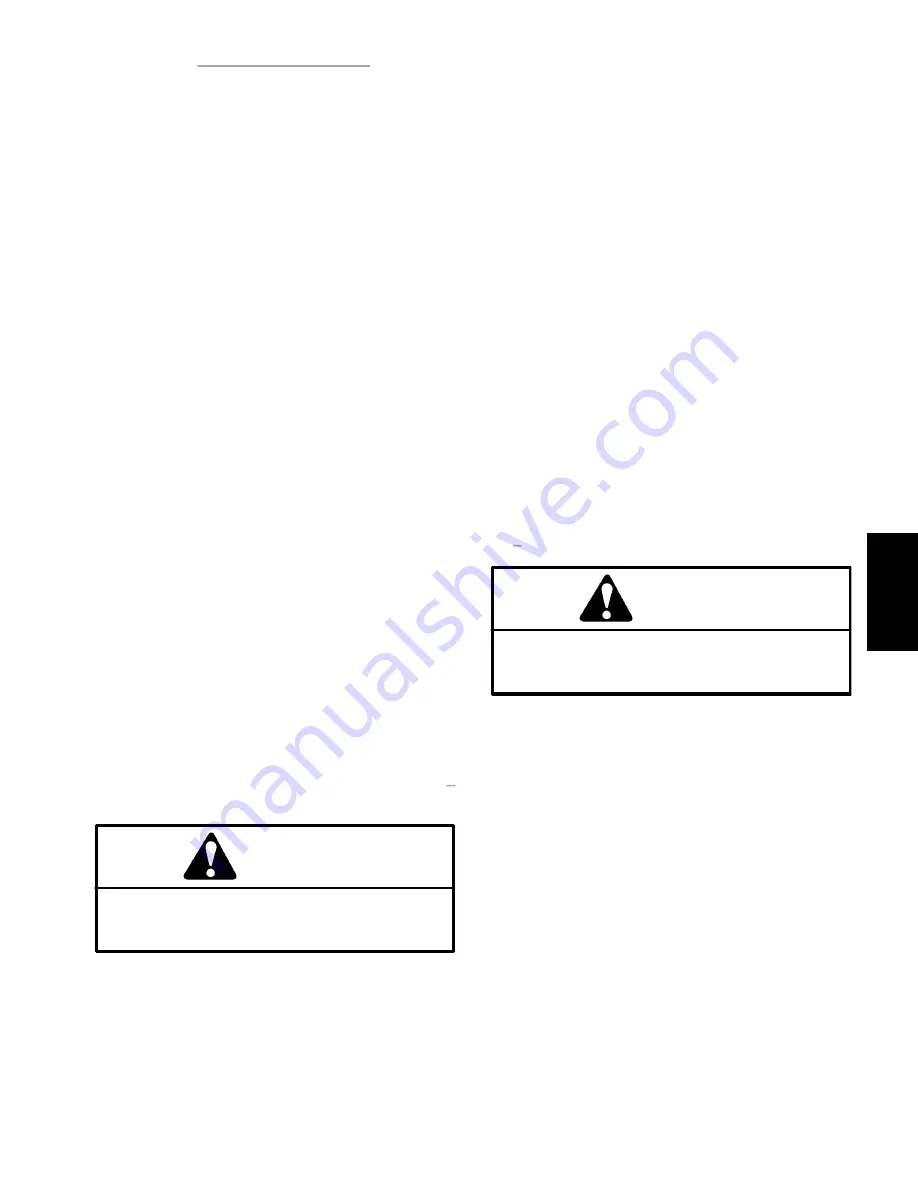
Procedure for Wheel Motor Case Drain Test:
1. Make sure hydraulic oil is at normal operating tem-
perature by operating the machine for approximately 10
minutes. Make sure the hydraulic tank is full.
2. Park machine on a level surface with the cutting units
lowered and off. Make sure engine is off and the parking
brake is engaged.
3. Read Precautions For Hydraulic Testing.
4. Make sure that traction pedal is adjusted to the neu-
tral position (see Traction Unit Operator’s Manual).
5. Attach a heavy chain between the rear of the ma-
chine frame and an immovable object to prevent the ma-
chine from moving during testing.
6. Chock front wheel being tested to prevent rotation of
the wheel. Make sure parking brake is on.
7. Disconnect hydraulic lines from front wheel motor
that is
not
being tested. Cap disconnected hydraulic
lines and plug ports in wheel motor to prevent contami-
nation.
8. Clean hose fitting and disconnect hose from the el-
bow connection on the top of the traction pump (Fig. 20).
IMPORTANT: Make sure oil flow indicator arrow on
the flow gauge is showing that the oil will flow from
the motor through the tester and into the hose.
9. Install flow tester with pressure gauges in series with
the pump and the disconnected hose. Make sure flow
control valve is fully open.
10.If machine has 3WD kit installed, make certain that
reel engage switch is pushed in (disengaged) to prevent
hydraulic flow to the rear wheel.
11. Start engine and move throttle to full speed
(3200 +
50 RPM)
.
CAUTION
Use extreme caution when performing test. The
machine forward.
front tire on the ground will be trying to move the
12.Slowly push traction pedal in
forward
direction until
1000 PSI is displayed on the pressure gauge.
13.Wheel motor internal leakage will be shown on flow
meter in GPM. Flow should be
less than 1.5 GPM
for
the tested wheel motor.
14.If specifications are not met, the tested wheel motor
needs to be repaired or replaced as necessary.
15.If remaining front wheel motor requires testing, com-
plete steps 6 to 13 for the remaining motor.
16.If machine has 3WD kit installed and rear wheel mo-
tor requires testing:
A. Both front wheel motors should have hydraulic
lines disconnected. Cap disconnected hoses and
plug ports in wheel motor to prevent contamination.
B. Attach a heavy chain between the rear of the ma-
chine frame and an immovable object to prevent the
machine from moving during testing.
C. Chock rear wheel to prevent it from turning.
D. Clean hose fitting and disconnect hose from the
elbow connection on the top of the traction pump
(Fig. 20).
E. Install tester in series with the pump and the dis-
connected hose. Make sure flow control valve is fully
open.
F. Start engine and move throttle to full speed
(3200
+ 50 RPM)
.
CAUTION
Use extreme caution when performing test. The
machine forward.
rear tire on the ground will be trying to move the
G. Slowly push traction pedal in
forward
direction
until 1000 PSI is displayed on the pressure gauge.
H. Wheel motor internal leakage will be shown on
flow meter in GPM. Flow should be
less than 1.5
GPM
for the tested wheel motor.
I. If specifications are not met, the wheel motor
needs to be repaired or replaced.
17.Disconnect tester from hydraulic fitting and hose.
Reconnect hose to pump connection.
18.Reconnect hydraulic lines to wheel motors.
Hydraulic System
Reelmaster 2000–D
Page 4 – 39
Hydraulic System
Содержание Reelmaster 2000-D
Страница 2: ...This page is intentionally blank Reelmaster 2000 D ...
Страница 4: ...This page is intentionally blank Reelmaster 2000 D ...
Страница 10: ...Rev A 0 09375 Reelmaster 2000 D Page 2 2 Product Records and Maintenance Equivalents and Conversions ...
Страница 25: ...Engine This page is intentionally blank Reelmaster 2000 D Page 3 9 Engine ...
Страница 36: ...This page is intentionally blank Engine Page 3 20 Reelmaster 2000 D ...
Страница 39: ...This page is intentionally blank Hydraulic System Reelmaster 2000 D Page 4 3 Hydraulic System ...
Страница 99: ...57 4 Rev A Reelmaster 2000 D Hydraulic System Page 4 This page is intentionally blank Hydraulic System ...
Страница 101: ...This page is intentionally blank Hydraulic System Reelmaster 2000 D Page 4 59 Hydraulic System ...
Страница 105: ...This page is intentionally blank Hydraulic System Reelmaster 2000 D Page 4 63 Hydraulic System ...
Страница 109: ...63 4 Rev A Reelmaster 2000 D Hydraulic System Page 4 This page is intentionally blank Hydraulic System ...
Страница 156: ...This page is intentionally blank Electrical System Page 5 30 Reelmaster 2000 D ...
Страница 159: ...This page is intentionally blank Reelmaster 2000 D Page 6 3 Chassis Chassis ...
Страница 172: ...This page is intentionally blank Chassis Page 6 16 Reelmaster 2000 D ...
Страница 175: ...This page is intentionally blank Reelmaster 2000 D Page 7 3 Cutting Units Cutting Units ...
Страница 194: ...This page is intentionally blank Electrical Diagrams Page 8 2 Reelmaster 2000 D ...
Страница 201: ...Rev A Page 8 9 This page is intentionally blank ...
Страница 203: ...Rev A Page 8 11 Reelmaster 2000 D Main Wire Harness Serial Number Below 230000000 ...
Страница 205: ...Rev A Page 8 13 Reelmaster 2000 D Main Wire Harness Serial Number Above 230000000 ...
Страница 207: ...Rev A Page 8 15 Reelmaster 2000 D Engine Wire Harness ...
Страница 208: ...Rev A Page 8 16 This page is intentionally blank ...