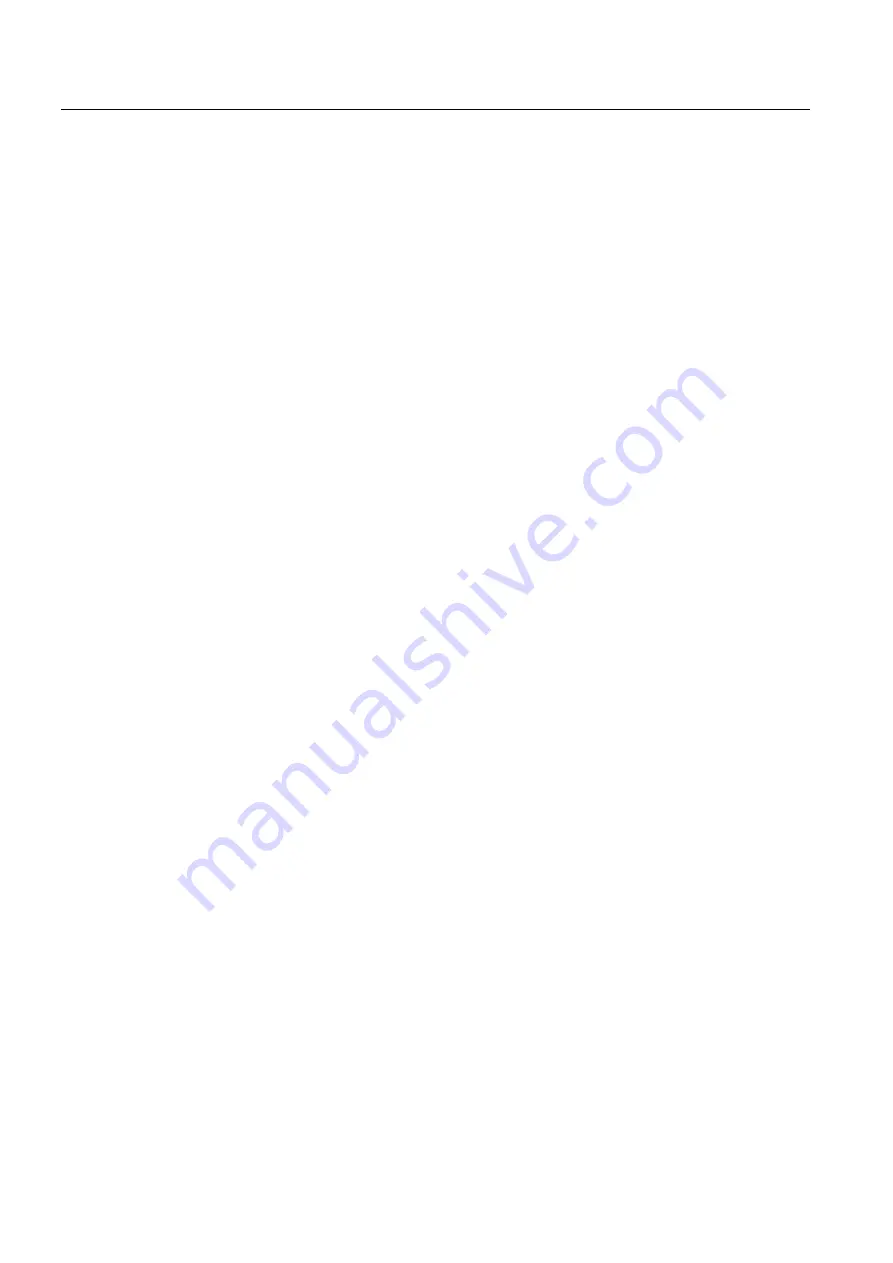
Functions
5.1 Overview of inverter functions
Frequency inverter
82
Operating Instructions, 08.10. 2008, t.b.d.
Functions relevant to all applications
① Inverter control is responsible for all of the other frequency inverter functions. Among
other things, it defines how the inverter responds to external control signals.
② The command source defines whether the motor is powered-up and powered-down
via terminals (digital inputs) or a fieldbus.
③ The setpoint source defines how the speed setpoint is entered, e.g. via terminals
(analog input) or via a fieldbus.
④ The setpoint calculationuses a ramp-function generator to prevent speed steps
occuring and to limit the speed to a permissible maximum value.
⑤ The closed-loop control ensures that the motor follows the speed setpoint. It offers
both V/f control, which is easy to configure, and vector control, which is more
complex.
Functions required in special applications only
⑥ The motor and frequency inverter protection avoids overloads and operating states
that could cause damage to the motor and frequency inverter. The motor temperature
monitoring is, e.g. set here.
⑦ The technological functions allow you to activate a motor holding brake or implement
a higher-level pressure or temperature control using the technology controller, for
example.
⑧ The status messages provide binary and analog signals at the terminals or via the
fieldbus. Examples include the current speed of the motor or fault messages issued
by the inverter.
⑨ A connection to a fieldbus can be established via software tools in the control
systems. How this is carried out with a SIMATIC controller is described in a separate
section.
⑩ The safety functions are only available for fail-safe frequency inverters.