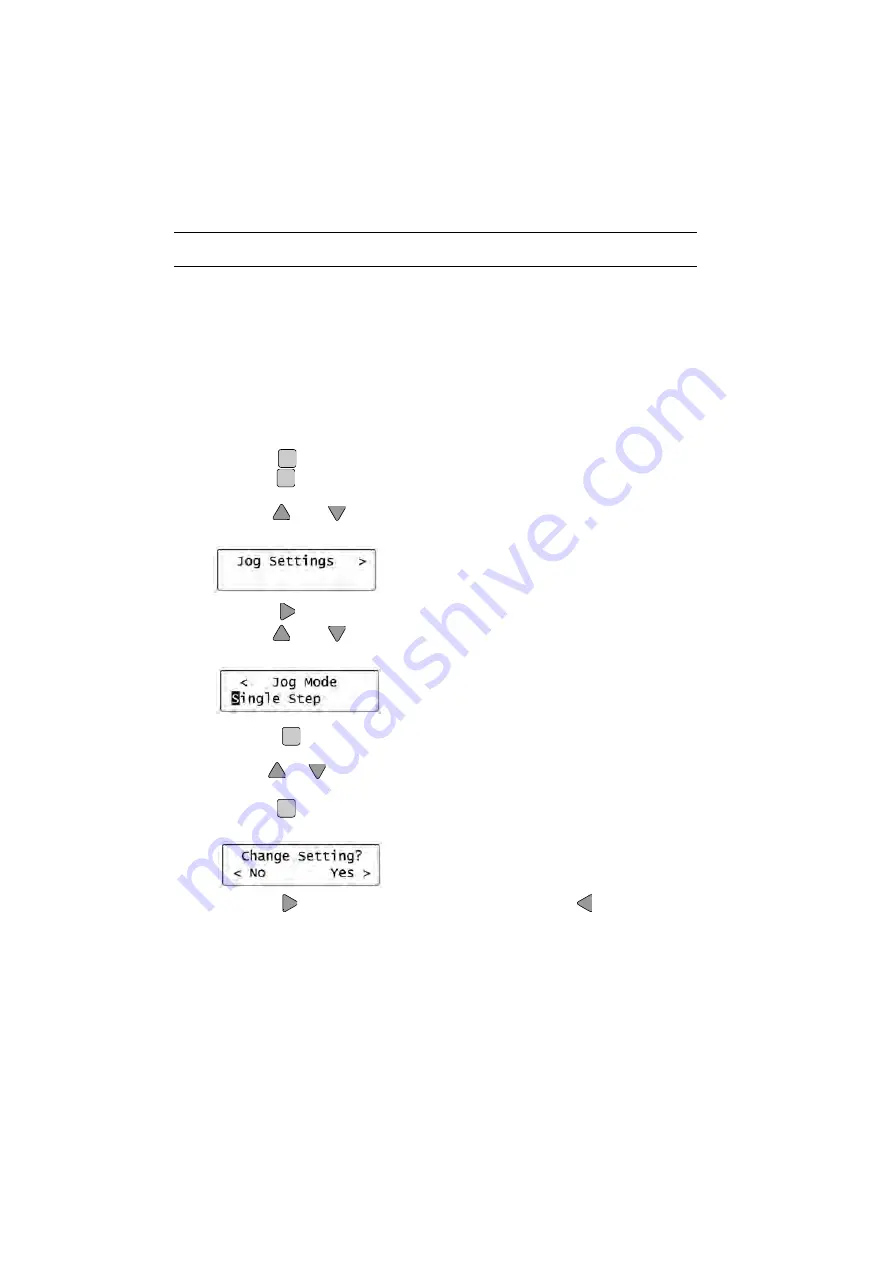
24
Chapter 3
Benchtop (Local Mode) Tutorial
3.7
Jogging
In ‘Local’ mode, the motor actuators can be jogged using the front panel arrow keys,
or by using an optional jog handset connected to the MOTOR CONTROL port on the
rear panel of the unit (see Section 2.5. for details on the jog handset). There are two
jogging modes available, ‘Single Step’ and ‘Continuous’. In ‘Single Step’ mode, the
motor moves by the step size specified in the Step Distance parameter. If the jog key
is held down, single step jogging is repeated until the button is released - see Fig. 3.6.
In ‘Continuous’ mode, the motor actuator will accelerate and move at the jog velocity
while the button is held down.
1) Press the
key until the channel 1 led is lit.
2) Press the
key to enter the Setup menu. The display then shows the parameter
most recently selected.
3) Use the
and
keys to scroll through the parameter list and select the
Jog Settings >
parameter.
4) Press the
key to enter Jog Settings menu.
5) Use the
and
keys to scroll through the parameter list and select the
<
Jog Mode
parameter.
6) Press the
key to enter the Edit mode. The first letter of the current value
flashes.
7) Use the
or
keys to adjust the displayed value to Single Step (The default
factory setting).
8) Press the
key to save the setting. The unit asks whether you want to save the
change by displaying ‘
Change Setting?
< No Yes >
’.
Press the
key to save the change (you would use the
key to leave the
value unchanged).
Chan
Menu
Save
Menu
Save
Menu
Save