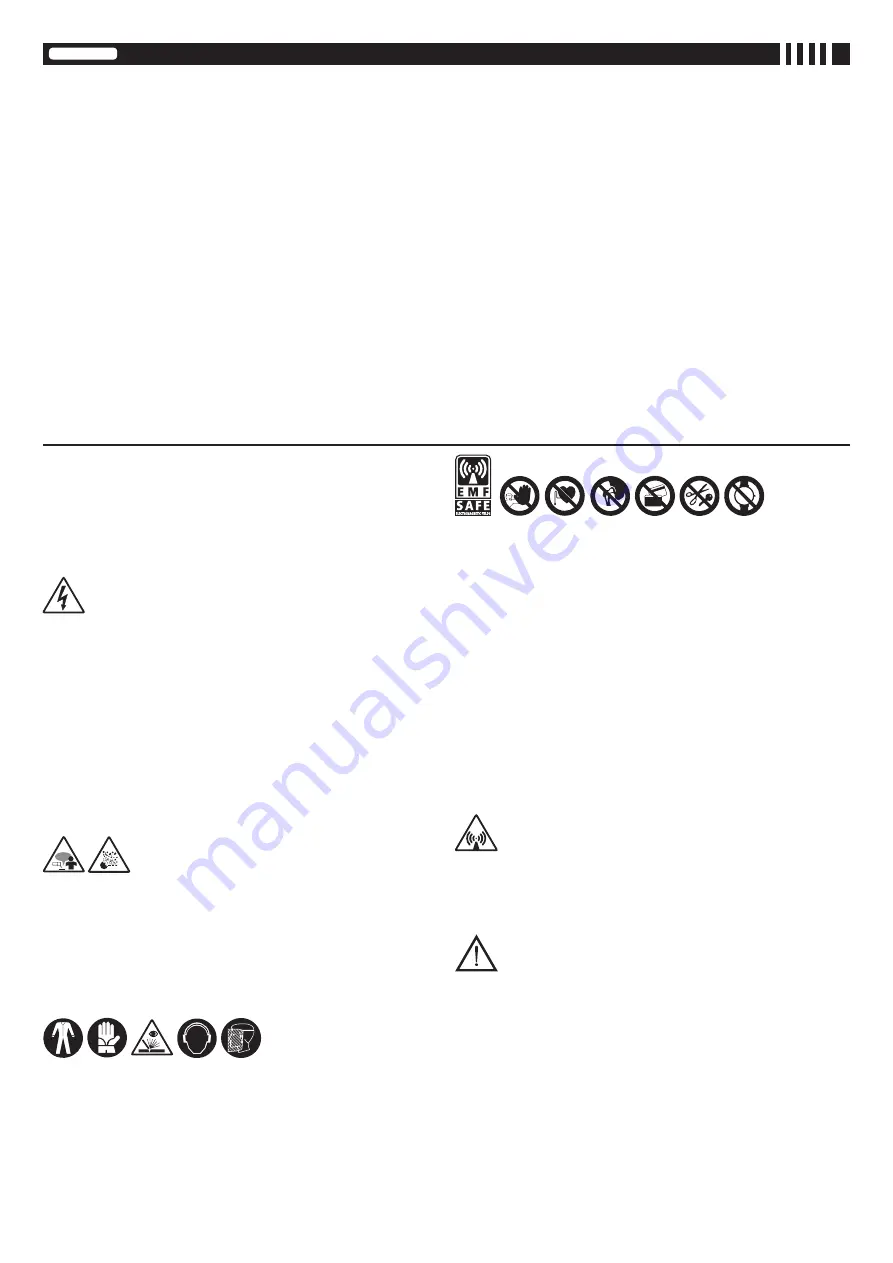
- 5 -
- The flow of the welding current generates electromagnetic fields (EMF)
around the welding circuit.
Electromagnetic fields can interfere with certain medical equipment (e.g. Pace-
makers, respiratory equipment, metallic prostheses etc.).
Adequate protective measures must be adopted for persons with these types of
medical apparatus. For example, they must be forbidden access to the area in
which welding machines are in operation.
This welding machine conforms to technical product standards for exclusive
use in an industrial environment for professional purposes. It does not assure
compliance with the basic limits relative to human exposure to electromagnetic
fields in the domestic environment.
The operator must adopt the following procedures in order to reduce exposure
to electromagnetic fields:
- Fasten the two welding cables as close together as possible.
- Keep head and trunk as far away as possible from the welding circuit.
- Never wind welding cables around the body.
- Avoid welding with the body within the welding circuit. Keep both cables on
the same side of the body.
- Connect the welding current return cable to the piece being welded, as close
as possible to the welding joint.
- Do not weld while close to, sitting on or leaning against the welding machine
(keep at least 50 cm away from it).
- Do not leave objects in ferromagnetic material in proximity of the welding
circuit.
- Minimum distance d: 20 cm (Fig. N).
- Class A equipment:
This welding machine conforms to technical product standards for exclusive
use in an industrial environment and for professional purposes. It does not
assure compliance with electromagnetic compatibility in domestic dwellings
and in premises directly connected to a low-voltage power supply system
feeding buildings for domestic use.
EXTRA PRECAUTIONS
- WELDING OPERATIONS:
- In environments with increased riskof electric shock
- In confined spaces
- In the presence of flammable or explosive materials
MUST BE evaluated in advance by an “Expert supervisor” and must always be
carried out in the presence of other people trained to intervene in emergencies.
Technical protection measures MUST BE taken as described in 5.10; A.7; A.9.
of the “IEC TECHNICAL SPECIFICATION or CLC/TS 62081”.
- Welding MUST NOT be allowed if the welding machine or wire feeder is
supported by the operator (e.g. using belts).
- The operator MUST NOT BE ALLOWED to weld in raised positions unless
safety platforms are used.
- VOLTAGE BETWEEN ELECTRODE HOLDERS OR TORCHES: working with
more than one welding machine on a single piece or on pieces that are
connected electrically may generate a dangerous accumulation of no-load
voltage between two different electrode holders or torches, the value of which
may reach double the allowed limit.
An expert coordinator must use measuring instruments to determine the
existence of a risk and should take suitable protection measures as detailed
in 5.9 of the “IEC TECHNICAL SPECIFICATION or CLC/TS 62081”.
CONTINUOUS WIRE WELDING MACHINES FOR MIG-MAG AND FLUX TIG, MMA
ARC WELDING DESIGNED FOR PROFESSIONAL AND INDUSTRIAL USE.
Note: In the following text the term “welding machine” will be used.
1. GENERAL SAFETY CONSIDERATIONS FOR ARC WELDING
The operator should be properly trained to use the welding machine safely
and should be informed about the risks related to arc welding procedures, the
associated protection measures and emergency procedures.
(Refer also to the “IEC TECHNICAL SPECIFICATION or CLC/TS 62081”:
INSTALLATION AND USE OF EQUIPMENT FOR ARC WELDING).
- Avoid direct contact with the welding circuit: the no-load voltage supplied by
the welding machine can be dangerous under certain circumstances.
- When the welding cables are being connected or checks and repairs are
carried out the welding machine should be switched off and disconnected
from the power supply outlet.
- Switch off the welding machine and disconnect it from the power supply
outlet before replacing consumable torch parts.
- Make the electrical connections and installation according to the safety rules
and legislation in force.
- The welding machine should be connected only and exclusively to a power
source with the neutral lead connected to earth.
- Make sure that the power supply plug is correctly connected to the earth
protection outlet.
- Do not use the welding machine in damp or wet places and do not weld in the
rain.
- Do not use cables with worn insulation or loose connections.
- If the welding machine has a liquid cooling unit the filling operations should
be carried out with the welding machine switched off and disconnected from
the power supply outlet.
- Do not weld on containers or piping that contains or has contained flammable
liquid or gaseous products.
- Do not operate on materials cleaned with chlorinated solvents or near such
substances.
- Do not weld on containers under pressure.
- Remove all flammable materials (e.g. wood, paper, rags etc.) from the working
area.
- Provide adequate ventilation or facilities for the removal of welding fumes near
the arc; a systematic approach is needed in evaluating the exposure limits for
the welding fumes, which will depend on their composition, concentration
and the length of exposure itself.
- Keep the gas bottle (if used) away from heat sources, including direct sunlight.
- Use adequate electrical insulation with regard to the electrode, the work piece
and any (accessible) earthed metal parts in the vicinity.
This is normally achieved by wearing gloves, shoes, head coverings and
clothing designed for this purpose and by using insulating platforms or mats.
- Always protect your eyes using masks or helmets fitted with appropriate
lenses.
Use special fire-resistant protective clothing and do not allow the skin to be
exposed to the ultraviolet and infrared rays produced by the arc; other people
in the vicinity of the arc should be protected by shields of non-reflecting
curtains.
- Noise level: If particularly intensive welding operations cause a personal
daily exposure level (LEPd) that is greater than or equal to 85db(A), the use of
suitable personal protectors is compulsory.
ENGLISH
INDEX
1. GENERAL SAFETY CONSIDERATIONS FOR ARC WELDING ...............................5
2. INTRODUCTION AND GENERAL DESCRIPTION ....................................................6
2.1 INTRODUCTION ..................................................................................................6
2.2 METAL WELDABILITY ..........................................................................................6
2.3 STANDARD ACCESSORIES ................................................................................6
2.4 OPTIONAL ACCESSORIES .................................................................................6
3. TECHNICAL DATA .....................................................................................................6
3.1 DATA PLATE .........................................................................................................6
3.2 OTHER TECHNICAL DATA ..................................................................................6
4. DESCRIPTION OF THE WELDING MACHINE ..........................................................6
4.1 CONTROL DEVICES, ADJUSTMENT AND CONNECTION ................................6
4.1.1 Welding machine..........................................................................................6
4.1.2 Wire feeder ..................................................................................................6
4.2 WELDING MACHINE CONTROL PANEL .............................................................6
4.2.1 CONTROL PANEL OF THE WIRE FEEDER ...............................................7
4.3 RECALLING AND STORING PROGRAMS ..........................................................8
4.3.1 RECALLING MANUFACTURER’S PRE-STORED PROGRAMS ...............8
4.3.1.1 MIG-MAG SYNERGIC programs ....................................................8
4.3.1.2 OPERATION IN MANUAL MODE (“PRG 0”) ..................................8
4.3.2 STORING AND RECALLING CUSTOMISED MIG-MAG PROGRAMS ......8
4.3.2.1 Introduction .....................................................................................8
4.3.2.2 Storage capacity for customised MIG-MAG programs ...................8
4.3.2.3 Storage procedure (SAVE) .............................................................8
4.3.2.4 Procedure for recalling a customised program (RECALL) ..............8
5. INSTALLATION ...........................................................................................................8
5.1 PREPARATION .....................................................................................................8
5.2 HOW TO LIFT THE WELDING MACHINE............................................................8
5.3 POSITION OF THE WELDING MACHINE ...........................................................9
5.4 CONNECTION TO THE MAIN POWER SUPPLY ...............................................9
5.4.1 Note .............................................................................................................9
5.4.2 Plug and outlet ............................................................................................9
5.5 CONNECTION OF THE WELDING CABLES ......................................................9
5.5.1 MIG-MAG WIRE WELDING ........................................................................9
5.5.1.1 Connecting the gas bottle ...............................................................9
5.5.1.2 Connecting the torch ......................................................................9
5.5.1.3 Connecting the welding current return cable ..................................9
5.5.2 TIG WELDING ...........................................................................................9
5.5.2.1 Connection to the gas bottle ...........................................................9
5.5.2.2 Connecting the welding current return cable ..................................9
5.5.2.3 Connecting the torch .......................................................................9
5.5.3 MMA WELDING WITH COATED ELECTRODE .........................................9
5.5.3.1 Connecting the electrode-holder clamp ..........................................9
5.5.3.2 Connecting the welding current return cable ..................................9
5.5.4 WARNINGS ................................................................................................9
5.6 LOADING THE WIRE REEL .................................................................................9
5.7 REPLACING THE LINER IN THE TORCH ...........................................................9
5.7.1 Coiled hose for steel wires .........................................................................9
5.7.2 Synthetic hose for aluminium wires ............................................................9
6. WELDING: DESCRIPTION OF THE PROCEDURE ...................................................9
6.1 MIG-MAG WELDING ...........................................................................................9
6.1.1 SHORT ARC TRANSFER MODE...............................................................9
6.1.2 SPRAY ARC TRANSFER MODE .............................................................10
6.1.3 PULSE ARC TRANSFER MODE .............................................................10
6.1.4 ADJUSTING THE WELDING PARAMETERS IN MIG-MAG ....................10
6.1.4.1 Protective gas ...............................................................................10
6.1.4.2 Welding current ............................................................................10
6.1.4.3 Arc voltage and arc pinch-off ........................................................10
6.1.5 BI-LEVEL AND PULSE ON PULSE OPERATION ....................................10
6.2 TIG (DC) WELDING ............................................................................................10
6.2.1 LIFT strike .................................................................................................10
6.3 MMA WELDING WITH COATED ELECTRODES ...............................................10
6.4 WELD QUALITY .................................................................................................10
7. MAINTENANCE ........................................................................................................10
7.1 ROUTINE MAINTENANCE .................................................................................10
7.1.1.Torch ..........................................................................................................10
7.1.2 Wire feeder ...............................................................................................10
7.2 EXTRAORDINARY MAINTENANCE .................................................................11
8. TROUBLESHOOTING ..............................................................................................11
page
page
Содержание INVERPULSE 425
Страница 174: ...174...
Страница 175: ...175 1 a a b b 2 a b c 3 4 200mm 300mm FIG I 1 6 1 6 1 2 1 2...
Страница 176: ...176...
Страница 177: ...177...
Страница 178: ...178 FIG P FIG O B A...