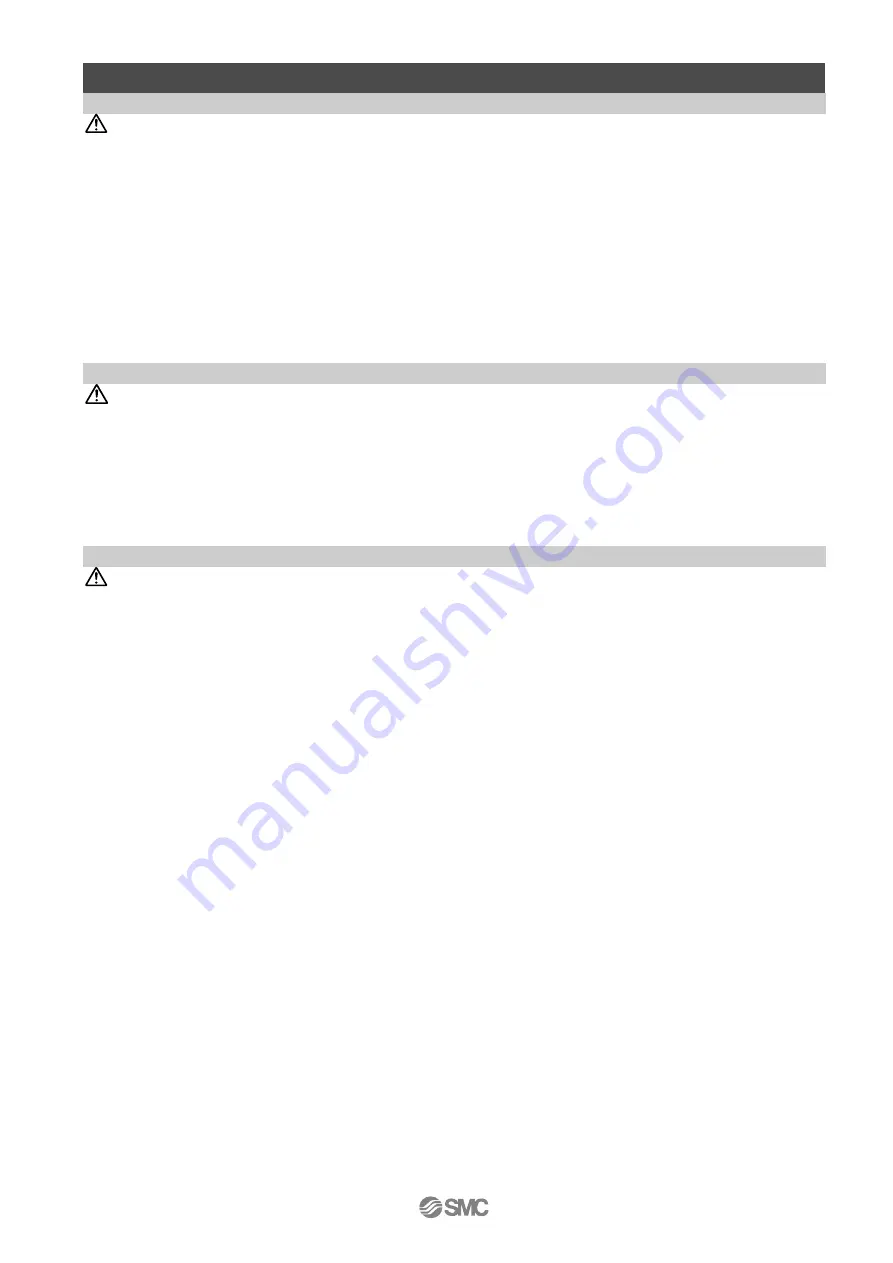
-30-
7. Electric actuators / Rod Type Common precautions
7.1 Design
Warning
1. Do not apply a load in excess of the actuator specification.
A product should be selected based on the maximum work load and allowable moment.
If the product is used outside of the operating specification, eccentric load applied to the guide
will become excessive and have adverse effects such as creating play in the guide, reduced
accuracy and reduced product life.
2. Do not use the product in applications where excessive external force or impact force is
applied to it.
The product can be damaged.
The components including the motor are manufactured to precise tolerances.
So that even a slight deformation may cause faulty operation or seizure.
7.2 Selection
Warning
1. Do not exceed the speed limit of the actuator specification.
Select a suitable actuator by the relationship of allowable work load and speed.
Noise or reduction of accuracy may occur if the actuator is operated in excess of its specification
and could lead to reduced accuracy and reduced product file.
2. When the product repeatedly cycles with partial strokes (100mm), lubrication can run out.
Operate it at a full stroke at least once a day or every 1000 strokes.
7.3 Handling
Caution
1. For thrust control, make sure to set it to "torque control mode", and operate within the
"pushing speed" range of each model.
Do not hit the workpiece or the stroke end with the piston in the "position control mode", "speed
control mode" or "positioning mode". The lead screw, bearing and internal stopper may be
damaged, causing malfunction.
2. When using the thrust control, the following parameter should be set.
- LECSA: The value of the parameter value [PC12] “Internal torque command” should be 30% or
less. (LEY63 : 50% or less)
- LECSB: The value of the parameter value [PC13] “Analog torque maximum output command”
should be 30% or less. (LEY63 : 50% or less)
- LECSS-T: The value of the parameter value [PC13] “Analog torque maximum output command”
should be 24% or less. (LEY63 : 40% or less)
It may lead to breakage and malfunction.
3. Normal/reverse torque limit value is set to 100 % as a default.
It is the maximum torque (the limit value) in the "position control mode", "speed control mode" or
"positioning mode". When the product is operated with a smaller value than the default,
acceleration when driving can decrease. Set it upon confirmation with the actual equipment used.
4. The maximum speed of this actuator varies depending on the stroke of the product.
When selecting a product, check the catalog for the model selection.
5. Do not apply a load, impact or resistance in addition to a transferred load during return to
origin.
Otherwise, the origin can be displaced since it is based on detected motor torque.
6. Do not scratch or gouge the sliding parts of the piston rod, by striking or grasping them
with other objects.
Piston rod is manufactured to precise tolerances, so that even a slight deformation may cause
malfunction.
7. Please connect it so that the impact and load may not be added to the rod from the side
when external guide is used.