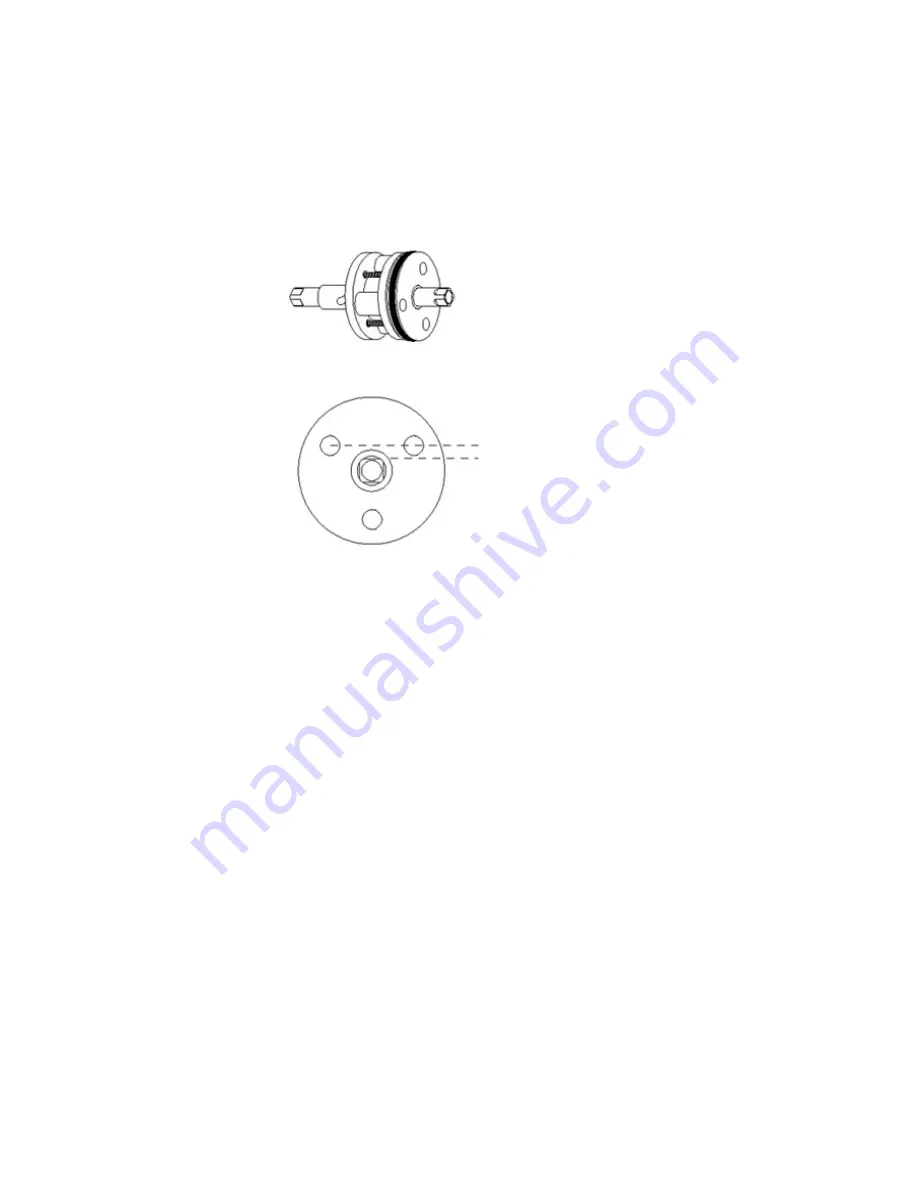
Appendix B
Rotary Valve Service
Assembly
Where possible, apply a slight rotating action to the parts as they go over or
through the O-Rings to help prevent any nicking or tearing of the new parts.
1. Being careful that the subassembly does not come apart, gently push the
O-Ring plate onto the drive shaft. Make sure that the threaded holes in
the plate are facing the subassembly.
Figure B–10.
Figure B–11.
2. Screw the slotted-head screws into the O-Ring plate, and push the drive
shaft into the O-Ring plate as far as it will go, as shown in Figure B–10.
3. Place the washers and bearing in the male end cap (thin washers in first,
as shown Figure B–9). One of the flats on the drive shaft lines up with a
line drawn between two of the holes in the O-Ring plate (Figure B–11).
4. Slide the subassembly onto the pins of the male end cap with this flat
lined up with the air inlet on the end cap.
5. Install the cylinder, sliding it over the subassembly and pressing the
male end cap into it.
6. Place the washers and bearing in the female end cap. Press the end cap
into the cylinder, making sure that the air inlet hole is in the same
orientation as the one in the male end cap.
7. Install the three end cap screws with the PEEK washers provided.
8. Replace the valve mounting hardware and air supply lines.
Thermo Scientific
SOLA II Flare User
Manual
B-10
Содержание SOLA II Flare
Страница 1: ...SOLA II Flare Sulfur Online Analyzer User Manual PN 90 1312 0...
Страница 2: ......
Страница 3: ...SOLA II Flare Sulfur Online Analyzer User Manual PN 90 1312 0 Revision A...
Страница 4: ......
Страница 6: ......
Страница 8: ......
Страница 14: ......
Страница 18: ......
Страница 42: ...Chapter 3 Start Up Shutdown Thermo Scientific SOLA II Flare User Manual 3 6 Figure 3 4 Diagnostics Menu...
Страница 44: ......
Страница 48: ......
Страница 70: ......
Страница 72: ......
Страница 80: ......
Страница 104: ......
Страница 122: ......
Страница 136: ......
Страница 148: ......
Страница 158: ......
Страница 160: ......
Страница 162: ......