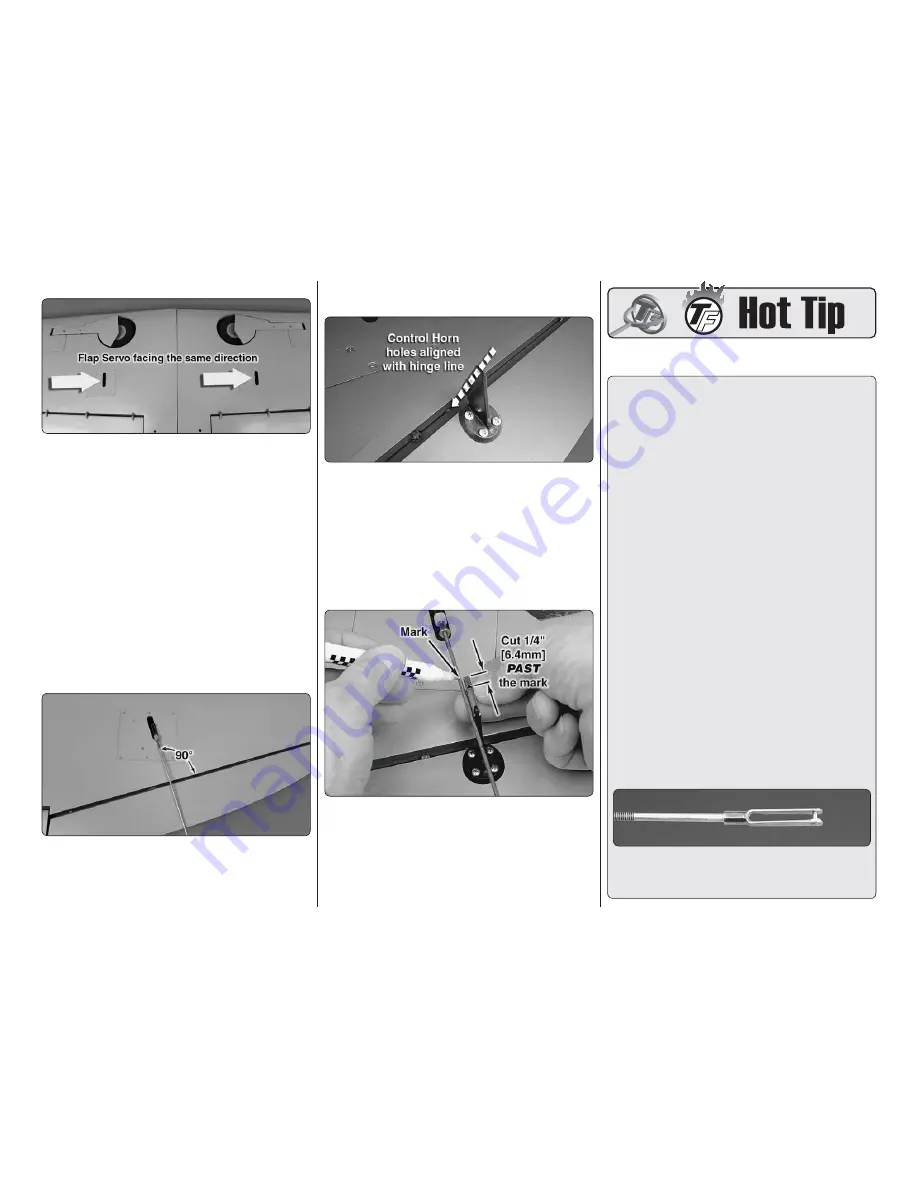
11
INSTALL THE FLAP SERVOS
❏ ❏
1. Install the fl ap servos following the same
procedure used to install the aileron servos. Note that
the fl ap servos face the same direction.
❏ ❏
2. Connect a 12" [305mm] servo extension wire
to the fl ap servo. Secure the extension to the servo
with a piece of heat shrink or electrical tape.
❏ ❏
3. Route the fl ap servo leads to the root of the
wing and out the hole in the top of the wing.
INSTALL THE AILERON AND
FLAP PUSHRODS
Do the left aileron fi rst. Temporarily plug the aileron
servo into the receiver. Switch on your transmitter
and plug a receiver battery into the receiver. Center
the aileron trim.
❏ ❏
1. Slide a silicone clevis retainer over a 4-40
threaded metal clevis. Thread a 4-40 nut followed by
the 4-40 metal clevis, threaded 12 turns onto a 4-40
x 12" [305mm] metal pushrod. Attach the clevis to
the
aileron
servo arm 5/8" [15.9mm] from the center
of the arm.
❏ ❏
2. Position the control horn so that it is inline with
the pushrod and over the plywood mounting plate. The
pushrod holes in the control horn should be aligned
with the hinge line of the aileron. On the aileron, mark
the four mounting holes. Remove the control horn and
drill a 5/64" [2mm] pilot hole at each mark. Do not drill
completely through the aileron. Attach the control horn
using four #4 x 1/2" [12.7mm] sheet metal screws. Use
thin CA to harden the holes.
❏ ❏
3. Install the metal solder clevis in the second
hole from the end of the control horn. Center the
aileron servo and aileron. Mark the pushrod where it
meets the solder clevis. Remove the pushrod and the
solder clevis and cut the pushrod 1/4" [6.4mm]
past
the mark. Solder the solder clevis to the pushrod using
the techniques described in the following
Hot Tip
.
HOW TO SOLDER
1. Use denatured alcohol or other solvent to
thoroughly clean the pushrod. Roughen the end of
the pushrod with coarse sandpaper where it is to
be soldered.
2. Apply a few drops of soldering fl ux to the end of
the pushrod, then use a soldering iron or a torch
to heat it. “Tin” the heated area with silver solder
by applying the solder to the end. The heat of the
pushrod should melt the solder – not the fl ame
of the torch or soldering iron – thus allowing the
solder to fl ow. The end of the wire should be coated
with solder all the way around.
3. Place the clevis on the end of the pushrod. Add
another drop of fl ux, then heat and add solder.
The same as before, the heat of the parts being
soldered should melt the solder, thus allowing
it to fl ow. Allow the joint to cool naturally without
disturbing. Avoid excess blobs, but make certain
the joint is thoroughly soldered. The solder should
be shiny, not rough. If necessary, reheat the joint
and allow to cool.
4. Immediately after the solder has solidifi ed, but
while it is still hot, use a cloth to quickly wipe off
the fl ux before it hardens.
Important:
After the joint
cools, coat the joint with oil to prevent rust.
Note:
Do not use the acid fl ux that comes with silver
solder for electrical soldering.
This is what a properly soldered clevis looks
like – shiny solder with good flow, no blobs and
flux removed.