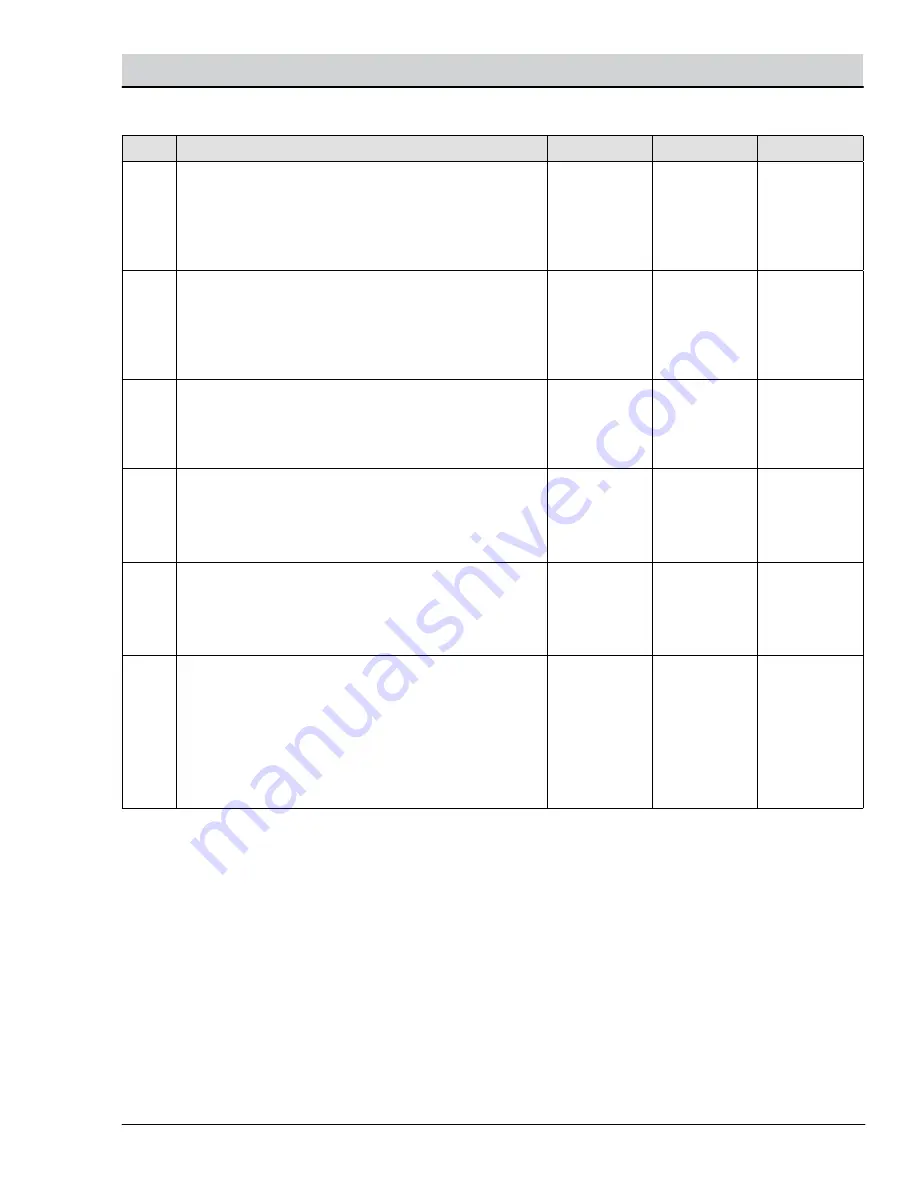
M17 Service Information 90
17358
(
08
-
20
16)
4-
7
5
TROUBLESHOOTING
STEP
ACTION
VALUE(S)
YES
NO
1
•
Key On
•
Enable hopper
roll
switch
•
Is there a
pertinent
fault message
displayed?
See
“
Fault Section"
Go to Step #2
2
•
Key Off
•
See “Manual Mode” section of this manual
•
Activate the hopper roll actuator switch in manual
mode
•
Does the hopper roll IN?
Go to Step #
6
Go to Step #3
3
•
Key Off
•
See “Self-Test Mode”
•
Does the Self-Test display output circuits J4-9, 18
as open or shorted?
Correct Open
or Short Cir-
cuit Condition
Go to Step #4
4
•
Key O
ff
•
See “Input Display Mode”
•
Does I6: Roll Switch in/out
correspond with
rocker switch position?
Go to Step #5
Correct Faulty
Input Condi-
tion
5
•
Key O
ff
•
See TESTING HOPPER ROLL ACTUATOR in the SER-
VICE section of this manual
•
Does the roll actuator pass the testing?
See TESTING
HOPPER ROLL
ACTUATOR
Go to Step #6
Replace Side
Brush Motor
6
•
Key O
ff
•
Reconnect hopper roll actuator to main wire harness
•
Test voltage applied to hopper roll actuator system as
shown on the electrical schematic
•
Are the electrical circuits operating as shown on the
electrical schematic?
Go Back to
Step #1
Identify Volt-
age Drop
Location and
Repair or Re-
place Neces-
sary Compo-
nents
Terms:
J4-9,18 = Main Sweep/Lift Module
Hopper
Roll Actuator,
Retract
/
In
, Off
Содержание M17 Series
Страница 10: ...1 6 M17 Service Information 9017358 08 2016 SAFETY PRECAUTIONS ...
Страница 124: ...4 28 TROUBLESHOOTING M17 Service Information 9017358 08 2016 ...
Страница 182: ...4 86 M17 Service Information 9017358 08 2016 TROUBLESHOOTING ...
Страница 202: ...5 20 SERVICE M17 Service Information 9017358 08 2016 PAGE INTENTIONAL LEFT BLANK ...
Страница 203: ...5 21 SERVICE M17 Service Information 9017358 08 2016 PAGE INTENTIONAL LEFT BLANK ...
Страница 204: ...5 22 SERVICE M17 Service Information 9017358 08 2016 PAGE INTENTIONAL LEFT BLANK ...