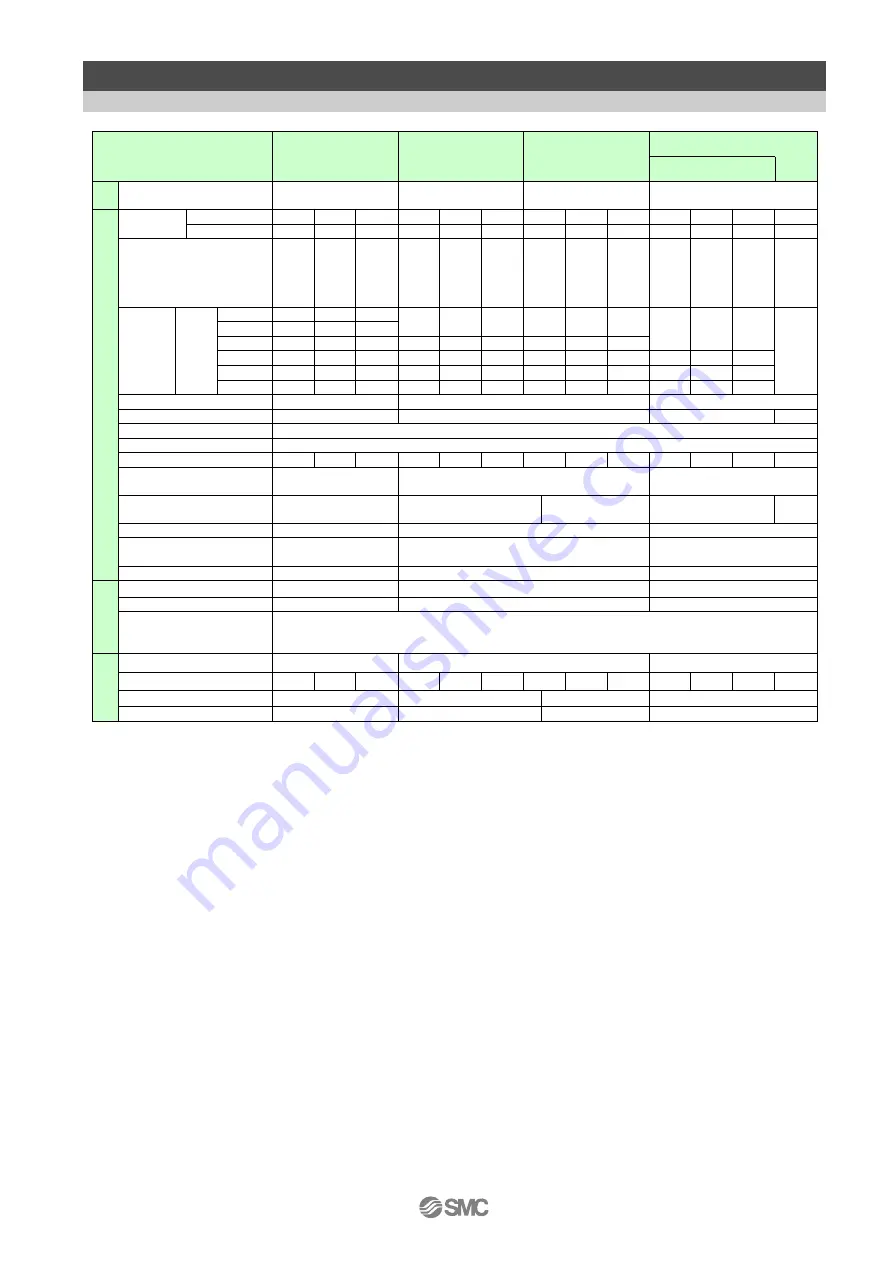
-13-
2. Rod type / LEY Series
2.1
Specification
Model
LEY25* / LEY25D*
(Parallel / In-line)
LEY32*
(Parallel type)
LEY32D*
(In-line type)
LEY63*
(Parallel type)
LEY63D*
(In-line type)
Stroke [mm]
Note1)
30, 50, 100, 150, 200,
250,300, 350, 400
30, 50, 100, 150, 200,
250,300, 350, 400, 500
30, 50, 100, 150, 200,
250,300, 350, 400, 500
100, 200, 300, 400, 500, 600,
700, 800
A
c
tuat
or
s
pec
if
ic
at
ion
Work load
[kg]
Horizontal
Note 2)
18
50
50
30
60
60
30
60
60
40
70
80
200
Vertical
8
16
30
9
19
37
12
24
46
19
38
72
115
Thrust [N]
Note3)
(Set value LEY25/32
:
15 to 30%)
(Set value LEY63
:
15 to 50%)
(Set value LEY25T32T
:
12 to 24%)
(Set value LEY63T
:
12 to 40%)
65
~
131
127
~
255
242
~
485
79
~
157
154
~
308
294
~
588
98
~
197
192
~
385
368
~
736
156
~
521
304
~
1012
573
~
1910
1003
~
3343
Maximum
Speed
Note4)
[mm/s]
Range
of
stroke
to 300
900
450
225
1200
600
300
1000
500
250
1000
500
250
70
305 to 400 600
300
150
405 to 500
-
-
-
800
400
200
640
320
160
505 to 600
-
-
-
-
-
-
-
-
-
800
400
200
605 to 700
-
-
-
-
-
-
-
-
-
600
300
150
705 to 800
-
-
-
-
-
-
-
-
-
500
250
125
Pushing speed [mm/s]
Note5)
35 or less
30 or less
30 or less
acceleration/deceleration [mm/s
2
]
5,000
5,000
5,000
3,000
Positioning repeatability [mm]
±0.02[Basic type] / ±0.01[High precision type]
Lost motion[mm]
0.1 or less[Basic type] / 0.05 or less[High precision type]
Lead[mm] (
Including pulley ratio
)
12
6
3
20
10
5
16
8
4
20
10
5
2.86
Impact resistance/vibration
Resistance [m/s
2
]
Note6)
50 / 20
50 / 20
50 / 20
Drive method
Ball screw and Belt [1:1] / Ball screw
Ball screw and Belt [1.25:1]
Ball screw
Ball screw
Ball screw
and Belt [4:7]
Guide type
Sliding bush (Piston rod part)
Sliding bush (Piston rod part)
Sliding bush (Piston rod part)
Operating temperature range
[
℃
]
5 to 40
5 to 40
5 to 40
Operating humidity range [%RH] 90 or less(No condensation)
90 or less (No condensation)
90 or less (No condensation)
E
le
ct
ric
sp
eci
fica
tio
Motor output/size
100W
/☐
40
200W
/☐
60
400W
/☐
60
Type of Motor
AC servo motor (100/200VAC)
AC servo motor (100/200VAC)
AC servo motor (200VAC)
Encoder
[Type of Motor: S2,S3,S4]: Incremental 17bit encoder (Resolution: 131072 p/rev)
[Type of Moto: S6,S7,S8]: Absolute 18bit encoder (Resolution: 262144 p/rev)
[Type of Moto: T6,T7,T8]: Absolute 22bit encoder (Resolution: 4194304 p/rev)
Lo
ck
sp
eci
fica
tio
n
Type
Note7)
No excitation operating type
No excitation operating type
No excitation operating type
Holding force [N]
131
255
607
607
607
588
197
385
736
313
607
1146
2006
Power consumption [W] at 20
℃
Note8)
6.3
7.9
7.9
7.9
Rated voltage [V]
24VDC
0
-10%
24VDC
0
-10%
DC24
0
-10%
DC24
0
-10%
Note 1) The middle stroke other than the above are produced upon receipt of order.
Note 2) The maximum value of the horizontal workload. (An external guide is necessary[Coefficient of friction:0.1 or less]).
The actual workload will depend on the type of external guide.
Note 3) Thrust setting range when "thrust control" in torque control mode, etc. Set it referring to the thrust conversion graph shown in the
catalog as a guide.
Note 4) The allowable speed changes by the stroke.
Note 5) Allowable impact speed when "impact work" in torque control mode, etc.
Note 6) Impact resistance: No malfunction occurred when the actuator was tested with a drop tester in both an axial direction and perpendicular direction
to the lead screw. (The test was performed with the actuator in the initial state.)
Vibration resistance: No malfunction occurred in a test ranging between 45 to 2000 Hz, when the actuator was tested in both an axial direction
and a perpendicular direction to the lead screw. (The test was performed with the actuator in the initial state.)
Note 7) Only when the motor option, "with lock", is selected.
Note 8) For an actuator with lock, add the power consumption for the lock.