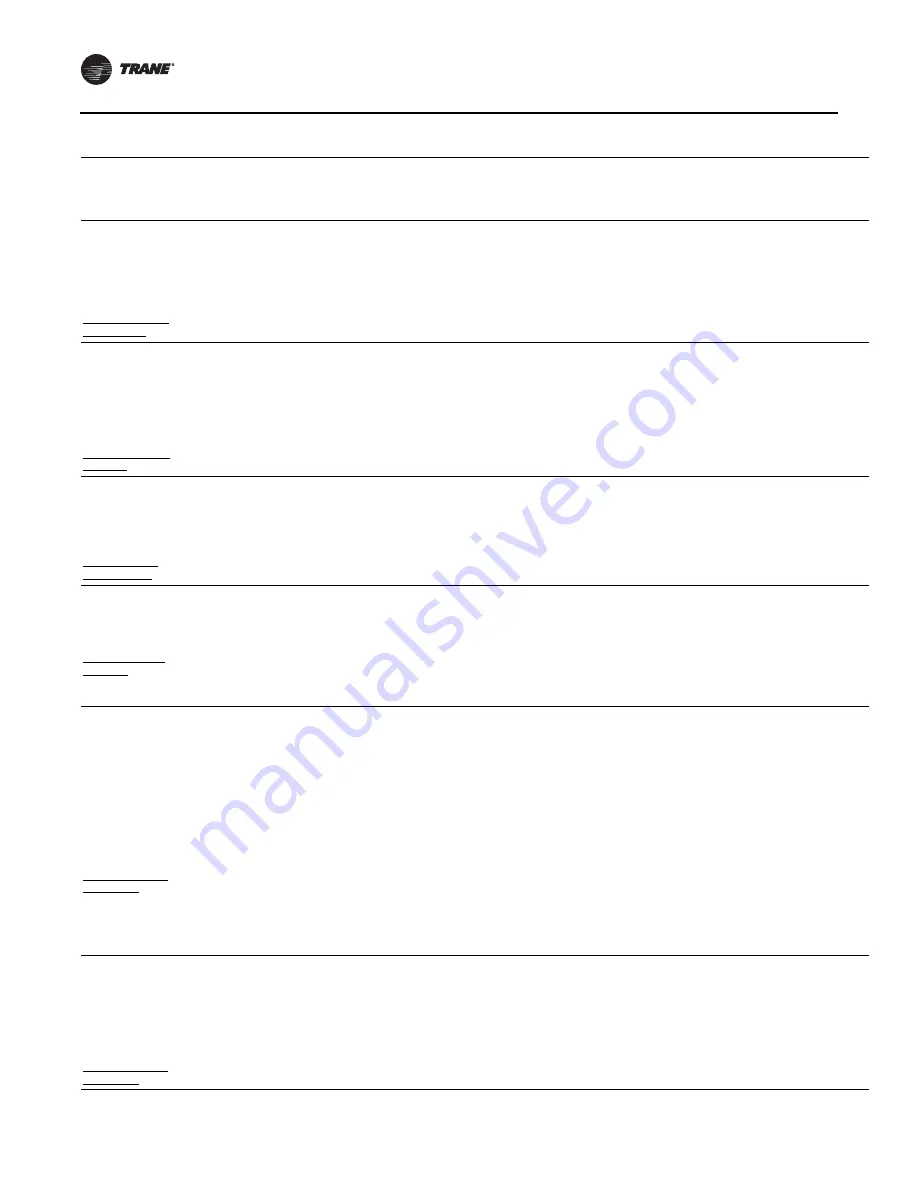
Diagnostics
74
RTAF-SVX001A-EN
Heat Recovery
Leaving Water
Temperature
Sensor
Heat Recovery
Leaving Water
Temp Sensor
Heat Rcvry Leav
Water Temp
Chiller
Info
Latch
All
Bad Sensor or LLID
Remote
High
Compressor
Refrigerant
Discharge Temp
- xy
High Cprsr Rfgt
Discharge Temp
- xy
High Cprsr Disch
Temp xy
Cprsr
Immediate Latch
All
[compressor
run unload or
compressor
not running]
The compressor discharge temperature exceeded 199.4 F (without oil
cooler) or 230ºF (with oil cooler). This diagnostic will be suppressed
during Stopping mode or after the compressor has stopped. Note: As
part of the Compressor High Temperature Limit Mode (aka Minimum
Capacity Limit), the compressor shall be forced loaded as the filtered
discharge temperature reaches 190ºF (without oil coolers), or 220ºF
(with oil coolers).
Remote
High Differential
Refrigerant
Pressure - xy
High Differential
Rfgt Pressure -
xy
High Diff Rfgt
Pressure - xy
Cprsr
Normal
Latch
Cprsr
Energized
GP2 Cprsr: The differential pressure for the respective circuit was above
275 Psid (1890 kPa) for 2 consecutive samples 5 seconds apart.
Remote
High Evaporator
Refrigerant
Pressure
High Evap Rfgt
Pressure
Chiller
Immediate NonLatch
All
The evaporator refrigerant pressure of either circuit has risen above
190 psig. The evaporator water pump relay will be de-energized to stop
the pump regardless of why the pump is running. The diagnostic will
auto reset and the pump will return to normal control when all of the
evaporator pressures fall below 185 psig. The primary purpose is to
stop the evaporator water pump and its associated pump heat from
causing refrigerant side pressures, close to the evaporator relief valve
setting, when the chiller is not running, such as could occur with Evap
Water Flow Overdue or Evaporator Water Flow Loss Diagnostics.
Remote
High Evaporator
Shell
Refrigerant
Pressure –
Circuit 1
High Evap Shell
Rfgt Pressure -
Ckt1
High Evap Shell
Press Ckt1
Chiller
Immediate NonLatch
All
The evaporator shell refrigerant pressure is installed, is valid, and has
risen above 190 psig.
- De-energize evaporator water pump regardless of why the pump is
running.
- Open the circuit’s EXV to 20% to allow refrigerant flow to other parts
of the chiller, if liquid line refrigerant pressure is less than 170 psig.
Return EXV to normal control (allow it to close until needed for circuit
operation) if liquid line refrigerant pressure is greater than 175 psig.
Automatically clear diagnostic when evaporator shell refrigerant
pressure is valid and drops below 180 psig.
- Allow evaporator water pump to return to normal control.
- Return circuit’s EXV to normal control (allow it to close until needed
for circuit operation).
Primary causes of this diagnostic:
- Evaporator water pump heat transferred to evaporator, either by flow
blockage, or by lack of heat dissipation in the water loop in the presence
of flow.
- Commissioning unit in high ambient temperature environments.
- Water box heater thermostat failed closed.
Remote
High Evaporator
Shell
Refrigerant
Pressure –
Circuit 2
High Evap Shell
Rfgt Pressure -
Ckt2
High Evap Shell
Press Ckt2
Chiller
Immediate NonLatch
All
See Circuit 1 description.
Remote
Table 27.
Main processor diagnostics (continued)
Diagnostic
Name
Affects
Target Severity Persistence
Active
Modes
[Inactive
Modes]
Criteria
Reset
Level