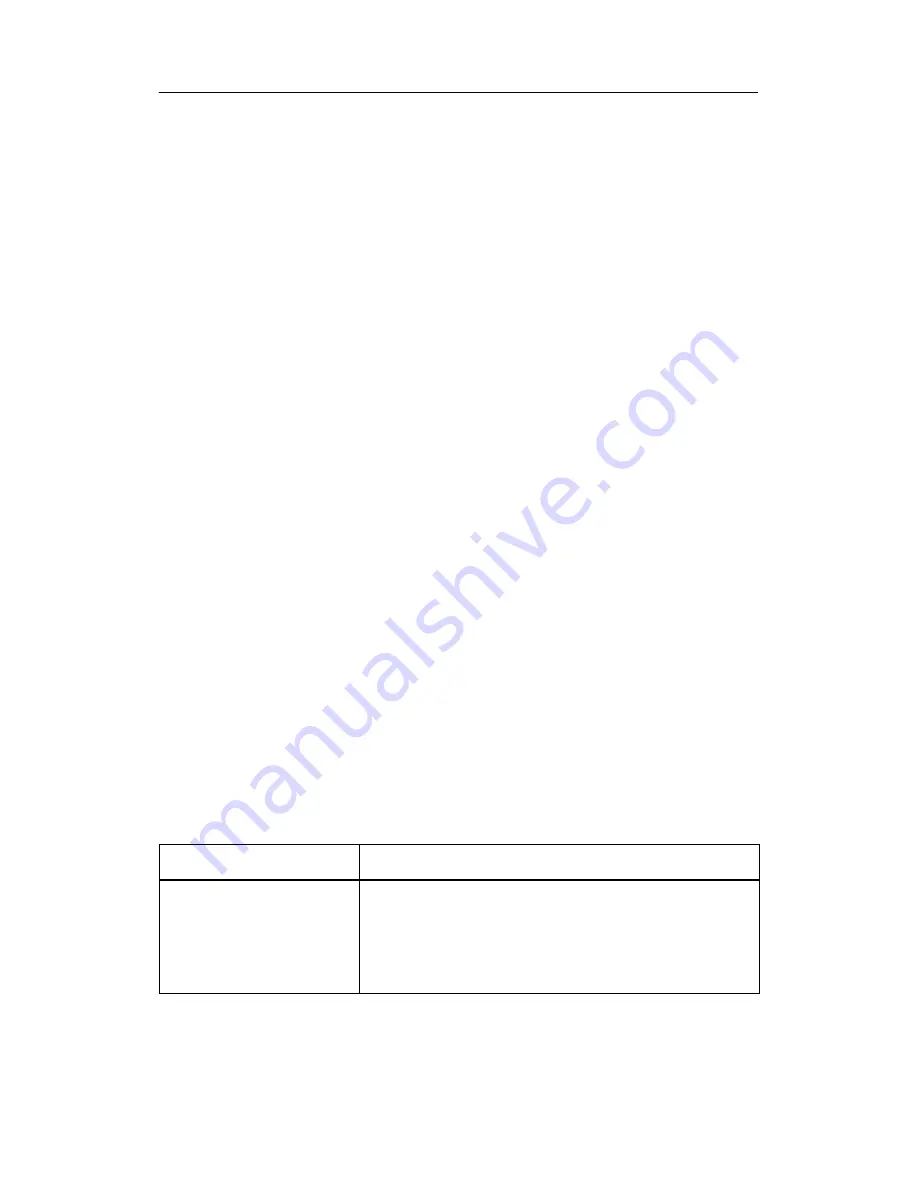
Commissioning
6-17
Automation System S7-400 Hardware and Installation
A5E00850741-01
6.9
Starting Up a PROFIBUS-DP Subnet
Introduction
This section describes the procedure for starting up a PROFIBUS-DP subnet with
an S7-400 CPU as the DP master.
Requirements
Before you can start up the PROFIBUS-DP subnet, the following requirements
must be met:
•
The PROFIBUS-DP subnet has been set up (see Chapter 5).
•
With STEP 7, you have configured the PROFIBUS-DP subnet and assigned a
PROFIBUS-DP address and the address area to all nodes (see manual
Configuring Hardware and Communication Connections with STEP 7
). Note that
for some DP slaves, address switches must also be set (see the reference
manuals for the particular DP slaves).
Starting Up
1. Use the programming device to load the configuration of the PROFIBUS-DP
subnet created under STEP 7 (preset configuration) in the CPU. This procedure
is described in the manual
Configuring Hardware and Communication
Connections with STEP 7
.
2. Switch on all DP slaves.
3. Switch the CPU from STOP to RUN.
Behavior of the CPU During Startup
During startup, the CPU compares the preset and actual configurations. You set
the duration of the test with STEP 7 in the “Startup” parameter block with the
“module time limits” parameter. (See also
Reference Manual
, Chapter 1, the
manual
Configuring Hardware and Communication Connections with STEP 7
, and
the STEP 7 Online Help).
If the preset configuration = actual configuration, the CPU goes into RUN.
If the preset configuration
≠
actual configuration, the CPU’s reaction depends on
the setting of the parameter for “Startup if preset configuration
≠
actual
configuration”:
Startup if Preset Config. Actual
Config. = Yes (Default)
Startup if Preset Config.
≠
Actual Config. = No
CPU goes into RUN
The CPU remains at STOP and, after the timeset in the “module time
limits” parameter, the BUSF LED flashes.
Flashing of the BUSF LED indicates that at least one slave will not
respond. In this case, check whether all slaves are switched on or
display the content of the diagnostic buffer
(see
Configuring Hardware and Communication Connections with
STEP 7
).
Содержание Simatic S7-400
Страница 6: ...Preface vi Automation System S7 400 Hardware and Installation A5E00850741 01 ...
Страница 52: ...Installing the S7 400 2 36 Automation System S7 400 Hardware and Installation A5E00850741 01 ...
Страница 60: ...Addressing the S7 400 3 8 Automation System S7 400 Hardware and Installation A5E00850741 01 ...
Страница 128: ...Networking 5 30 Automation System S7 400 Hardware and Installation A5E00850741 01 ...
Страница 148: ...Commissioning 6 20 Automation System S7 400 Hardware and Installation A5E00850741 01 ...
Страница 228: ...Index Index 4 Automation System S7 400 Hardware and Installation A5E00850741 01 ...