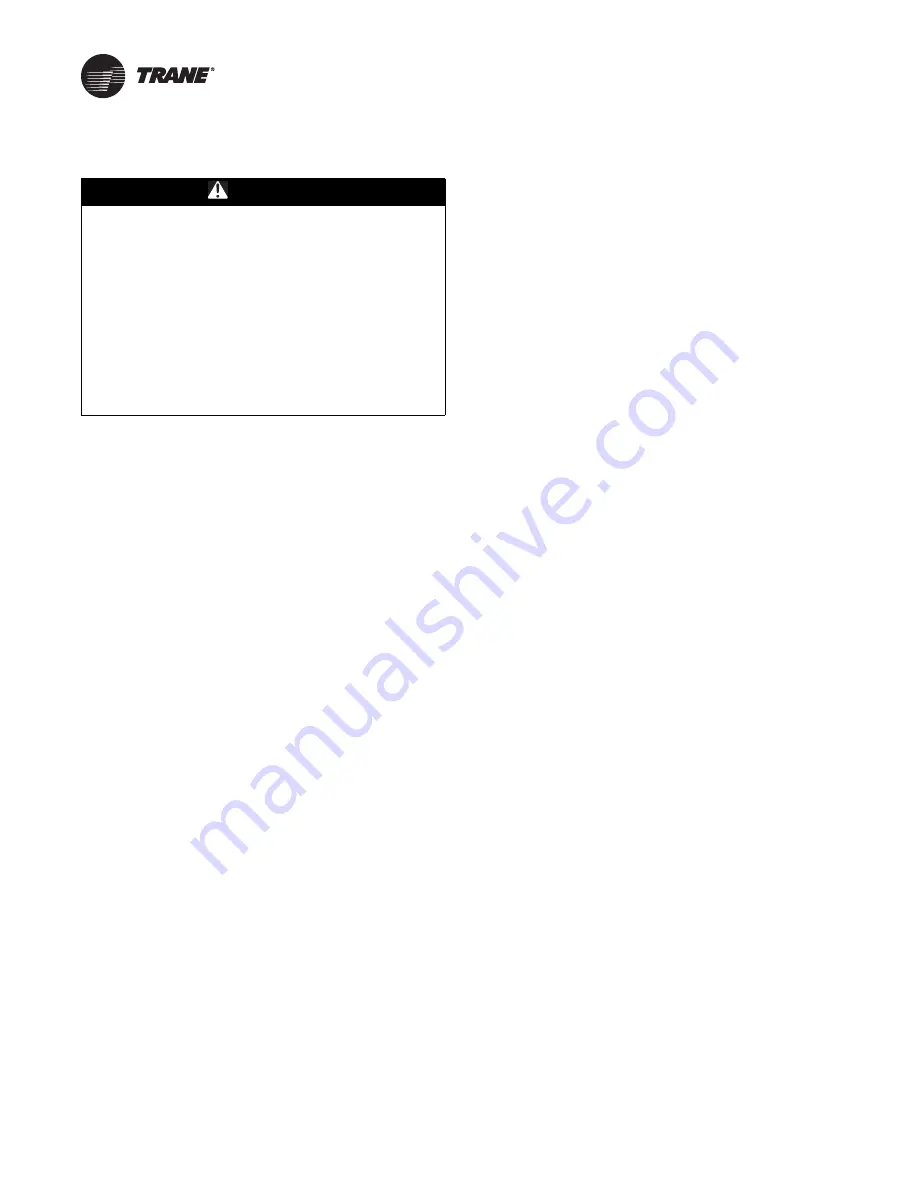
68
RTHD-SVX01K-EN
Maintenance
This section describes the basic chiller preventive
maintenance procedures, and recommends the intervals
at which these procedures should be performed. Use of a
periodic maintenance program is important to ensure the
best possible performance and efficiency from a Stealth™
chiller.
Use an Operator Log (see
)
to record an operating history for unit. The log serves as a
valuable diagnostic tool for service personnel. By
observing trends in operating conditions, an operator can
anticipate and prevent problem situations before they
occur.
If unit does not operate properly during inspections, see
.
Recommended Maintenance
Weekly
While the unit is running in stable conditions:
•
Log the chiller.
•
Check evaporator and condenser pressures with
gauges and compare to the reading on the Tracer
AdaptiView™ TD7 or Tracer
®
TU service tool. Pressure
readings should fall within operating ranges specified
in
. If chiller measurements
vary significantly from values listed in
and
, problems may exist with refrigerant
and oil charge levels. Contact local Trane service.
Note:
Optimum condenser pressure is dependent on
condenser water temperature, and should
equal saturation pressure of refrigerant at a
temperature 2 to 5
F above that of leaving
condenser water at full load.
Monthly
•
Review operating log.
•
Clean all water strainers in both the chilled and
condensing water piping systems.
•
Measure and log the subcooling and superheat.
•
“Refrigerant and Oil Charge Management,” p. 68
.
If chiller measurements vary significantly from values
listed in
and
, problems may
exist with refrigerant and oil charge levels. Contact
local Trane service.
Annual
Shut down the chiller once each year to check the
following:
•
Perform all weekly and monthly maintenance
procedures.
•
Have a qualified laboratory perform an oil analysis to
determine system moisture content and acid level
.
Important:
Due to the hygroscopic properties of the
POE oil, all oil must be stored in metal
containers. The oil will absorb water if
stored in a plastic container.
•
Contact Trane service to leak check the chiller, inspect
safety controls, and inspect electrical components for
deficiencies.
•
Inspect all piping components for leakage and/or
damage. Clean out any in-line strainers.
•
Clean and repaint any areas that show signs of
corrosion.
•
Inspect vent piping of all relief valves for presence of
refrigerant to detect improperly sealed relief valves.
Contact Trane service if unusual conditions are
observed.
•
Inspect the condenser tubes for fouling. Clean if
necessary. See
“Cleaning the Condenser,” p. 69
.
•
Check to make sure that the oil sump heater is working.
Scheduling Other Maintenance
•
Use a nondestructive tube test to inspect the
condenser and evaporator tubes at 3-year intervals.
Note:
It may be desirable to perform tube tests on these
components at more frequent intervals, depending
upon chiller application. This is especially true of
critical process equipment.
•
Depending on chiller duty, contact Trane service
organization to determine when to conduct a complete
examination of the unit to determine the condition of
the compressor and internal components.
Refrigerant and Oil Charge Management
Proper oil and refrigerant charge is essential for proper
unit operation, unit performance, and environmental
protection. Only trained and licensed service personnel
should service the chiller.
list baseline measurements for
Optimus™ units running at AHRI standard operating
WARNING
Hazardous Voltage w/Capacitors!
Failure to disconnect power and discharge capacitors
before servicing could result in death or serious injury.
Disconnect all electric power, including remote
disconnects and discharge all motor start/run
capacitors before servicing. Follow proper lockout/
tagout procedures to ensure the power cannot be
inadvertently energized. For variable frequency drives
or other energy storing components provided by Trane
or others, refer to the appropriate manufacturer’s
literature for allowable waiting periods for discharge of
capacitors. Verify with a CAT III or IV voltmeter rated
per NFPA 70E that all capacitors have discharged.
Содержание Optimus RTHD
Страница 27: ...Installation Mechanical RTHD SVX01K EN 27...
Страница 28: ...Installation Mechanical 28 RTHD SVX01K EN...
Страница 29: ...Installation Mechanical RTHD SVX01K EN 29...
Страница 54: ...Controls 54 RTHD SVX01K EN Figure 23 Tracer TU...
Страница 88: ...Log and Check Sheets 88 RTHD SVX01K EN Page Left Intentionally Blank...
Страница 95: ...Notes RTAF SVX001K EN 95...