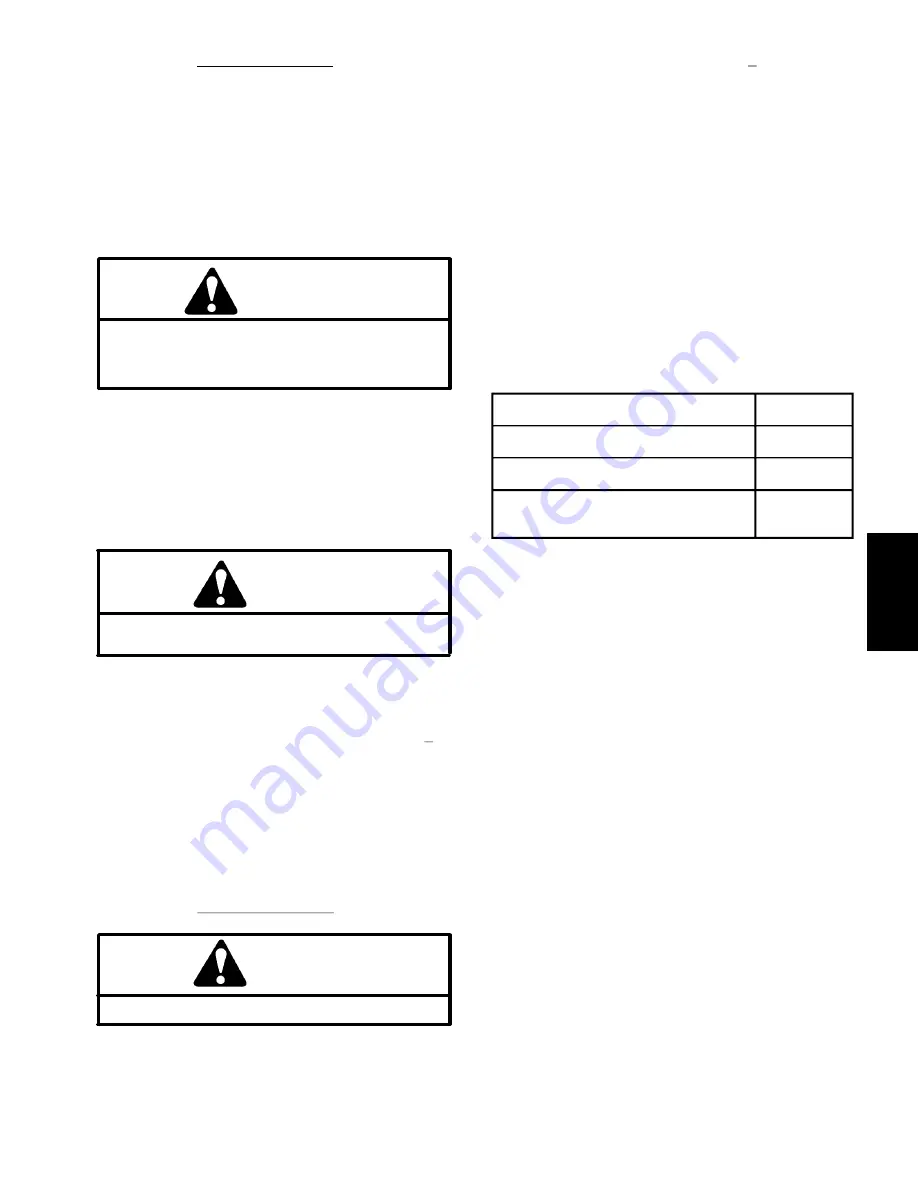
Procedure for Charge Pump Flow Test:
1. Make sure hydraulic oil is at normal operating tem-
perature by operating the machine for approximately 10
minutes.
2. Park machine on a level surface with the cutting units
lowered. Make sure engine is off and the parking brake
is engaged.
3. Read Precautions For Hydraulic Testing.
CAUTION
draulic oil.
Operate all hydraulic controls to relieve system
pressure and avoid injury from pressurized hy-
4. Disconnect outside top hose from the discharge fit-
ting of the charge pump (Fig. 21). Connect gauge end
of flow tester with pressure gauges to the pump dis-
charge fitting.
5. Connect the other end of the tester to the discon-
nected hose.
CAUTION
after tester installation.
Make sure that all hoses are free of the flywheel
6. Make sure that traction pedal and lift valve are in neu-
tral and the parking brake is engaged.
7. Start and operate engine at full speed
(3200 + 50
RPM)
.
8. Watch flow and pressure gauges carefully while
slowly closing the flow control valve until pressure
gauge reads
500 PSI
.
9.
Minimum
flow gauge reading should be
2.5 GPM
. If
specification is not met, repair or replace charge pump.
Procedure for Lift Relief Pressure Check:
CAUTION
Do not allow charge pressure to exceed 650 PSI.
1. Fully open control valve on the tester.
2. Make sure hydraulic oil is at operating temperature.
3. Operate engine at full speed
(3200 + 50 RPM)
.
4. Watch pressure gauge carefully. Make sure lift lever
is in the neutral position. Record the pressure.
5. While holding the lift lever in the raised position,
watch the pressure gauge. Record pressure when the
relief valve opens.
6. Return lift lever to neutral position. Shut off engine.
7. Subtract the relief valve closed pressure from the re-
lief valve open pressure (see example below). The dif-
ference should be from
450 to 500 PSI
.
A. If this specification is not met, adjust lift relief
valve.
B. If this specification is met, go to step 9.
NOTE:
Do not remove lift relief valve from the hydraulic
manifold for adjustment.
8. Adjust the lift relief valve pressure as follows:
A. Remove the cap from the relief valve.
B. To increase the relief valve pressure setting, use
an allen wrench and turn adjustment socket clock-
wise. A 1/8 turn on the socket will make a measur-
able change in relief pressure.
C. To decrease the relief valve pressure setting, use
an allen wrench and turn adjustment socket counter-
clockwise. A 1/8 turn on the socket will make a mea-
surable change in relief pressure.
D. Repeat steps 1 through 8 above until the relief
valve pressure setting is correct. Reinstall cap on re-
lief valve when valve is set properly.
E. If the relief valve pressure setting can not be ad-
justed to specification, go to step 9 and replace the
relief valve.
NOTE:
If the pressure and flow are within specification
but the cutting units do not lift or lift slowly, check for me-
chanical binding or internal leakage of the lift cylinder.
9. Disconnect tester from the pump and hose. Recon-
nect hose to the pump.
Example Calculation
PRESSURE
Relief Valve Open (Lever raised)
620
Relief Valve Closed (Lever in neutral)
150
Open less Closed Pressure
470
(450 to 500 PSI)
Hydraulic System
Reelmaster 2000–D
Page 4 – 27
Hydraulic System
Содержание Reelmaster 2000-D
Страница 2: ...This page is intentionally blank Reelmaster 2000 D ...
Страница 4: ...This page is intentionally blank Reelmaster 2000 D ...
Страница 10: ...Rev A 0 09375 Reelmaster 2000 D Page 2 2 Product Records and Maintenance Equivalents and Conversions ...
Страница 25: ...Engine This page is intentionally blank Reelmaster 2000 D Page 3 9 Engine ...
Страница 36: ...This page is intentionally blank Engine Page 3 20 Reelmaster 2000 D ...
Страница 39: ...This page is intentionally blank Hydraulic System Reelmaster 2000 D Page 4 3 Hydraulic System ...
Страница 99: ...57 4 Rev A Reelmaster 2000 D Hydraulic System Page 4 This page is intentionally blank Hydraulic System ...
Страница 101: ...This page is intentionally blank Hydraulic System Reelmaster 2000 D Page 4 59 Hydraulic System ...
Страница 105: ...This page is intentionally blank Hydraulic System Reelmaster 2000 D Page 4 63 Hydraulic System ...
Страница 109: ...63 4 Rev A Reelmaster 2000 D Hydraulic System Page 4 This page is intentionally blank Hydraulic System ...
Страница 156: ...This page is intentionally blank Electrical System Page 5 30 Reelmaster 2000 D ...
Страница 159: ...This page is intentionally blank Reelmaster 2000 D Page 6 3 Chassis Chassis ...
Страница 172: ...This page is intentionally blank Chassis Page 6 16 Reelmaster 2000 D ...
Страница 175: ...This page is intentionally blank Reelmaster 2000 D Page 7 3 Cutting Units Cutting Units ...
Страница 194: ...This page is intentionally blank Electrical Diagrams Page 8 2 Reelmaster 2000 D ...
Страница 201: ...Rev A Page 8 9 This page is intentionally blank ...
Страница 203: ...Rev A Page 8 11 Reelmaster 2000 D Main Wire Harness Serial Number Below 230000000 ...
Страница 205: ...Rev A Page 8 13 Reelmaster 2000 D Main Wire Harness Serial Number Above 230000000 ...
Страница 207: ...Rev A Page 8 15 Reelmaster 2000 D Engine Wire Harness ...
Страница 208: ...Rev A Page 8 16 This page is intentionally blank ...